Process for preparing dimethyl sulfate by discontinuous process
A technology of dimethyl sulfate and batch method, which is applied in the preparation of sulfate, organic chemistry and other directions, can solve the problems of methanol market fluctuation and high raw material prices, and achieve the effects of low operating costs, lower energy consumption, and lower consumption.
- Summary
- Abstract
- Description
- Claims
- Application Information
AI Technical Summary
Problems solved by technology
Method used
Image
Examples
Embodiment 1
[0032] Such as figure 1 The process flow shown, weigh 0.2gI 2 , and place it in the autoclave, according to I:SO 3 The molar ratio is 1:430. Measure 30ml of liquid sulfur trioxide with a measuring cylinder, place it in the autoclave, and seal the autoclave. Replace the air in the autoclave three times with argon, then feed Ar-containing methane gas (argon volume percentage is 5%) in the autoclave until the pressure in the autoclave is 3 MPa, heat the autoclave to 175 ° C, stop the reaction after 180 min, and wait for The still temperature is down to room temperature, and its gas phase composition is measured by gas chromatography. After measuring, the gas in the still is emptied, and the still is opened, and the reaction solution therein is poured out and carried out underpressure distillation to obtain dimethyl sulfate, such as figure 2 measured. Depend on image 3 , Figure 4 Determination and calculation showed that the gas-phase methane conversion rate was 47.80%, an...
Embodiment 2
[0034] Weigh 0.3gI 2 , and place it in the autoclave, according to I:SO 3 The molar ratio is 1:288. Measure 30ml of liquid sulfur trioxide with a measuring cylinder, place it in the autoclave, and seal the autoclave. Replace the air in the autoclave three times with argon, then feed Ar-containing methane gas into the autoclave (the volume percentage of argon is 5%) until the pressure in the autoclave is 2 MPa, heat the autoclave to 130 ° C, and stop the reaction after 150 min. The temperature of the kettle was lowered to room temperature, and its gas phase composition was measured by gas chromatography. After the measurement, the gas in the kettle was emptied, and the kettle was opened, and the reaction solution therein was poured out for rectification under reduced pressure. The gas-phase methane conversion rate was measured to be 59.94%, and the yield of dimethyl sulfate was 94.07%.
Embodiment 3
[0036] Take by weighing 0.35g sodium iodide, and it is placed in autoclave, according to I: SO 3 The molar ratio is 1:288, and 17.5 L of gaseous sulfur trioxide is introduced into the autoclave, and the autoclave is sealed. Replace the air in the autoclave with argon three times, then feed Ar-containing civil natural gas (5% by volume of argon) into the autoclave until the pressure in the autoclave is 2MPa, heat the autoclave to 160°C, and stop the reaction after 3min. The temperature of the kettle is lowered to room temperature, and its gas phase composition is measured by gas chromatography. After the measurement, the gas in the kettle is emptied, and the kettle is opened, and the reaction solution therein is poured out for ordinary distillation. The gas-phase methane conversion rate was measured to be 32.37%, and the yield of dimethyl sulfate was 97.71%.
PUM
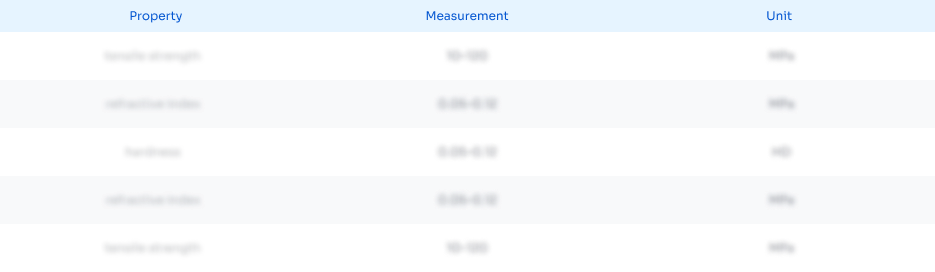
Abstract
Description
Claims
Application Information

- R&D Engineer
- R&D Manager
- IP Professional
- Industry Leading Data Capabilities
- Powerful AI technology
- Patent DNA Extraction
Browse by: Latest US Patents, China's latest patents, Technical Efficacy Thesaurus, Application Domain, Technology Topic, Popular Technical Reports.
© 2024 PatSnap. All rights reserved.Legal|Privacy policy|Modern Slavery Act Transparency Statement|Sitemap|About US| Contact US: help@patsnap.com