Copper-zinc-nickel-cobalt-indium alloy and preparation method thereof
A technology of indium alloy and copper-zinc-nickel, which is applied in the field of copper-zinc-nickel-cobalt-indium alloy and its manufacturing, can solve the problems of cemented carbide oxidation heat stress, hard alloy decobalt, high melting temperature, etc. Effects of cobalt, low brazing temperature, and low melting temperature
- Summary
- Abstract
- Description
- Claims
- Application Information
AI Technical Summary
Problems solved by technology
Method used
Examples
Embodiment 1
[0026] a, by weight percentage: Cu: 46%; Zn: 40%; Ni: 11%; Co: 1%; In: 0.8%; Mn: 0.6%; Si: 0.15%; Sn: 0.4%; Re mixed with lanthanum La in a weight ratio of 2:3: 0.05%;
[0027] B, high-melting point metal nickel Ni, cobalt Co are melted into master alloy A1, A2 with copper Cu respectively; Described master alloy A1 is made up of Cu50:Ni50 of weight ratio; Described master alloy A2 is made of Cu70 of weight ratio: Composition of Co30;
[0028] c, deoxidizing element silicon Si, manganese Mn are smelted into master alloy B1, B2 respectively with copper Cu in vacuum furnace; Described master alloy B1 is made up of Cu83:Si17 of weight ratio; Described master alloy B2 is made of weight ratio Composition of Cu70:Mn30;
[0029] d, smelting easily oxidizable metal Re and copper Cu in a vacuum furnace to form an intermediate alloy C; the weight ratio of the copper Cu to Re is 80:20;
[0030] e. After melting the remaining amount of copper Cu in the intermediate frequency furnace, wh...
Embodiment 2
[0036] Take by weight percentage: Cu: 49%; Zn: 38%; Ni: 10%; Co: 1%; In: 0.8%; Mn: 0.7%; Si: 0.15%; Ag: 0.3%; Re: 0.05% in which La is mixed in a weight ratio of 2:3.
Embodiment 3
[0038] Take by weight percentage: Cu: 52%; Zn: 38%; Ni: 8%; Co: 0.8%; In: 0.3%; Mn: 0.2%; Si: 0.15%; Sn: 0.5%; Re: 0.05% in which La is mixed in a weight ratio of 2:3.
PUM
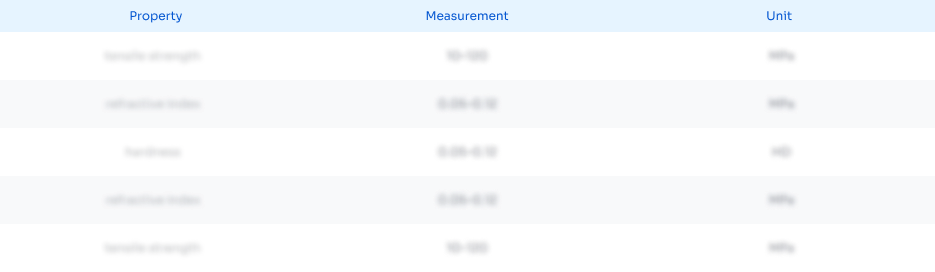
Abstract
Description
Claims
Application Information

- Generate Ideas
- Intellectual Property
- Life Sciences
- Materials
- Tech Scout
- Unparalleled Data Quality
- Higher Quality Content
- 60% Fewer Hallucinations
Browse by: Latest US Patents, China's latest patents, Technical Efficacy Thesaurus, Application Domain, Technology Topic, Popular Technical Reports.
© 2025 PatSnap. All rights reserved.Legal|Privacy policy|Modern Slavery Act Transparency Statement|Sitemap|About US| Contact US: help@patsnap.com