A lanthanon permanent magnetic powder and its making method
A rare earth permanent magnet and magnetic powder technology, which is applied in the direction of magnetic materials, magnetic objects, and inorganic materials, can solve the problems of high price of rare earth metal Nd, high price of rare earth permanent magnet powder, and poor coercive force of rare earth permanent magnet powder. Achieve good market application prospects, high cost performance, and improve the effect of coercive force
- Summary
- Abstract
- Description
- Claims
- Application Information
AI Technical Summary
Problems solved by technology
Method used
Image
Examples
Embodiment 1
[0031] Example 1 Preparation by arc remelting and rapid quenching
[0032] The used metal batching composition of the present embodiment is: (Nd 0.49 La 0.51 ) 12.7 Fe 76.4 B 7.7 Zr 3.2
[0033] The total mass percentage of pure metal and mixed rare earth elements in the ingredients is: Nd: 13.95wt% La: 13.92wt% Fe: 66.31wt% B: 1.29wt% Zr: 4.53wt%, the preparation process of the arc remelting and rapid quenching method is as follows:
[0034] (1) Alloy melting and crushing
[0035]After the above raw materials are prepared according to the ingredients, they are melted and cast into alloy ingots in a vacuum induction melting furnace. The smelted alloy ingot is broken into alloy particles of <10mm by jaw crusher.
[0036] (2) Rapid Quenching Milling
[0037] Put the broken alloy particles into the vacuum arc quenching furnace and vacuumize. After the vacuum is lower than 10Pa, fill Ar gas to -0.04MPa~0.2MPa, start arc quenching, and the linear speed of the roller is 15...
Embodiment 2
[0045] Example 2 Preparation by induction remelting and rapid quenching
[0046] The used metal batching composition of the present embodiment is: (Nd 0.49 La 0.51 ) 12.7 Fe 76.4 B 7.7 Zr 3.2
[0047] The total mass percentage of pure metals and mixed rare earth elements in the ingredients is: Nd: 13.95wt% La: 13.92wt% Fe: 66.31wt% B: 1.29wt% Zr: 4.53wt%, made by induction remelting and rapid quenching process including the following step:
[0049] After the above raw materials are prepared according to the ingredients, they are melted and cast into alloy ingots in a vacuum induction melting furnace.
[0050] (2) Rapid Quenching Milling
[0051] Put the melted alloy ingot into the vacuum induction quenching furnace, pump the vacuum to below 10Pa, start the intermediate frequency and high frequency melting bag, after the alloy ingot is melted, fill it with Ar gas to -0.04MPa~0.2MPa, after melting The molten metal flows through the nozzle to...
Embodiment 3
[0059] Example 3 Preparation by Arc Remelting and Rapid Quenching
[0060] The used metal batching composition of the present embodiment is: (Nd 0.61 La 0.39 ) 11.6 Fe 77.6 B 7.6 Zr 3.2
[0061] The total mass percentage of pure metal and mixed rare earth elements in the batch is: Nd: 16.05wt% La: 9.89wt% Fe: 68.18wt% B: 1.29wt% Zr: 4.59wt%, the implementation process is as in Example 1.
[0062] After testing, the performance of the quenching magnet is:
[0063] B r : 597.10mT H cj : 707.17kA / m (BH) max : 57.761kJ / m 3 h k : 206.79kA / m
[0064] The test curve is shown in Figure 3
PUM
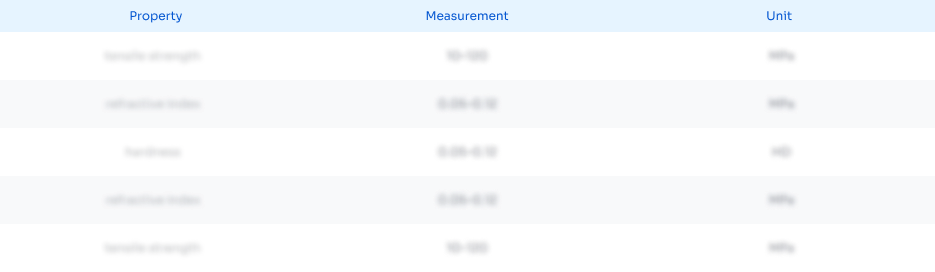
Abstract
Description
Claims
Application Information

- R&D
- Intellectual Property
- Life Sciences
- Materials
- Tech Scout
- Unparalleled Data Quality
- Higher Quality Content
- 60% Fewer Hallucinations
Browse by: Latest US Patents, China's latest patents, Technical Efficacy Thesaurus, Application Domain, Technology Topic, Popular Technical Reports.
© 2025 PatSnap. All rights reserved.Legal|Privacy policy|Modern Slavery Act Transparency Statement|Sitemap|About US| Contact US: help@patsnap.com