Surface modification method for ruthenium in situ wrapping ultramicro high purity Si3N4 powder
A surface modification and ultra-fine technology, applied in the field of high-performance structural ceramic materials, can solve the problems of complex equipment, degraded high-temperature performance of materials, high cost, etc., to improve green body density and sintering activity, improve uniformity, and low cost Effect
- Summary
- Abstract
- Description
- Claims
- Application Information
AI Technical Summary
Problems solved by technology
Method used
Examples
Embodiment 1
[0023] Direct injection of highly dispersed Si with an average size of 90 nm in 5 ml of analytically pure ethanol 3 N 4 (Specific surface 11.2m 2 / g) particles 16.7mg, ball milled for 4 hours to make it evenly suspended and dispersed, drop by drop into 5ml0.1mM / LRuCl 3 ·nH2 O ethanol solution, continue ball milling for 2 hours, add 0.1 ml of 75% hydrazine hydrate drop by drop, stir evenly, add ammonia water to adjust the pH value of the suspension to 8.5-9. Then pour it into a pressure vessel, tighten the seal, keep warm at 100°C, and perform an alcohol thermal reduction reaction for 2 hours, take it out, centrifuge, filter, wash with alcohol, and dry to obtain 16.75 mg of ruthenium-wrapped Si 3 N 4 Composite (ruthenium content 0.3wt.%), solid composite ultrafine Si 3 N 4 The average particle size of the powder is 140nm, and the original N-H deformation vibration peak in the infrared absorption spectrum disappears.
Embodiment 2
[0025] Inject 90nm highly dispersed Si directly into 15ml analytical pure ethanol 3 N 4 (Specific surface 11.2m 2 / g) particles 200mg, ball milled and stirred for 4 hours to make it evenly suspended and dispersed, dropwise added 6ml 20mM / L RuBr 3 ·nH 2 O ethanol solution, ball milled and stirred for 2 hours, 1.5 ml of 75% hydrazine hydrate was added dropwise, stirred evenly, and ammonia water was added to adjust the pH value of the suspension to 8.5-9. Then pour it into a pressure vessel, tighten the seal, keep warm at 100°C, and perform an alcohol thermal reduction reaction for 2 hours, take it out, centrifuge, filter, wash with alcohol, and dry to obtain 212.13 mg of ruthenium-wrapped Si 3 N 4 Composite (ruthenium content 5.72wt.%), solid composite Si 3 N 4 The average particle diameter of the powder is 200nm, and the original N-H deformation vibration peak in the infrared absorption spectrum spectrum disappears.
Embodiment 3
[0027] Inject 90nm highly dispersed Si directly into 15ml analytical pure ethanol 3 N 4 (Specific surface 11.2m 2 / g) 200 mg of granules, ball milled and stirred for 4 hours to make them uniformly suspended and dispersed, and 1.2ml of 100mM / LRuCl was added dropwise 3 ·nH 2 O, continue ball milling and stirring for 2 hours, add 1.5 ml of 75% hydrazine hydrate drop by drop, stir evenly, add ammonia water to adjust the pH value of the suspension to 8.5-9. Then pour it into a pressure vessel, tighten the seal, keep warm at 100°C, and carry out alcohol thermal reduction for 2 hours. Take it out, centrifuge, filter, wash with alcohol, and dry to obtain 212.12 mg of ruthenium-wrapped Si 3 N 4 Composite (ruthenium content 5.71 wt.%). solid composite Si 3 N 4 In addition to the Si and N peaks, Ru peaks also appear on the EDS spectrum of the powder.
PUM
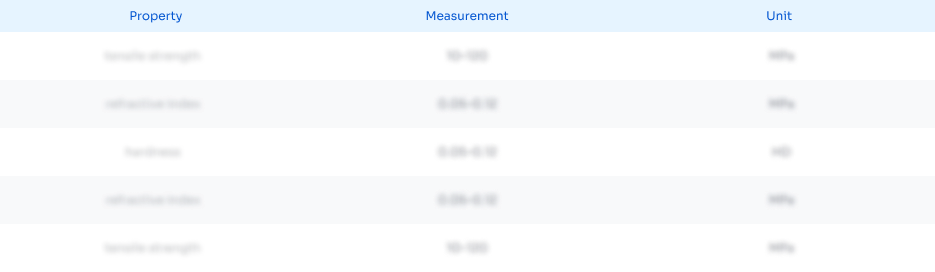
Abstract
Description
Claims
Application Information

- R&D Engineer
- R&D Manager
- IP Professional
- Industry Leading Data Capabilities
- Powerful AI technology
- Patent DNA Extraction
Browse by: Latest US Patents, China's latest patents, Technical Efficacy Thesaurus, Application Domain, Technology Topic, Popular Technical Reports.
© 2024 PatSnap. All rights reserved.Legal|Privacy policy|Modern Slavery Act Transparency Statement|Sitemap|About US| Contact US: help@patsnap.com