Double hot-rolling composite friction material and its production
A composite friction material, double hot pressing technology, applied in the field of composite friction materials, can solve the problems of low bonding strength and low porosity, and achieve the effects of stable friction coefficient, increased porosity coefficient and low wear rate
- Summary
- Abstract
- Description
- Claims
- Application Information
AI Technical Summary
Problems solved by technology
Method used
Examples
Embodiment 1
[0032] Embodiment 1: Taking the Jetta front wheel brake pad as an example, the height after pressing is 12 mm.
[0033] The basic formula of the first hot-pressed hybrid fiber composite friction material (by mass percentage): 15% cashew oil modified phenolic resin; 5% clear rubber; 15% steel fiber; 5% vermiculite; 2% Kevlar fiber; 5% cotton, 8% silicon oxide; 10% talc; 5% molybdenum disulfide; 20% barium sulfate; 10% calcium hydroxide.
[0034] Mix the above materials evenly, weigh them and pour them into a standard mold (length 300mm×width 60mm), at 150°C; pressure 16Mpa; holding time 3 minutes and deflate twice; Composite friction material; put the pressed material into a constant temperature box for post-treatment at 160°C for 4 hours.
[0035] Under dry conditions, leave it for more than 24 hours; then crush it, and use a sieve of 5-10 mesh (2-2.8mm sieve hole) to sieve.
[0036] In terms of mass fraction, the formula used for the second hot-pressed composite friction ma...
Embodiment 2
[0038]Embodiment 2: Taking the Jetta front wheel brake pad as an example, the height after pressing is 12mm.
[0039] The basic formula of the first hot-pressed semi-metallic fiber composite friction material (by mass percentage): cashew nut oil modified phenolic resin 20%; nitrile rubber 5%; steel fiber 28%; copper scrap 2%; aluminum oxide 8% 2% cast stone powder; 3% molybdenum disulfide; 7% graphite; 15% barium sulfate; 5% magnesium oxide, 5% kaolin. In fact, the first thermocompression forming composite friction material can be selected from waste materials prepared from the above formula.
[0040] Mix the above materials evenly, weigh them and pour them into a standard mold (length 300mm×width 60mm), at 165°C; pressure 20Mpa; holding time 3 minutes and deflate 2 times; Composite friction material; put the pressed material into a constant temperature box for post-treatment at 160°C for 4 hours.
[0041] Under dry conditions, let it stand for more than 24 hours; then crush...
Embodiment 3
[0045] The basic formula of the first heat-pressed non-metal fiber composite friction material (by mass percentage): cashew nut oil modified phenolic resin 25%; nitrile rubber 5%; vermiculite 8%; sepiolite 10%; Kevlar fiber 2 %; aluminum oxide 10%; molybdenum disulfide 5%; talcum powder 10%; barium sulfate 15%; magnesium oxide 5%, kaolin 5%. Mix the above materials evenly, weigh them and pour them into a standard mold (length 300mm×width 60mm), at 140°C; pressure 12Mpa; holding time 3 minutes and deflate twice; Composite friction material; put the pressed material into a constant temperature box for post-treatment at 160°C for 4 hours. The metal fiber-free composite friction material for the first hot pressing can also be the waste material of the first hot pressing forming composite friction material.
[0046] Under dry conditions, it is placed for more than 24 hours; then it is pulverized and screened with a 10-mesh sieve.
[0047] In terms of mass fraction, the formula us...
PUM
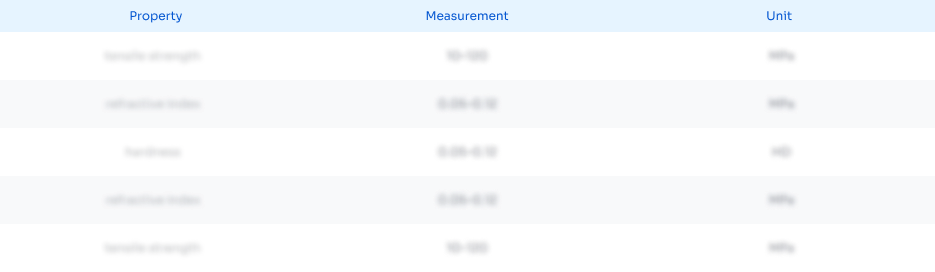
Abstract
Description
Claims
Application Information

- Generate Ideas
- Intellectual Property
- Life Sciences
- Materials
- Tech Scout
- Unparalleled Data Quality
- Higher Quality Content
- 60% Fewer Hallucinations
Browse by: Latest US Patents, China's latest patents, Technical Efficacy Thesaurus, Application Domain, Technology Topic, Popular Technical Reports.
© 2025 PatSnap. All rights reserved.Legal|Privacy policy|Modern Slavery Act Transparency Statement|Sitemap|About US| Contact US: help@patsnap.com