Magnesium alloy phosphorization solution and magnesium alloy surface treatment method
A magnesium alloy and solution technology, which is applied in the coating process of metal materials, etc., can solve the problems of high surface resistance of magnesium alloy, low surface phosphating film binding force, poor surface phosphating film binding force, etc., and achieve low surface resistance , good bonding force, high corrosion resistance effect
- Summary
- Abstract
- Description
- Claims
- Application Information
AI Technical Summary
Problems solved by technology
Method used
Examples
Embodiment 1
[0022] This embodiment is used to illustrate the phosphating solution and the magnesium alloy surface treatment method of the present invention.
[0023] 1. Thermal degreasing
[0024] Dissolve sodium pyrophosphate, sodium carbonate, sodium silicate, sodium hydroxide and sodium lauryl sulfate in deionized water to prepare a thermal degreasing solution, which contains 3 g / L sodium pyrophosphate, 3 g / L sodium carbonate, silicon NaOH 3 g / L, Sodium Hydroxide 3 g / L and Sodium Lauryl Sulfate 0.2 g / L.
[0025] The above solution was heated to 40°C. Then, the AZ91D magnesium alloy casting (Nanjing Yunhai Special Metals Co., Ltd.) with a size of 10 × 4 × 0.5 cm is completely immersed in the solution, and the temperature of the solution is kept at 40° C. After soaking for 2 minutes, the magnesium alloy casting is taken out and used Rinse with deionized water until no hydroxide ions are detected.
[0026] 2. Activation
[0027] Lactic acid, boric acid and tartaric acid were dissolved...
Embodiment 2
[0037] This embodiment is used to illustrate the phosphating solution and the magnesium alloy surface treatment method of the present invention.
[0038] Treat the magnesium alloy according to the same method as in Example 1, the difference is that step 4 is: phosphoric acid, calcium dihydrogen phosphate, polyethylene glycol, sodium silicate, sodium molybdate and ammonium metavanadate are dissolved in deionized water Prepare a phosphating solution containing 0.1 mole / liter of phosphoric acid, 20 grams / liter of calcium dihydrogen phosphate, 10 grams / liter of polyethylene glycol, 2 grams / liter of sodium silicate, 4 grams / liter of sodium molybdate and metavanadic acid Ammonium is 0.8 g / L, and the pH value of the solution is adjusted to 2.8 with 5 mol / L sodium hydroxide solution; the temperature of the phosphating solution is 45° C., and the soaking time is 40 seconds. The obtained magnesium alloy is designated as A2.
Embodiment 3
[0040] This embodiment is used to illustrate the phosphating solution and the magnesium alloy surface treatment method of the present invention.
[0041] The magnesium alloy is processed according to the same method as in Example 1, and the difference is that step 4 is: dissolving phosphoric acid, calcium dihydrogen phosphate, hexamethylenetetramine, tartaric acid, sodium silicate, sodium molybdate and ammonium metavanadate Prepare phosphating solution in deionized water, which contains phosphoric acid 0.08 mol / L, calcium dihydrogen phosphate 30 g / L, hexamethylenetetramine 1 g / L, tartaric acid 5 g / L, sodium silicate 1.5 g / L , sodium molybdate 2.5 g / liter and ammonium metavanadate 0.5 g / liter, the pH value of this solution is adjusted to 3 with 5 moles / liter of sodium hydroxide solution; the temperature of the phosphating solution is 50°C, and the soaking time is 20 seconds. The obtained magnesium alloy is designated as A3.
PUM
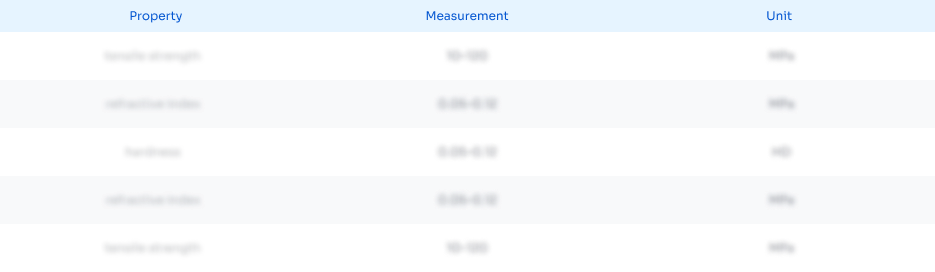
Abstract
Description
Claims
Application Information

- Generate Ideas
- Intellectual Property
- Life Sciences
- Materials
- Tech Scout
- Unparalleled Data Quality
- Higher Quality Content
- 60% Fewer Hallucinations
Browse by: Latest US Patents, China's latest patents, Technical Efficacy Thesaurus, Application Domain, Technology Topic, Popular Technical Reports.
© 2025 PatSnap. All rights reserved.Legal|Privacy policy|Modern Slavery Act Transparency Statement|Sitemap|About US| Contact US: help@patsnap.com