Preparation method of anode catalyst for water electrolysis reaction
A catalyst and water electrolysis technology, applied in the direction of electrodes, electrolysis process, electrolysis components, etc., can solve the problems of restricting the use of catalysts, low amount of deposited catalytic layer, low current density, etc., to achieve shortened preparation time, simple preparation process, high current effect of density
- Summary
- Abstract
- Description
- Claims
- Application Information
AI Technical Summary
Problems solved by technology
Method used
Image
Examples
Embodiment 1
[0027] In 0.1M cobalt nitrate solution, under ultrasonic stirring, 0.1M potassium phosphate solution (solution pH value is 9) was added dropwise at a rate of 5 mL / min, and ultrasonically stirred evenly. The suspension was filtered, the filter cake was washed with deionized water, and dried overnight at 80°C. Mix the obtained powder with isopropanol, disperse the slurry uniformly by ultrasonic, and spray it on the ITO conductive glass. The conductive glass was put into 0.1M potassium phosphate buffer solution with a pH value of 7 for electrolytic activation, with a constant voltage of 1.29V for 3 hours. After drying at room temperature, the obtained cobalt-phosphorus catalyst was soaked in 1M KOH solution and transferred from the ITO conductive glass, and dried overnight at 70°C. The cobalt phosphorus catalyst is tested by a transmission electron microscope, and the result shows that its morphology is a porous ball with a particle diameter of 1-2 μm, and there are many pores o...
Embodiment 2
[0031] Into a mixed solution of 0.1M ferrous sulfate and 0.1M nickel sulfate, under ultrasonic stirring, 0.1M potassium hydroxide solution (pH value of the solution is 10) was added dropwise, and ultrasonically stirred evenly. The suspension was filtered, the filter cake was washed with deionized water, and dried overnight at 70°C. Mix the obtained powder with the alkaline polymer electrolyte membrane solution, and disperse the slurry uniformly by ultrasonic to form a membrane electrode, assemble it into an electrolytic cell, pass distilled water at a speed of 7mL / min, and conduct electrolytic activation at a constant voltage of 2.2V. 3 hours. The membrane electrode made of this nickel-iron catalyst can reach a current density of 120mA / cm in an electrolytic cell at a voltage of 1.8V 2 .
Embodiment 3
[0033]In 0.1M cobalt sulfate solution, under ultrasonic stirring, 0.5M potassium phosphate buffer solution (pH value is 9) was added dropwise, and ultrasonically stirred evenly. The suspension was filtered, the filter cake was washed with deionized water, and dried overnight at 80°C. The prepared solid powder was mixed with isopropanol, the slurry was ultrasonically dispersed, and sprayed onto glassy carbon. The glassy carbon was put into 0.2M potassium phosphate buffer solution with a pH value of 9 for electrolytic activation with a constant voltage of 1.69V for 3 hours. After drying at room temperature, the obtained cobalt-phosphorous catalyst was soaked in 1M KOH solution and transferred from glassy carbon, filtered, and dried overnight at 60°C.
PUM
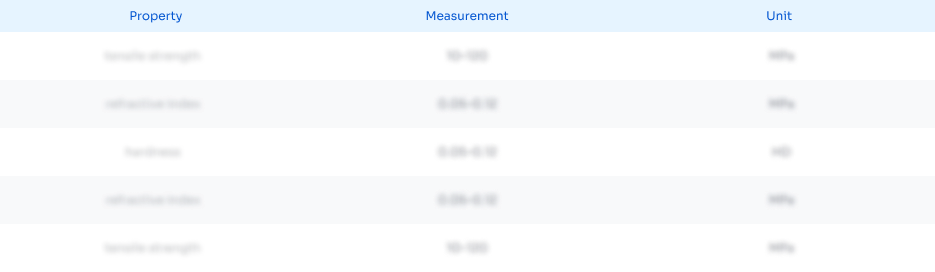
Abstract
Description
Claims
Application Information

- R&D
- Intellectual Property
- Life Sciences
- Materials
- Tech Scout
- Unparalleled Data Quality
- Higher Quality Content
- 60% Fewer Hallucinations
Browse by: Latest US Patents, China's latest patents, Technical Efficacy Thesaurus, Application Domain, Technology Topic, Popular Technical Reports.
© 2025 PatSnap. All rights reserved.Legal|Privacy policy|Modern Slavery Act Transparency Statement|Sitemap|About US| Contact US: help@patsnap.com