Preparation technology for gamma phase U-Mo alloy powder
A preparation process and technology of alloy powder, applied in the field of preparation of γ-phase U-Mo alloy powder, can solve the problems of high powder milling cost, easy environmental pollution, huge equipment, etc., to improve hydrogenation efficiency, reduce impurity content, and improve ball milling. The effect of efficiency
- Summary
- Abstract
- Description
- Claims
- Application Information
AI Technical Summary
Problems solved by technology
Method used
Image
Examples
Embodiment 1
[0014] The devices used in this example include a hydrogenation furnace, a planetary ball mill, a muffle furnace, a vacuum sealing device for quartz tubes, a hypoxic glove box, and the like.
[0015] Firstly, the U-2Mo alloy rod was vacuum annealed at 800°C for 2 hours. Grind the surface with metallographic sandpaper, remove the surface oxide film with dilute nitric acid, wash with absolute ethanol, quickly place it in a hydrogenation furnace, and vacuumize it for storage. Raise the temperature of the hydrogenation furnace to 60°C and fill it with 0.2MPa high-purity hydrogen for hydrogenation. The hydrogenation holding time is 2 hours. Then evacuate to 100Pa, continue to heat up to 350°C, and keep warm for 1 hour to dehydrogenate uranium hydride. After dehydrogenation, when the temperature is lowered to 60°C, 0.2 MPa high-purity hydrogen gas is introduced for hydrogenation, and the hydrogenation holding time is 2 hours. After the hydrogenation is completed, the sample is coo...
Embodiment 2
[0018] This example is the same as Example 1, except that the U-7Mo alloy rod is vacuum annealed at 900° C. for 4 hours. Grind with metallographic sandpaper, remove the oxide film on the surface with dilute nitric acid, wash with absolute ethanol, quickly place it in a hydrogenation furnace, and vacuumize it for storage. The hydrogenation furnace was heated up to 150°C, filled with 0.3MPa high-purity hydrogen for hydrogenation, and the hydrogenation holding time was 4 hours. Then evacuate to 60Pa, continue to heat up to 450°C, and keep warm for 2.5 hours to dehydrogenate uranium hydride. After dehydrogenation, when the temperature is lowered to 160°C, 0.3MPa high-purity hydrogen is introduced for hydrogenation, and the hydrogenation holding time is 4 hours. After the hydrogenation is completed, the sample is cooled with the furnace, and a layered and granular uranium hydride-molybdenum dual-phase product is obtained. Use a star ball mill, agate jar and tungsten balls to make...
Embodiment 3
[0021] This example is the same as Example 1, except that the U-10Mo alloy rod is vacuum annealed at 1000° C. for 6 hours. Grind with metallographic sandpaper, remove the oxide film on the surface with dilute nitric acid, wash with absolute ethanol, quickly place it in a hydrogenation furnace, and vacuumize it for storage. The hydrogenation furnace was heated up to 250°C, filled with 0.4MPa high-purity hydrogen for hydrogenation, and the hydrogenation holding time was 6 hours. Then evacuate to 30Pa, continue to heat up to 550°C, and keep warm for 4 hours to dehydrogenate uranium hydride. After dehydrogenation, when the temperature is lowered to 250°C, 0.4MPa high-purity hydrogen is introduced for hydrogenation, and the hydrogenation holding time is 6 hours. After the hydrogenation is completed, the sample is cooled with the furnace, and a layered and granular uranium hydride-molybdenum dual-phase product is obtained. Use a star ball mill, agate jar and tungsten balls to make...
PUM
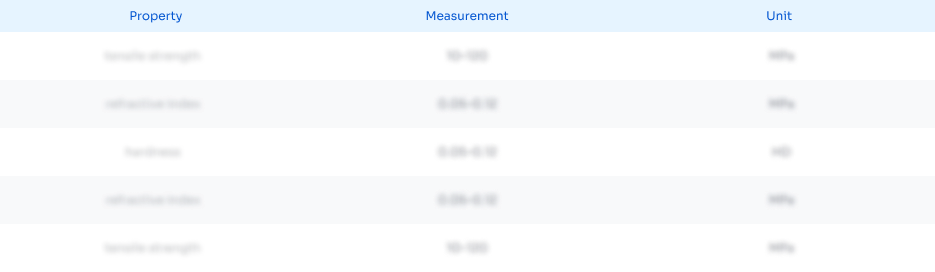
Abstract
Description
Claims
Application Information

- R&D
- Intellectual Property
- Life Sciences
- Materials
- Tech Scout
- Unparalleled Data Quality
- Higher Quality Content
- 60% Fewer Hallucinations
Browse by: Latest US Patents, China's latest patents, Technical Efficacy Thesaurus, Application Domain, Technology Topic, Popular Technical Reports.
© 2025 PatSnap. All rights reserved.Legal|Privacy policy|Modern Slavery Act Transparency Statement|Sitemap|About US| Contact US: help@patsnap.com