Preparation method of high-density regenerated fibre spinning solution
A technology for regenerating fibers and spinning dope, which is applied in the preparation of spinning solution, man-made filament in cellulose solution, and fiber processing, etc., can solve the problems of spinning liquid leakage, improving dope system, and clogging of spinneret holes, etc. Achieve the effect of removing low-boiling organic solvents
- Summary
- Abstract
- Description
- Claims
- Application Information
AI Technical Summary
Problems solved by technology
Method used
Examples
Embodiment 1
[0020] The composition of the regenerated cellulose fiber spinning dope is: bamboo pulp: N-methylmorpholine oxide containing water with a mass concentration of 13%: the mass ratio of acetone is 25:38:37. Filter the dissolved bamboo pulp spinning stock solution through a candle filter, then feed it into the twin-screw extruder at a speed of 20kg / h, and set the temperature in each area of the screw (from the tail to the head) to 90°C , 90°C, 90°C, 90°C, 90°C, 95°C, 95°C, 95°C, 95°C, the vacuum degree is 0.01Mpa, and the screw speed is 100r / min. After the degassing is completed, take a small sample of the stock solution, and observe with the naked eye and under an optical microscope that there are only 2 small bubbles with a diameter below 0.03 mm. At this time, the mass concentration of the bamboo pulp spinning stock solution is 39.68%.
Embodiment 2
[0022] The composition of the regenerated cellulose fiber spinning stock solution is: the mass ratio of wood pulp:N-methylmorpholine oxide containing water with a mass concentration of 13%:carbon tetrachloride is 20:50:30. Filter the dissolved wood pulp spinning solution through a candle filter, then feed it into the single-screw extruder at a speed of 25kg / h, and set the temperature of each zone in the screw (from the tail to the head) to 90°C , 90°C, 90°C, 90°C, 95°C, 95°C, the vacuum degree is 0.004Mpa, and the screw speed is 200r / min. After the degassing is completed, take a small stock solution sample, and observe with the naked eye and under an optical microscope that there are only 3 small bubbles with a diameter below 0.03 mm. At this time, the mass concentration of the wood pulp spinning stock solution is 28.57%.
Embodiment 3
[0024] The composition of the regenerated cellulose fiber spinning stock solution is: the mass ratio of reed: N-methylmorpholine oxide containing 13% water in mass concentration: chloroform is 10:40:50. Filter the dissolved reed spinning stock solution through a candle filter, and then use a thin film evaporator to defoam, the temperature is 90°C, the vacuum degree is 0.006Mpa, and the rotation speed is 100r / min. After the degassing is completed, take a small stock solution sample, and observe with the naked eye and under an optical microscope that there are only 4 small bubbles with a diameter below 0.03 mm. At this time, the mass concentration of the reed spinning stock solution is 20%.
PUM
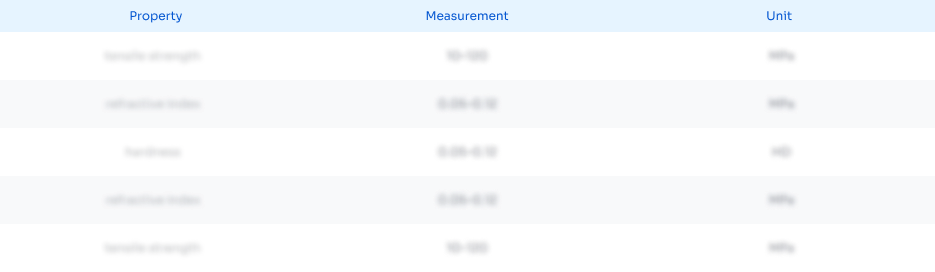
Abstract
Description
Claims
Application Information

- R&D
- Intellectual Property
- Life Sciences
- Materials
- Tech Scout
- Unparalleled Data Quality
- Higher Quality Content
- 60% Fewer Hallucinations
Browse by: Latest US Patents, China's latest patents, Technical Efficacy Thesaurus, Application Domain, Technology Topic, Popular Technical Reports.
© 2025 PatSnap. All rights reserved.Legal|Privacy policy|Modern Slavery Act Transparency Statement|Sitemap|About US| Contact US: help@patsnap.com