Production method and apparatus for trichlorosilane
A technology of trichlorosilane and its production method, which is applied in the direction of halosilane, silicon halide compound, energy input, etc., can solve the problems of insufficient recovery of synthesis tail gas, easy occurrence of overheating phenomenon, and consumption of low-temperature refrigerant, etc., to achieve beneficial The effect of detection and control, low production cost, and reduced consumption
- Summary
- Abstract
- Description
- Claims
- Application Information
AI Technical Summary
Problems solved by technology
Method used
Image
Examples
Embodiment 1
[0020] A kind of manufacture method of trichlorosilane, comprises the steps:
[0021] A, hydrogen chloride treatment: hydrogen chloride gas is dehydrated, then pressurized to 0.25Mpa (G) by a hydrogen chloride compressor and sent to the fluidized bed reactor after preheating;
[0022] B. Drying and pushing of silicon powder: transfer the silicon powder heated to 150°C to the bottom of the trichlorosilane large-scale fluidized bed reactor of the present invention to the silicon powder dried by hot nitrogen in the powder drying furnace;
[0023] C. Synthesis reaction: In the fluidized bed reactor, under the temperature control of 300°C and the pressure of 0.15Mpa (G), the silicon powder and hydrogen chloride undergo a gas-solid phase reaction to generate a mixture of trichlorosilane and silicon tetrachloride. The heat is removed by heat transfer oil, part of it is sent to waste heat boiler by-product steam and then merged into the steam pipe network, and part of it is directly u...
Embodiment 2
[0029] A kind of manufacture method of trichlorosilane, comprises the steps:
[0030] A. Hydrogen chloride treatment: Hydrogen chloride gas is dehydrated, then pressurized to 0.5Mpa (G) by a hydrogen chloride compressor and sent to the fluidized bed reactor after preheating;
[0031] B. Silicon powder drying and pushing: the silicon powder dried by hot nitrogen in the powder drying furnace is transported to the bottom of the fluidized bed reactor with nitrogen heated to 200°C;
[0032] C. Synthesis reaction: In the fluidized bed reactor, under the temperature control of 310°C and the pressure of 0.4Mpa (G), the silicon powder and hydrogen chloride undergo a gas-solid phase reaction to generate a mixture of trichlorosilane and silicon tetrachloride. The heat is removed by heat transfer oil, part of it is sent to waste heat boiler by-product steam and then merged into the steam pipe network, and part of it is directly used for some heat consuming equipment.
[0033] D. Dust remov...
Embodiment 3
[0038] A kind of manufacture method of trichlorosilane, comprises the steps:
[0039] A. Hydrogen chloride treatment: Hydrogen chloride gas is dehydrated, then pressurized to 0.5Mpa (G) by a hydrogen chloride compressor and sent to the fluidized bed reactor after preheating;
[0040] B. Silicon powder drying and pushing: the silicon powder dried by hot nitrogen in the powder drying furnace is transported to the bottom of the fluidized bed reactor with nitrogen heated to 180°C;
[0041] C. Synthesis reaction: In the fluidized bed reactor, under the temperature control of 310°C and the pressure of 0.4Mpa (G), the silicon powder and hydrogen chloride undergo a gas-solid phase reaction to generate a mixture of trichlorosilane and silicon tetrachloride. The heat is removed by heat transfer oil, part of it is sent to waste heat boiler by-product steam and then merged into the steam pipe network, and part of it is directly used for some heat consuming equipment.
[0042] D. Dust rem...
PUM
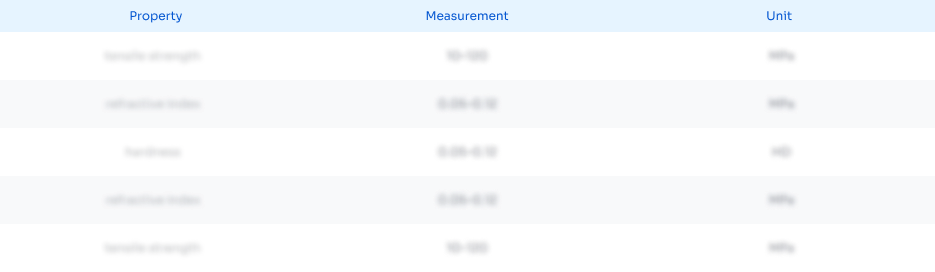
Abstract
Description
Claims
Application Information

- Generate Ideas
- Intellectual Property
- Life Sciences
- Materials
- Tech Scout
- Unparalleled Data Quality
- Higher Quality Content
- 60% Fewer Hallucinations
Browse by: Latest US Patents, China's latest patents, Technical Efficacy Thesaurus, Application Domain, Technology Topic, Popular Technical Reports.
© 2025 PatSnap. All rights reserved.Legal|Privacy policy|Modern Slavery Act Transparency Statement|Sitemap|About US| Contact US: help@patsnap.com