Preparation method for metallic phase sample of 1060 aluminium plate and MB3 magnesium alloy palate join
A technology for metallographic samples and magnesium alloy plates, applied in the field of material welding, can solve problems such as pits, difficulties in metallographic sample preparation, inability to accurately focus, etc., to achieve easy analysis, clear metallographic samples, and overcome over-corrosion. Effect
- Summary
- Abstract
- Description
- Claims
- Application Information
AI Technical Summary
Problems solved by technology
Method used
Examples
Embodiment 1
[0038] 1. Sampling
[0039] The welded joints of the 1060 aluminum plate and the MB3 magnesium alloy are cut into samples with a side length of 18mm and a height of 15mm with a grinding wheel slicer or a wire cutting machine.
[0040] 2. Grinding
[0041] (1) Coarse grinding
[0042] Roughly grind the sample prepared in step 1 with a grinder or file.
[0043] (2) fine grinding
[0044] After rough grinding, the grinding surface of the sample is manually finely ground with metallographic sandpaper or water sandpaper.
[0045] 3. Polishing
[0046] (1) Polishing machine for polishing
[0047] Polish the finely ground sample with a polishing machine. When polishing, wet the polishing fabric with water, spread it tightly and fix it on the polishing disc of the polishing machine, and sprinkle diamond polishing liquid with a particle size of 6um on the polishing disc. When the polishing fabric is wet, it is necessary to add an appropriate amount of diamond polishing liquid or ...
Embodiment 2
[0067] In the process steps of this embodiment, the welded joint between the 1060 aluminum plate and the MB3 magnesium alloy is cut into a sample with a side length of 15 mm and a height of 12 mm with a grinding wheel slicer or a wire cutting machine. In polishing step 3, the finely ground sample is polished with a polishing machine. During polishing, the polishing fabric is soaked with water, paved and tightened and fixed on the polishing disc of the polishing machine, and the diamond polishing liquid with a particle size of 1um is Sprinkle on the polishing disc until the polishing fabric is wet. When polishing, add an appropriate amount of diamond polishing liquid or water to maintain the humidity of the polishing disc. The pressure head of the polishing machine is 80 Newtons, and the speed of the polishing machine is 150 rpm minutes, the polishing time is 1.5 minutes. In step 4 of the etching process, the etching time for one side of the 1060 aluminum plate in the etching s...
Embodiment 3
[0073] In the process steps of this embodiment, the welded joint between the 1060 aluminum plate and the MB3 magnesium alloy is cut into a sample with a side length of 20 mm and a height of 18 mm with a grinding wheel slicer or a wire cutting machine. In polishing step 3, the finely ground sample is polished with a polishing machine. During polishing, the polishing fabric is soaked with water, paved and tightened and fixed on the polishing disc of the polishing machine, and the diamond polishing liquid with a particle size of 15um is Sprinkle it on the polishing disc until the polishing fabric is wet. When polishing, you need to add an appropriate amount of diamond polishing liquid or water to maintain the humidity of the polishing disc. minutes, the polishing time is 2 minutes. In step 4 of the etching process, the etching time for one side of the 1060 aluminum plate in the etching solution is 90 seconds. The ratio of the etching solution on one side of the MB3 magnesium all...
PUM
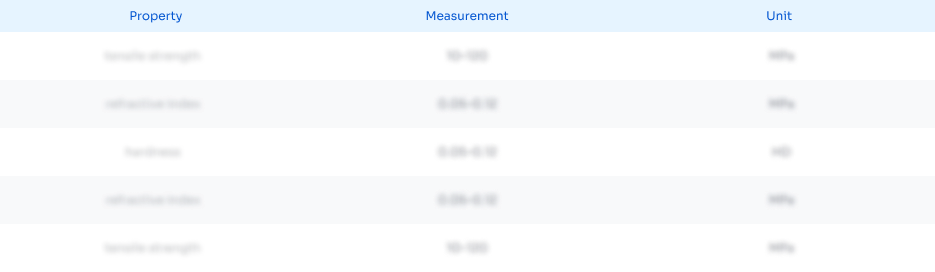
Abstract
Description
Claims
Application Information

- R&D
- Intellectual Property
- Life Sciences
- Materials
- Tech Scout
- Unparalleled Data Quality
- Higher Quality Content
- 60% Fewer Hallucinations
Browse by: Latest US Patents, China's latest patents, Technical Efficacy Thesaurus, Application Domain, Technology Topic, Popular Technical Reports.
© 2025 PatSnap. All rights reserved.Legal|Privacy policy|Modern Slavery Act Transparency Statement|Sitemap|About US| Contact US: help@patsnap.com