Terylene middle strength filament oil solution and production method thereof
A polyester and oil preparation technology, which is applied in the field of polyester medium-strength oil preparation and its manufacturing, can solve the problems of increasing the strength of wool and stiff yarn, peculiar smell, etc. Effect
- Summary
- Abstract
- Description
- Claims
- Application Information
AI Technical Summary
Problems solved by technology
Method used
Examples
Embodiment 1
[0017] Determine the proportion of each component by weight ratio:
example 1
[0019] 78 parts of polyethers, including 34 parts of lauryl alcohol random polyether and 44 parts of propylene glycol block polyether;
[0020] 10 parts of emulsifier, including 6 parts of nonylphenol polyoxyethylene ether (TX type) and 4 parts of lauric acid polyoxyethylene ether (LAE type);
[0021] 7 parts of antistatic agent, including 3 parts of C12-14 alcohol phosphate polyoxyethylene ether potassium salt, 4 parts of nonylphenol polyoxyethylene phosphate potassium salt;
[0022] 5 parts of additives, including 4.5 parts of modified silicone, 0.25 parts of preservative, and 0.25 parts of defoamer.
example 2
[0024] 83 parts of polyethers, including 30 parts of dodecanol random polyether, 10 parts of butanol random polyether, and 43 parts of propylene glycol block polyether;
[0025] 8 parts of emulsifier, including 5 parts of nonylphenol polyoxyethylene ether (TX type), C 12-14 3 parts of alcohol polyoxyethylene ether (MOA class);
[0026] 5 parts of antistatic agent, including 2 parts of C12-14 alcohol phosphate polyoxyethylene ether potassium salt, 3 parts of amphoteric phosphate amine salt;
[0027] 4 parts of additives, including 2 parts of hydrophilic silicone oil, 1 part of preservative, and 1 part of higher alcohol.
PUM
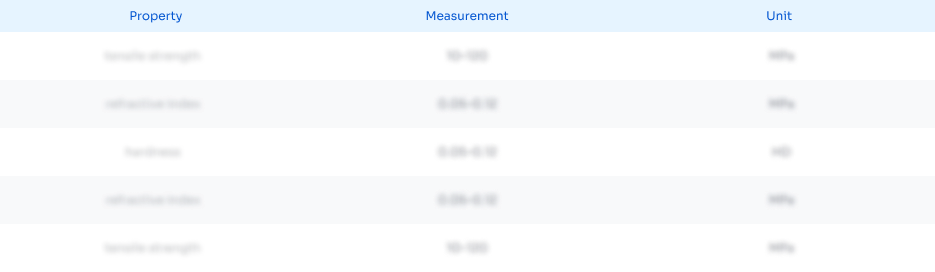
Abstract
Description
Claims
Application Information

- R&D
- Intellectual Property
- Life Sciences
- Materials
- Tech Scout
- Unparalleled Data Quality
- Higher Quality Content
- 60% Fewer Hallucinations
Browse by: Latest US Patents, China's latest patents, Technical Efficacy Thesaurus, Application Domain, Technology Topic, Popular Technical Reports.
© 2025 PatSnap. All rights reserved.Legal|Privacy policy|Modern Slavery Act Transparency Statement|Sitemap|About US| Contact US: help@patsnap.com