Technique for alloying steel making directly from tungsten ore
A technology of alloying steelmaking and tungsten ore, which is applied in the field of alloy steel smelting, can solve the problems of large amount of direct alloying slag, low tungsten yield, and low solid-state reduction rate, so as to improve the reduction reaction speed and be easy to operate The effect of running and short recovery period
- Summary
- Abstract
- Description
- Claims
- Application Information
AI Technical Summary
Problems solved by technology
Method used
Examples
Embodiment 1
[0036] Example 1: High-speed tool steel M2 (W6Mo5Cr4V2) is completely smelted by direct alloying of tungsten ore on an electric arc furnace with a charging capacity of 20 tons. The process route adopted is: low-phosphorus P scrap steel and carbon-containing tungsten ore balls are cold-packed in an electric furnace Group, silicon carbide SiC, adding ferromolybdenum → enter the melting period → enter the oxidation period → enter the reduction period → add ferrovanadium → add slag depletion agent silicon carbide SiC → release from the furnace → desulfurize and refine in the LF furnace → perform VD vacuum treatment → carry out pouring. In this process route, the carbon-containing tungsten ore pellets are first prepared, which are composed of 85% tungsten ore, 13% reducing agent, 1% catalyst, and 1% binder. Firstly, the tungsten ore, reducing agent, The catalyst is crushed and ground into a 200-mesh powder, then mixed and added with a binder to form a carbon-tungsten ore pellet. T...
Embodiment 2
[0037] Embodiment 2: fully use tungsten ore direct alloying to smelt high-speed tool steel M2Al (W6Mo5Cr4V2 Al) on the electric arc furnace with charging capacity of 15 tons. Silicon carbide SiC, adding ferromolybdenum → enter the melting period → enter the oxidation period → enter the reduction period → add ferrovanadium → add slag depleting agent SiC → add aluminum ingots, take out the furnace → carry out desulfurization and refining in LF furnace → perform VD vacuum treatment → carry out pouring. The prepared carbon-containing tungsten ore pellets are composed of 82.5% tungsten ore, 15% reducing agent, 1.5% catalyst, and 1% binder. First, the tungsten ore, reducing agent, and catalyst are crushed and ground into 200 Mesh powder, then mix and add binder to make tungsten carbide pellets. The tungsten content of tungsten ore is 49.6%, the reducing agent is 80% coal mixed with 20% coke powder, the fixed carbon content of coal is 82.5%, the fixed carbon content of coke powder i...
Embodiment 3
[0038] Example 3: High-speed tool steel M2Al (W6Mo5Cr4V2 Al) is smelted by direct alloying of tungsten ore on an electric arc furnace with a loading capacity of 10 tons. The process route adopted is: low-phosphorus scrap steel and carbon-containing tungsten ore balls are cold-packed in an electric furnace Group, silicon carbide SiC, adding ferromolybdenum → enter the melting period → enter the oxidation period → enter the reduction period → add ferrovanadium → add slag depleting agent SiC → add aluminum ingots, take out the furnace → carry out desulfurization and refining in LF furnace → carry out VD vacuum treatment → Perform pouring. The prepared carbon-containing tungsten ore pellets are composed of 80% tungsten ore, 16.5% reducing agent, 2% catalyst, and 1.5% binder. First, the tungsten ore, reducing agent, and catalyst are crushed and ground into 200 Mesh powder, then mix and add binder to make tungsten carbide pellets. The tungsten content of tungsten ore is 48.1%, the ...
PUM
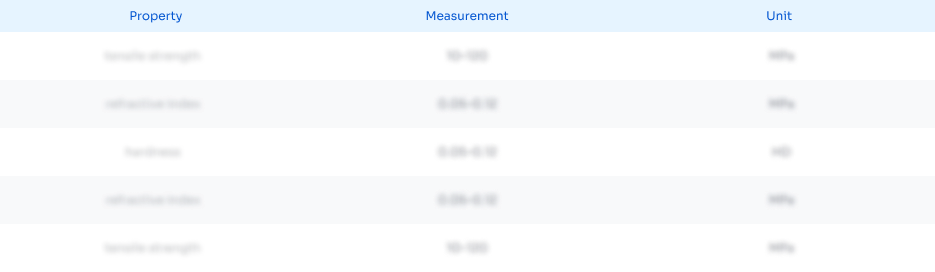
Abstract
Description
Claims
Application Information

- R&D
- Intellectual Property
- Life Sciences
- Materials
- Tech Scout
- Unparalleled Data Quality
- Higher Quality Content
- 60% Fewer Hallucinations
Browse by: Latest US Patents, China's latest patents, Technical Efficacy Thesaurus, Application Domain, Technology Topic, Popular Technical Reports.
© 2025 PatSnap. All rights reserved.Legal|Privacy policy|Modern Slavery Act Transparency Statement|Sitemap|About US| Contact US: help@patsnap.com