Preparation method of prealloy powder for nano level oxide dispersion strengthened metal
A nano-scale oxide and pre-alloyed powder technology, which is applied in the field of pre-alloyed powder for preparing nano-scale oxide dispersion-strengthened metals, can solve the problems of not meeting high performance requirements, uneven dispersion, and difficult control The effect of good consistency, reduced defects, and low cost
- Summary
- Abstract
- Description
- Claims
- Application Information
AI Technical Summary
Problems solved by technology
Method used
Examples
Embodiment 1
[0021] Example 1: 1.0% alumina dispersion strengthened iron-based alloy
[0022] 1) Weigh 108 grams of analytically pure citric acid, dissolve it in deionized water, and configure it into a 1000ml solution;
[0023] 2) Weigh the analytically pure Fe(NO 3 ) 3 .9H 2 O 202 g, Al(NO 3 ) 3 .9H 2 O 4.2 grams, dissolve in the citric acid aqueous solution;
[0024] 3) Add 11 grams of ethylene glycol as a dispersant, and slowly add ammonia water dropwise under magnetic stirring to adjust the pH value of the solution to 6;
[0025] 4) Put it into a water bath at 80°C for constant temperature heating and evaporation to form a sol;
[0026] 5) After the gel is formed, put it in an oven for drying at 100°C to obtain a xerogel, and then bake it in a muffle furnace at 500°C to obtain a super gel.
[0027] Fine oxide mixed powder;
[0028] 6) reducing the above-mentioned calcined oxide in a hydrogen flow at 500° C. for 60 minutes to obtain iron powder dispersed in nano-alumina;
[0...
Embodiment 2
[0030] Example 2: 2.0% Yttria Dispersion Strengthened Iron-Based Alloy
[0031] 1) Weigh 106 grams of analytically pure citric acid, dissolve it in deionized water, and configure it into a 600ml solution;
[0032] 2) Weigh the analytically pure Fe(NO 3 ) 3 .9H 2 O 202 grams, Y (NO 3 ) 3 .6H 2 O 1.94 grams, dissolved in citric acid aqueous solution;
[0033] 3) Add 15 grams of ethylene glycol as a dispersant, and slowly add ammonia water dropwise under magnetic stirring to adjust the pH value of the solution to 8;
[0034] 4) Put it into a water bath at 100°C for constant temperature heating and evaporation to form a sol;
[0035] 5) After forming the gel, put it in an oven for drying at 120°C to obtain a xerogel, and then roast it in a muffle furnace at 800°C to obtain an ultrafine oxide mixed powder;
[0036] 6) reducing the above-mentioned calcined oxide in a hydrogen flow at 800° C. for 40 minutes to obtain iron powder dispersed in nanometer yttrium oxide;
[0037]...
PUM
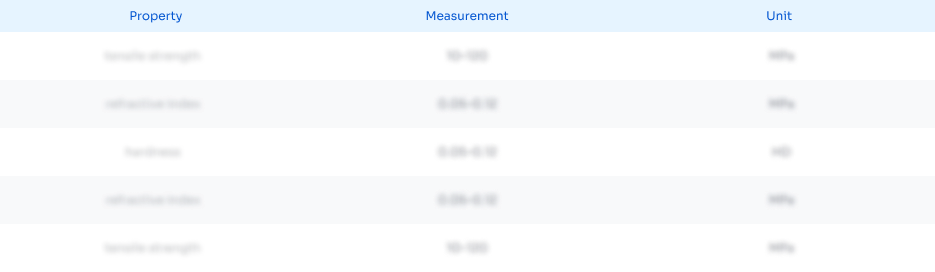
Abstract
Description
Claims
Application Information

- Generate Ideas
- Intellectual Property
- Life Sciences
- Materials
- Tech Scout
- Unparalleled Data Quality
- Higher Quality Content
- 60% Fewer Hallucinations
Browse by: Latest US Patents, China's latest patents, Technical Efficacy Thesaurus, Application Domain, Technology Topic, Popular Technical Reports.
© 2025 PatSnap. All rights reserved.Legal|Privacy policy|Modern Slavery Act Transparency Statement|Sitemap|About US| Contact US: help@patsnap.com