High-density ultra-strength petroleum compression fracture proppant and preparation method thereof
A fracturing proppant and petroleum technology, which is applied in the direction of earthwork drilling, production fluid, wellbore/well components, etc., can solve the problems of land occupation, environmental pollution, etc., and achieve the goal of saving resources, increasing oil production, and good practical prospects Effect
- Summary
- Abstract
- Description
- Claims
- Application Information
AI Technical Summary
Problems solved by technology
Method used
Image
Examples
Embodiment 1
[0032] A petroleum fracturing proppant, the raw materials are as follows in mass parts: 90 parts of waste alumina adsorbent, 2 parts of titanium oxide, 1 part of talc, 1 part of barium carbonate, and 6 parts of ceramic clay.
[0033] 1. Add 90 parts of waste alumina adsorbent powder, 2 parts of titanium oxide, 1 part of talc, 1 part of barium carbonate and 6 parts of ceramic clay into the ball mill, and add 0.3% of the total weight of raw materials as a ball milling aid tripolyphosphoric acid Sodium, add water and ball mill for 10-12 hours to obtain a uniform slurry. The solid content of the slurry is 60wt%.
[0034] 2. Dry and granulate the slurry prepared in step 1 in a spray drying tower to obtain a powder;
[0035] 3. Form the powder obtained in step 2 into a semi-finished proppant with a particle size of 30-50 mesh on a sugar-coated ball forming machine;
[0036] 4. Dry the semi-finished product obtained in step 3, and burn it in a shuttle kiln at a temperature of 1580°...
Embodiment 2
[0038] 1. Add 86 parts of waste alumina adsorbent powder, 2 parts of titanium oxide, 1 part of light calcium carbonate, 1 part of talc, 2 parts of manganese oxide and 8 parts of ceramic clay to the ball mill, and add 0.3% of the total weight of raw materials Sodium tripolyphosphate as a ball milling aid, add water and ball mill for 10-12 hours to obtain a uniform slurry. The solid content of the slurry is 60wt%.
[0039] 2. Dry and granulate the slurry prepared in step 1 in a spray drying tower to obtain a powder with a certain particle size;
[0040] 3. Form the powder obtained in step 2 into a semi-finished proppant with a particle size of 20-40 mesh on a sugar-coated ball forming machine;
[0041] 4. Dry the semi-finished product obtained in step 3, and burn it in a tunnel kiln at a temperature of 1500°C. The fired proppant is milled in a ball mill with water for 2 hours, and then dried to obtain a smooth-surfaced oil fracturing proppant product.
Embodiment 3
[0042] Example 3: A petroleum fracturing proppant, the mass percentage of raw materials is as follows: 92 parts of waste alumina adsorbent, 1 part of titanium oxide, 2 parts of dolomite, and 5 parts of ceramic clay. The preparation steps are the same as in Example 1.
PUM
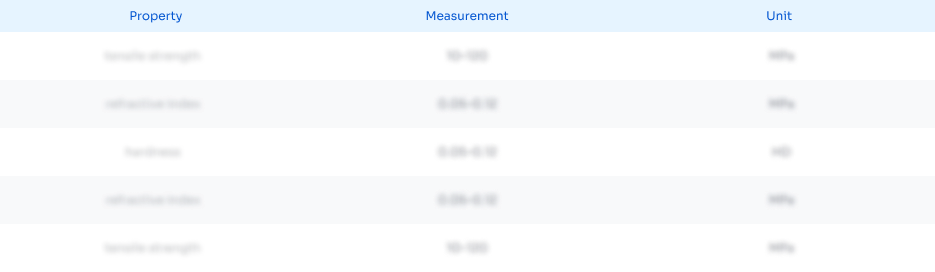
Abstract
Description
Claims
Application Information

- R&D
- Intellectual Property
- Life Sciences
- Materials
- Tech Scout
- Unparalleled Data Quality
- Higher Quality Content
- 60% Fewer Hallucinations
Browse by: Latest US Patents, China's latest patents, Technical Efficacy Thesaurus, Application Domain, Technology Topic, Popular Technical Reports.
© 2025 PatSnap. All rights reserved.Legal|Privacy policy|Modern Slavery Act Transparency Statement|Sitemap|About US| Contact US: help@patsnap.com