Superfine crystal nickel-based high-temperature alloy and method for preparing same
A nickel-based high-temperature alloy and ultra-fine-grained technology, applied in the field of high-temperature alloy steel, can solve the problems of complex composition and high alloy deformation resistance, and achieve the effects of simple composition, low tonnage requirements, and cost reduction
- Summary
- Abstract
- Description
- Claims
- Application Information
AI Technical Summary
Problems solved by technology
Method used
Image
Examples
Embodiment 1
[0023] Alloy 1 in Table 1 is an alloy within the specified composition range of the present invention. Its preparation method is that the raw materials are properly proportioned, then subjected to vacuum induction melting and vacuum arc remelting, and homogenized treatment: heat preservation at 1160°C for 25 hours and heat preservation at 1190°C for 75 hours. Then the billet is opened at 1120°C, and then rolled at 1050°C, and the final rolling temperature is 980°C. figure 1 and figure 2 It is the microstructure photo of Alloy 1 after rolling. It can be seen that the grains of alloy 1 after rolling are uniform and fine, and the grade is ASTM13; granular Nb-rich and Mo-rich precipitates are precipitated on the grain boundaries of the alloy. Due to the high dissolution temperature of the granular precipitated phase, even when heated at a higher temperature, the grain growth rate is very slow, image 3 and Figure 4 These are the comparisons of grain growth trends between the...
Embodiment 2
[0025] Alloy 2 in Table 1 is an alloy within the specified composition range of the present invention. Its preparation method is that the raw materials are properly proportioned, then subjected to vacuum induction melting and vacuum arc remelting, and then homogenized treatment: heat preservation at 1160°C for 25 hours and heat preservation at 1190°C for 75 hours. Then the billet is opened at 1120°C, and then the rolling is started at 1020°C, and the final rolling temperature is 980°C. Alloy 2 has uniform and fine grains after rolling, and its grade is ASTM12.5. The characteristics of the precipitated phase at the grain boundary and the grain growth trend during high-temperature heating are the same as those in Example 1.
Embodiment 3
[0027] Alloy 3 in Table 1 is an alloy within the specified composition range of the present invention. Its preparation method is that the raw materials are properly proportioned, then subjected to vacuum induction melting and vacuum arc remelting, and then homogenized treatment: heat preservation at 1160°C for 25 hours and heat preservation at 1190°C for 75 hours. Then the billet is opened at 1120°C, and then rolled at 1050°C, and the final rolling temperature is 990°C. Alloy 3 has uniform and fine grains after rolling, and its grade is ASTM12. The characteristics of the precipitated phase at the grain boundary and the grain growth trend during high-temperature heating are the same as those in Example 1.
[0028] Table 1 Alloy composition (wt%)
[0029]
PUM
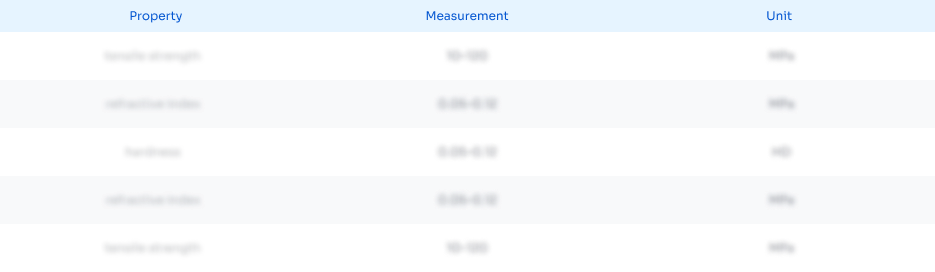
Abstract
Description
Claims
Application Information

- Generate Ideas
- Intellectual Property
- Life Sciences
- Materials
- Tech Scout
- Unparalleled Data Quality
- Higher Quality Content
- 60% Fewer Hallucinations
Browse by: Latest US Patents, China's latest patents, Technical Efficacy Thesaurus, Application Domain, Technology Topic, Popular Technical Reports.
© 2025 PatSnap. All rights reserved.Legal|Privacy policy|Modern Slavery Act Transparency Statement|Sitemap|About US| Contact US: help@patsnap.com