Method for preparing fully-degradable natural fibre/montmorillonite/polylactic acid composite material
A technology of natural fibers and composite materials, which is applied in the field of preparation of fully degradable natural fibers/montmorillonite/polylactic acid composite materials, can solve the problems of inability to carry out large-scale industrial production and cannot be completely degraded, and achieve excellent biodegradability, The preparation method is simple and effective, and the effect is suitable for industrial production
- Summary
- Abstract
- Description
- Claims
- Application Information
AI Technical Summary
Problems solved by technology
Method used
Examples
Embodiment 1
[0030] 1. Polylactic acid, montmorillonite, and ramie fibers with an aspect ratio of 5 were vacuum-dried at 30°C for 24 hours to remove moisture.
[0031] 2. Mix the dried polylactic acid, montmorillonite, compatibilizer polycaprolactone and antioxidant tris(2,4-di-tert-butylphenyl) phosphite in a dry container in proportion by weight , wherein polylactic acid is 90 parts, montmorillonite is 8 parts, compatibilizer is 1 part, and antioxidant is 1 part; Melt and blend with twin-screw extruder, carry out reactive extrusion, screw speed is 10rpm, extrusion The outlet temperature is 140°C. After the material is extruded, it is cooled, pelletized and dried to obtain the masterbatch.
[0032] 3. Mix the polylactic acid masterbatch obtained in step 2 with polylactic acid and ramie fiber according to a certain ratio in a twin-screw extruder for compound extrusion, wherein the screw speed is 200rpm, and the extrusion temperature is 180°C. The polylactic acid masterbatch 5 parts for ra...
Embodiment 2
[0034] 1. Polylactic acid, montmorillonite, and sisal fibers with an aspect ratio of 100 were vacuum-dried at 120°C for 1 hour to remove moisture.
[0035] 2. Mix the dried polylactic acid, montmorillonite, compatibilizer polyhydroxyalkanoate and antioxidant phosphite tris (2,4-di-tert-butylphenyl) ester in a dry container in proportion by weight Uniform, wherein polylactic acid is 85 parts, montmorillonite is 6 parts, compatibilizer is 4 parts, antioxidant is 5 parts; Melt and blend with twin-screw extruder, carry out reactive extrusion, screw speed is 250rpm, The extrusion temperature is 190°C. After extrusion, the material is cooled, pelletized and dried to obtain the masterbatch.
[0036] 3. Mix the polylactic acid masterbatch obtained in step 2 with polylactic acid and sisal fiber according to a certain ratio in a twin-screw extruder for compound extrusion, wherein the screw speed is 250rpm, and the extrusion temperature is 180°C. The material is 25 parts, and the sisal ...
Embodiment 3
[0038] 1. Polylactic acid, montmorillonite, and jute fibers with an aspect ratio of 50 were vacuum-dried at 80°C for 12 hours to remove moisture.
[0039] 2. Mix the dried polylactic acid, montmorillonite, compatibilizer polyethylene glycol and antioxidant phenylene diisodecyl phosphite evenly in a dry container in proportion by weight, wherein polylactic acid is 80 parts, montmorillonite The soil is 15 parts, the compatibilizer is 4 parts, and the antioxidant is 1 part; use a twin-screw extruder to melt and blend, and carry out reactive extrusion, the screw speed is 150rpm, and the extrusion temperature is 180°C. The masterbatch is obtained after cooling, pelletizing and drying.
[0040]3. Mix the polylactic acid masterbatch obtained in step 2 with polylactic acid and jute fiber according to a certain ratio in a twin-screw extruder for compound extrusion, wherein the screw speed is 170rpm, the extrusion temperature is 170°C, and the polylactic acid masterbatch is 20 parts, j...
PUM
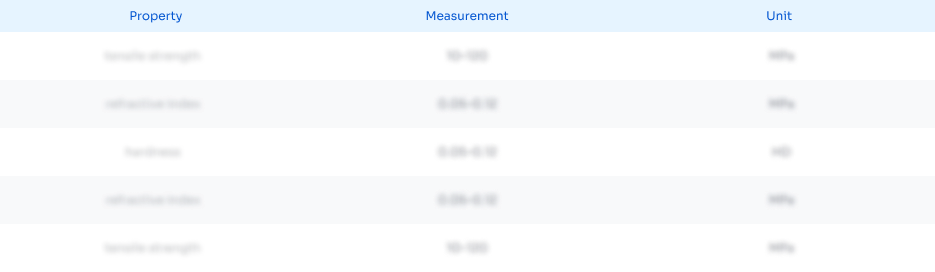
Abstract
Description
Claims
Application Information

- R&D
- Intellectual Property
- Life Sciences
- Materials
- Tech Scout
- Unparalleled Data Quality
- Higher Quality Content
- 60% Fewer Hallucinations
Browse by: Latest US Patents, China's latest patents, Technical Efficacy Thesaurus, Application Domain, Technology Topic, Popular Technical Reports.
© 2025 PatSnap. All rights reserved.Legal|Privacy policy|Modern Slavery Act Transparency Statement|Sitemap|About US| Contact US: help@patsnap.com