Heat-resisting steel flux-cored wire
A technology of flux-cored welding wire and heat-resistant steel, applied in welding medium, welding equipment, welding equipment and other directions, can solve the problems of increased oxygen content of weld metal, decreased toughness of weld metal, and limited use environment, and achieves improvement of metal Toughness, improved oxidation resistance and thermal strength, easy-to-use effects
- Summary
- Abstract
- Description
- Claims
- Application Information
AI Technical Summary
Problems solved by technology
Method used
Examples
Embodiment 1
[0033] A low-carbon steel strip of 0.8×12mm (thickness×width) is selected and rolled into a U shape by a forming machine. Take 1000 grams of mixed material as an example: take 230 grams of rutile, 15 grams of wollastonite, 190 grams of silicon manganese alloy, 85 grams of iron powder, 15 grams of nickel powder, 25 grams of cryolite, 71 grams of feldspar, 130 grams of ferrochrome, 60 grams of ferromolybdenum, 60 grams of medium-carbon ferromanganese, 27 grams of magnesia, 61 grams of quartz, 5 grams of fluorite, 15 grams of aluminum-magnesium alloy, and 11 grams of ferro-titanium (the particle size of the powder obtained can pass through a 60-mesh sieve). Put the various powders taken into the powder mixer and mix for 40 minutes, then add the mixed powder into the U-shaped groove of the low-carbon steel belt, and the filling rate is 17%; close the U-shaped groove to wrap the powder in it; then pass The wire drawing machine draws and reduces the diameter step by step from a diam...
Embodiment 2
[0036] A low-carbon steel strip of 0.8×12mm (thickness×width) is selected and rolled into a U shape by a forming machine. Take 1000 grams of mixed materials as an example: take 215 grams of rutile, 19 grams of wollastonite, 200 grams of silicon-manganese alloy, 86 grams of iron powder, 17 grams of nickel powder, 25 grams of cryolite, 70 grams of feldspar, and 130 grams of ferrochrome. 60 grams of ferromolybdenum, 60 grams of medium-carbon ferromanganese, 25 grams of magnesia, 65 grams of quartz, 5 grams of fluorite, 15 grams of aluminum-magnesium alloy, and 8 grams of ferrotitanium (the particle size of the obtained powder is to pass through a 60-mesh sieve). Put the various powders taken into the powder mixer and mix for 40 minutes, then add the mixed powder into the U-shaped groove of the low-carbon steel belt, and the filling rate is 16%; close the U-shaped groove to wrap the powder in it; then pass The wire drawing machine draws and reduces the diameter step by step from a...
Embodiment 3
[0039] A low-carbon steel strip of 0.8×12mm (thickness×width) is selected and rolled into a U shape by a forming machine. Take 1000 grams of mixed materials as an example: take 210 grams of rutile, 25 grams of wollastonite, 190 grams of silicon manganese alloy, 90 grams of iron powder, 20 grams of nickel powder, 25 grams of cryolite, 70 grams of feldspar, 135 grams of ferrochrome, 60 grams of ferromolybdenum, 60 grams of medium-carbon ferromanganese, 30 grams of magnesia, 60 grams of quartz, 5 grams of fluorite, 15 grams of aluminum-magnesium alloy, and 5 grams of ferro-titanium (the particle size of the powder obtained can pass through a 60-mesh sieve). The various powders that are taken are put into the powder mixer and mixed for 40 minutes, then the mixed powder is added into the U-shaped groove of the low-carbon steel strip, the filling rate is 18%, the U-shaped groove is closed, and the powder is wrapped therein. Then, the flux-cored welding wire of the present invention ...
PUM
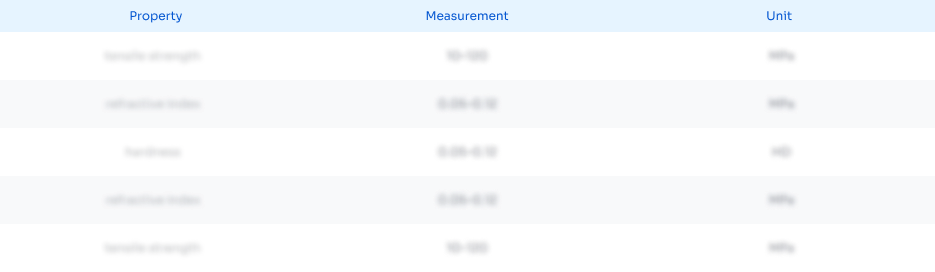
Abstract
Description
Claims
Application Information

- R&D
- Intellectual Property
- Life Sciences
- Materials
- Tech Scout
- Unparalleled Data Quality
- Higher Quality Content
- 60% Fewer Hallucinations
Browse by: Latest US Patents, China's latest patents, Technical Efficacy Thesaurus, Application Domain, Technology Topic, Popular Technical Reports.
© 2025 PatSnap. All rights reserved.Legal|Privacy policy|Modern Slavery Act Transparency Statement|Sitemap|About US| Contact US: help@patsnap.com