Flame retardant and use thereof in polymer modification
A flame retardant and polymer technology, applied in the field of flame retardant and its application in polymer modification, can solve the problems of poor dispersion, poor affinity, affecting the processing performance and mechanical properties of polymer materials, etc. , to achieve the effect of improving compatibility, improving dispersibility, processing performance and mechanical properties
- Summary
- Abstract
- Description
- Claims
- Application Information
AI Technical Summary
Problems solved by technology
Method used
Image
Examples
Embodiment 1
[0017] Put 10000g of magnesium hydroxide, 500g of stearic acid, 500g of zinc borate and 500g of KH-560 silane coupling agent into a high temperature mixing kettle, heat up to 80±5℃, stir at high speed for 20-30 minutes to obtain the flame retardant .
Embodiment 2
[0019] 3250g of the flame retardant obtained in Example 1 was blended uniformly with 1750g of low density polyethylene in a high-speed mixer. Then extrude on a twin-screw extruder with an extrusion temperature of 180°C, water cooling, and pelletizing to obtain a flame-retardant polyethylene material. The mechanical properties and flame-retardant properties are shown in Table 1.
Embodiment 3
[0021] Combine 10,000 g of magnesium hydroxide, 500 g of stearic acid, 500 g of zinc borate and 500 g of KH-570 silane coupling agent, heat up to 80±5° C., stir at high speed for 20-30 minutes to obtain a flame retardant.
PUM
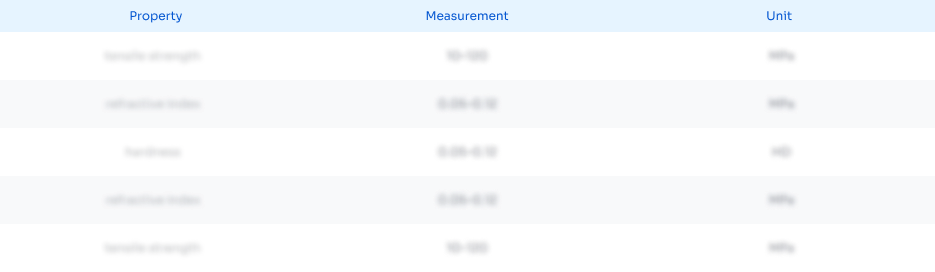
Abstract
Description
Claims
Application Information

- R&D
- Intellectual Property
- Life Sciences
- Materials
- Tech Scout
- Unparalleled Data Quality
- Higher Quality Content
- 60% Fewer Hallucinations
Browse by: Latest US Patents, China's latest patents, Technical Efficacy Thesaurus, Application Domain, Technology Topic, Popular Technical Reports.
© 2025 PatSnap. All rights reserved.Legal|Privacy policy|Modern Slavery Act Transparency Statement|Sitemap|About US| Contact US: help@patsnap.com