Carbon-base tungsten coating and its preparation method
A coating and carbon-based technology, which is applied in the field of carbon-based tungsten coating and its preparation, can solve problems such as low density and purity, accumulation of impurity ash, poor bonding force of grain boundary strength, etc., achieve fast deposition speed, improve efficiency, The effect of surface densification
- Summary
- Abstract
- Description
- Claims
- Application Information
AI Technical Summary
Problems solved by technology
Method used
Examples
Embodiment 1
[0013] Choose carbon / carbon composite material as the substrate, and set the process parameters for depositing tungsten coating by double-layer glow ion metallization technology: source voltage 950V, cathode voltage 500V, air pressure 50Pa, spacing 15mm, duty cycle 0.8, deposition time 4h. Treat the surface of the carbon / carbon composite material with crystal phase sandpaper and ultrasonically clean it, then dry it and put it on the cathode of the double-glow furnace, vacuumize and feed argon, adjust the cathode voltage to 350V and heat and clean the carbon / carbon composite material matrix for 0.5 hours . Turn on the furnace, put the tungsten plate on the source of the double-glow furnace, close the furnace, evacuate and inject argon gas, and follow the set double-layer glow ion infiltration metal process parameters (including source voltage, cathode voltage, air pressure, pole voltage, etc.) spacing, duty cycle, deposition time) to deposit the tungsten coating; heat-treat th...
Embodiment 2
[0015] Graphite was selected as the substrate, and the process parameters of tungsten coating deposited by double-layer glow ion metallization technology were set: source voltage 950V, cathode voltage 450V, air pressure 40Pa, electrode spacing 10mm, duty cycle 0.6, deposition time 6h. Treat the graphite surface with crystal phase sandpaper and ultrasonically clean it, then dry it and place it on the cathode of a double-glow furnace, vacuumize and feed argon, adjust the cathode voltage to 300V and heat and clean the graphite substrate for 1 hour. Turn on the furnace, put the tungsten plate on the source of the double-glow furnace, close the furnace, evacuate the argon gas, and follow the set double-layer glow ionization metal permeation process parameters (including source voltage, cathode voltage, air pressure, spacing, duty cycle, deposition time) for the deposition of tungsten coating. The prepared carbon-based tungsten coating was heat-treated at 1200° C. for 0.5 hours.
Embodiment 3
[0017] Carbon / carbon composite material is selected as the substrate, and the process parameters for depositing tungsten coating by double-layer glow ion metallization technology are set: source voltage 850V, cathode voltage 550V, air pressure 50Pa, electrode spacing 20mm, duty cycle 0.8, deposition Time 2h. Treat the surface of the carbon / carbon composite material with crystal phase sandpaper and ultrasonically clean it, then dry it and put it on the cathode of the double-glow furnace, vacuumize and feed argon, adjust the cathode voltage to 350V and heat and clean the carbon / carbon composite material matrix for 1.5h . Turn on the furnace, put the tungsten plate on the source of the double-glow furnace, close the furnace, evacuate the argon gas, and follow the set double-layer glow ionization metal permeation process parameters (including source voltage, cathode voltage, air pressure, spacing, duty cycle, deposition time) to deposit the tungsten coating; heat-treat the prepar...
PUM
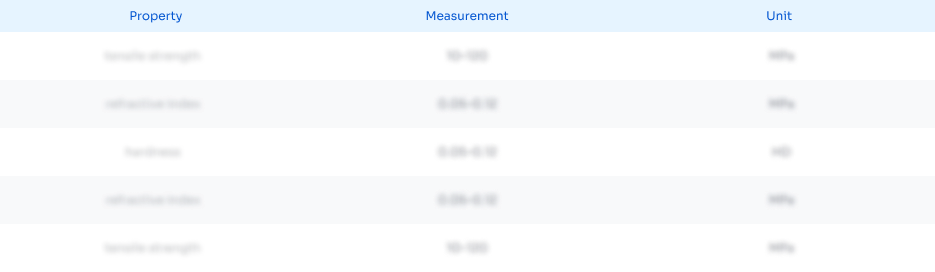
Abstract
Description
Claims
Application Information

- R&D
- Intellectual Property
- Life Sciences
- Materials
- Tech Scout
- Unparalleled Data Quality
- Higher Quality Content
- 60% Fewer Hallucinations
Browse by: Latest US Patents, China's latest patents, Technical Efficacy Thesaurus, Application Domain, Technology Topic, Popular Technical Reports.
© 2025 PatSnap. All rights reserved.Legal|Privacy policy|Modern Slavery Act Transparency Statement|Sitemap|About US| Contact US: help@patsnap.com