Production method of ultrahard high-chromium cast grinding ball
A technology of casting grinding balls and production process, which is applied in the direction of manufacturing tools, quenching agents, heat treatment process control, etc., can solve the problems of complex production process, high chromium casting grinding ball cost increase, large investment in production equipment, etc., and achieve huge social benefits , Reduce the content of precious metal chromium, and reduce the effect of operating costs
- Summary
- Abstract
- Description
- Claims
- Application Information
AI Technical Summary
Problems solved by technology
Method used
Image
Examples
Embodiment 1
[0035] The chemical composition of superhard high chromium cast grinding balls is as follows:
[0036] Carbon (C): 2.98%, Silicon (Si): 0.61%, Manganese (Mn): 0.46%,
[0037] Chromium (Cr): 10.15%, phosphorus (P): 0.052%, sulfur (S): 0.055%;
[0038] Copper (Cu): 0.062%, Molybdenum (Mo): 0.033%, Nickel (Ni): 0.027%,
[0039] Tungsten (W): 0.02%, rare earth yttrium (Y-Re): 0.121%,
[0040] Iron (Fe) 85.43%.
[0041] The manufacturing process of superhard high chromium cast grinding balls is as follows:
[0042] First, the steel scrap is melted in an intermediate frequency induction furnace, and the temperature is raised to 1510-1550°C, and then Cr, Cu, Mo, Ni, W alloys are added to achieve the required chemical composition. Then put the rare earth yttrium into the molten iron ladle, melt it with molten iron and let it stand for 7 minutes, so as to degrade and inoculate the molten iron. The treated molten iron uses casting direct-reading spectrometer to measure its chem...
Embodiment 2
[0050] Superhard high chromium casting grinding ball and its production process
[0051] The chemical composition of superhard high chromium cast grinding balls is as follows:
[0052] Carbon (C): 2.4%, Silicon (Si): 0.62%, Manganese (Mn): 0.32%,
[0053] Chromium (Cr): 10.19%, phosphorus (P): 0.059%, sulfur (S): 0.053%;
[0054] Copper (Cu): 0.041%, Molybdenum (Mo): 0.045%, Nickel (Ni): 0.031%,
[0055] Tungsten (W): 0.017%, rare earth yttrium (Y-Re): 0.128%,
[0056]Iron (Fe) 86.096%.
[0057] The manufacturing process of superhard high chromium cast grinding balls is as follows:
[0058] Firstly, the steel scrap is melted in an intermediate frequency induction furnace, and the temperature is raised to 1520-1560°C, and then Cr, Cu, Mo, Ni, W alloys are added to achieve the required chemical composition. Then put the rare earth yttrium into the molten iron ladle, melt it with the molten iron and let it stand for 6 minutes to carry out the modification and inoculati...
Embodiment 3
[0066] Superhard high chromium casting grinding ball and its production process
[0067] The chemical composition of superhard high chromium cast grinding balls is as follows:
[0068] Carbon (C): 2.12%, Silicon (Si): 0.59%, Manganese (Mn): 0.47%,
[0069] Chromium (Cr): 10.25%, phosphorus (P): 0.041%, sulfur (S): 0.043%;
[0070] Copper (Cu): 0.052%, Molybdenum (Mo): 0.032%, Nickel (Ni): 0.029%,
[0071] Tungsten (W): 0.023%, rare earth yttrium (Y-Re): 0.13%,
[0072] Iron (Fe) 86.22%.
[0073] The manufacturing process of superhard high chromium cast grinding balls is as follows:
[0074] Firstly, the steel scrap is melted in an intermediate frequency induction furnace, and the temperature is raised to 1540-1580°C, and then Cr, Cu, Mo, Ni, W alloys are added to achieve the required chemical composition. Then put the rare earth yttrium into the molten iron ladle, melt it with the molten iron and let it stand for 5 minutes to carry out the modification and inoculati...
PUM
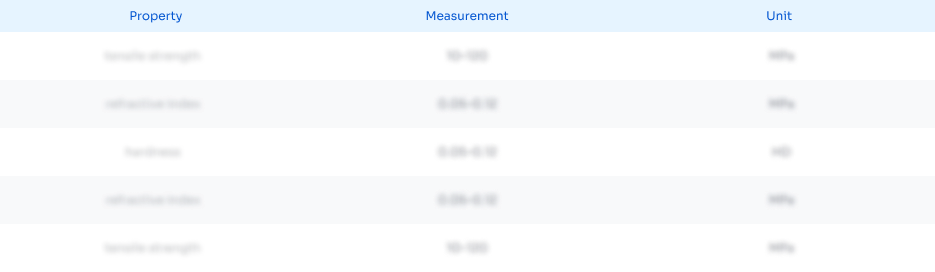
Abstract
Description
Claims
Application Information

- Generate Ideas
- Intellectual Property
- Life Sciences
- Materials
- Tech Scout
- Unparalleled Data Quality
- Higher Quality Content
- 60% Fewer Hallucinations
Browse by: Latest US Patents, China's latest patents, Technical Efficacy Thesaurus, Application Domain, Technology Topic, Popular Technical Reports.
© 2025 PatSnap. All rights reserved.Legal|Privacy policy|Modern Slavery Act Transparency Statement|Sitemap|About US| Contact US: help@patsnap.com