Method for smelting high-speed steel by employing oxide ore
A high-speed steel and oxide technology, applied in the field of steelmaking in the metallurgical industry, can solve the problems of low alloy yield, low direct alloying rate, and no technical reports, and achieve the effect of high yield
- Summary
- Abstract
- Description
- Claims
- Application Information
AI Technical Summary
Problems solved by technology
Method used
Examples
Embodiment 1
[0026] Embodiment 1: fully use V on the electric arc furnace with charging capacity of 30 tons 2 o 5 Direct alloying smelting of high-speed tool steel W6Mo5Cr4V2 (M2), the adopted process route is as follows: when charging, first put 450kg of lime and 150kg of fluorite at the bottom of the smelting furnace, and add 25500kg of ordinary carbon and low phosphorus (p≤0.3%) scrap steel raw materials; Mix molybdenum oxide with a reducing agent, the amount of molybdenum oxide is 2850kg; the reducing agent is carbon powder, the amount is 600kg, and the mixture of molybdenum oxide and reducing agent is installed around the scrap raw material; select 4500kg tungsten ore, select carbon powder, Ferrosilicon is used as a reducing agent, and the dosage is: 300kg of carbon powder and 375kg of ferrosilicon. After mixing tungsten ore and reducing agent, put it into the high temperature action area of the smelting furnace, and keep a distance of 1 meter from the furnace wall. After the charg...
Embodiment 2
[0029] Embodiment 2: fully use V on the electric arc furnace with charging capacity of 15 tons 2 o 5 Direct alloying smelting high-speed tool steel W6Mo5Cr4V2A1 (M2A1 brand), when charging, first put lime 187.5kg and fluorite 37.5kg in the bottom of the smelting furnace, add ordinary carbon and low phosphorus (p≤0.3%) scrap steel raw materials 12375kg; add molybdenum oxide The dosage is 1350kg, the reducing agents used are carbon powder and ferrosilicon, the dosages are: carbon powder is 142.5kg, ferrosilicon alone is 116.3kg, molybdenum oxide and reducing agent are mixed and installed around the scrap raw materials ; Mix tungsten ore with reducing agent, the consumption of tungsten ore is 1875kg, reducing agent is carbon powder, silicon carbide, consumption is respectively: carbon powder is 131.3kg, silicon carbide is 146.3kg. Put the mixture of tungsten ore and reducing agent into the high-temperature action area of the smelting furnace, 1.1 meters away from the furnace w...
Embodiment 3
[0031] Embodiment 3: fully use V on the electric arc furnace with charging capacity of 10 tons 2 o 5 Direct alloying smelting high-speed tool steel W6Mo5Cr4V2A1 (M2A1), when charging, first put 100kg of lime in the bottom of the smelting furnace, add 8000kg of ordinary carbon and low phosphorus (p≤0.3%) scrap steel raw materials; mix molybdenum oxide with reducing agent, oxidize The amount of molybdenum is 850kg, the reducing agent is ferrosilicon, the dosage is 130kg for ferrosilicon, the mixture of molybdenum oxide and reducing agent is installed around the scrap raw material; the tungsten ore is mixed with the reducing agent, and the amount of tungsten ore is: 1000kg , the reducing agent is carbon powder and silicon carbide, and the dosage is respectively: 75kg of carbon powder and 85kg of silicon carbide. Put the mixture of tungsten ore and reducing agent into the high-temperature action area of the smelting furnace, and at least 1.2 meters away from the furnace wall; s...
PUM
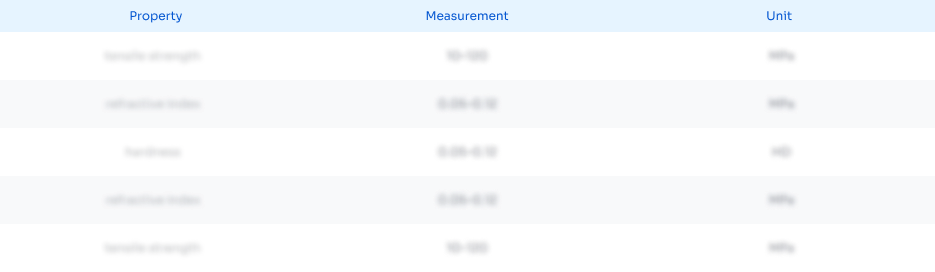
Abstract
Description
Claims
Application Information

- R&D
- Intellectual Property
- Life Sciences
- Materials
- Tech Scout
- Unparalleled Data Quality
- Higher Quality Content
- 60% Fewer Hallucinations
Browse by: Latest US Patents, China's latest patents, Technical Efficacy Thesaurus, Application Domain, Technology Topic, Popular Technical Reports.
© 2025 PatSnap. All rights reserved.Legal|Privacy policy|Modern Slavery Act Transparency Statement|Sitemap|About US| Contact US: help@patsnap.com