Method for recovering cutting solution from by-product of silicon chip cutting processing
A silicon wafer cutting and by-product technology, applied in separation methods, chemical instruments and methods, distillation separation, etc., can solve the problems of waste of resources, high price, environmental pollution, etc., and achieve the effect of reducing environmental pollution
- Summary
- Abstract
- Description
- Claims
- Application Information
AI Technical Summary
Problems solved by technology
Method used
Examples
Embodiment 1
[0023] Get the sample 1000g of silicon chip cutting by-product, add the flask with stirring, after stirring evenly, add 250g separating agent, the composition of separating agent is: polyethylene glycol 200 (PEG200) 50g, polyethylene glycol 10000 (PEG10000) 20g , polyethylene glycol monoethyl ether 12g, polyethylene glycol monooleate (DO400) 5g, nonionic surfactant (emulsifier OP-10) 11g, penetrant (JFC) 8g, after stirring evenly at 40°C , into a centrifuge to obtain 750g of SiC-rich slurry and 500g of SiC-poor suspension; the SiC-poor suspension is separated from the solid-liquid by a plate-and-frame filter: add 30gXRD-1 to the resulting filtrate at 115 React at ℃ for 10 hours, cool to 60℃, enter the plate and frame filter to filter out solid particles; then enter the distillation pot, 130℃, remove low boilers under normal pressure, cool to below 60℃ to obtain the recovered cutting fluid. The recycled cutting fluid is used for wire-cutting processing of solar-grade silicon ro...
Embodiment 2
[0025] Get the sample 1000g of silicon chip cutting by-product, add the flask with stirring, after stirring evenly, add 350g separating agent, the composition of separating agent is: polyethylene glycol 200 (PEG200) 100g, polyethylene glycol 10000 (PEG10000) 50g , polyethylene glycol monoethyl ether 22g, polyethylene glycol monooleate (DO400) 8g, polyethylene glycol dioleate (MO600) 8g nonionic surfactant (OP-10) 12g, penetrant (JFC ) 8g, after stirring evenly at 40°C, enter the centrifuge to obtain 800g of silicon carbide-rich slurry and 453g of silicon carbide-poor suspension, the suspension is separated from solid and liquid by a plate and frame filter, and 35g of XRD- 1. React at 115°C for 10 hours, cool to 60°C, enter the plate and frame filter, filter out solid particles, then enter the distillation pot, 130°C, remove low boiling substances under normal pressure, and cool to below 60°C to obtain Recycle the cutting fluid. The recycled cutting fluid is used for wire-cutt...
Embodiment 3
[0027] Get the sample 1000g of silicon chip cutting by-product, add the flask with stirring, after stirring evenly, add 200g separating agent, the composition of separating agent is: polyethylene glycol 400 (PEG400) 50g, polyethylene glycol 800 (PEG800) 20g , polyethylene glycol monoethyl ether 12g, polyethylene glycol monooleate (DO400) 5g, polyethylene glycol dioleate (MO600) 5g nonionic surfactant (OP-10) 8g, penetrant (JFC ) 8g, viscosity modifier 5g, after stirring evenly at 40°C, enter the centrifuge to obtain 813g of silicon carbide-rich slurry and 528g of silicon carbide-poor suspension, the suspension is separated from solid and liquid by a plate and frame filter, and the obtained filtrate Add 40g of XRD-1 to it, react at 105°C for 14 hours, cool to 60°C, enter the plate and frame filter, filter out solid particles, and then enter the distillation pot, at 130°C, remove low boiling substances under normal pressure, cool to 60°C The recovered cutting fluid can be obtain...
PUM
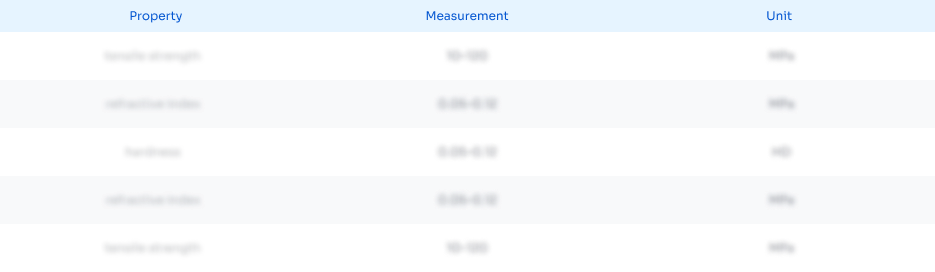
Abstract
Description
Claims
Application Information

- R&D Engineer
- R&D Manager
- IP Professional
- Industry Leading Data Capabilities
- Powerful AI technology
- Patent DNA Extraction
Browse by: Latest US Patents, China's latest patents, Technical Efficacy Thesaurus, Application Domain, Technology Topic, Popular Technical Reports.
© 2024 PatSnap. All rights reserved.Legal|Privacy policy|Modern Slavery Act Transparency Statement|Sitemap|About US| Contact US: help@patsnap.com