Manufacturing method of Fe-6.5Si alloy powder and manufacturing method of magnetic powder core
A technology of fe-6.5si and alloy powder, which is applied in the field of magnetic powder core manufacturing, can solve the problems of low yield and failure to realize industrial production, and achieve good formability and compressibility
- Summary
- Abstract
- Description
- Claims
- Application Information
AI Technical Summary
Problems solved by technology
Method used
Image
Examples
Embodiment 1
[0024] Put industrial pure iron, crystalline silicon, sponge titanium (or ferroniobium) into a nominal 50 kg vacuum induction furnace for smelting, and cast it into an alloy steel ingot with a chemical composition of 6.2% silicon, 0.3% titanium, and more than 0.02% C being Fe , use the hammering method to break it into material blocks below 40mm, put it into the jaw crusher and crush it into small pieces less than 5mm, and then enter the vibrating ball mill to grind it into alloy powders less than 120 mesh, and put it in a hydrogen-protected box-type electric furnace 900 Incubate at ℃ for 6 hours for annealing treatment, sieve with a vibrating sieve machine, and carry out particle size distribution according to the ratio of -120 mesh to +200 mesh accounting for 30%, -200 mesh to +300 mesh accounting for 50%, and -300 mesh accounting for 20%. Ratio, according to phosphoric acid 5%+ acetone 95% mass percent is made into solution again by the mass percent of alloy powder 94%, phos...
Embodiment 2
[0028] The process flow is the same as Example 1, the smelting composition is Si6.98%, Ti0.5%, C0.012%, and the rest is Fe. After being broken into alloy powder, the temperature is 1050 ° C, and the hydrogen reduction annealing treatment is kept for 3 hours, according to -120 mesh ~ +200 mesh accounts for 20%, -200 mesh to +300 mesh accounts for 60%, and -300 mesh accounts for 20% for particle size ratio. Make a solution with 15% acetone phosphate (that is, 15% phosphoric acid + 85% acetone), mix 98% of the alloy powder, 2% of the above acetone phosphate solution, and keep stirring until the acetone is completely volatilized and the alloy powder is dry before adding Insulation agent 0.4% kaolin, 0.6% FK155 adhesive, 0.2% M 0 S 2 After the lubricant is evenly mixed, then mix evenly with 0.8% barium stearate (release agent), and then it can be loaded into the feeding box of a 100t hydraulic dry powder automatic molding machine, according to 21t / cm 2 Compression molding under p...
Embodiment 3
[0030] The process flow is the same as in Example 1. The smelting chemical composition is shown in the table below. The annealing temperature of the alloy powder is 950°C for 4 hours and the concentration of acetone phosphate is 10%. The addition amount is 4% (mass percentage) of the alloy powder. Its chemical composition changes and magnetic properties are shown in Table 3:
[0031] chemical composition
PUM
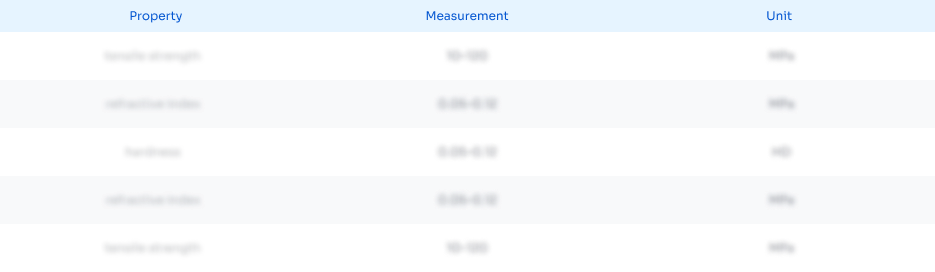
Abstract
Description
Claims
Application Information

- Generate Ideas
- Intellectual Property
- Life Sciences
- Materials
- Tech Scout
- Unparalleled Data Quality
- Higher Quality Content
- 60% Fewer Hallucinations
Browse by: Latest US Patents, China's latest patents, Technical Efficacy Thesaurus, Application Domain, Technology Topic, Popular Technical Reports.
© 2025 PatSnap. All rights reserved.Legal|Privacy policy|Modern Slavery Act Transparency Statement|Sitemap|About US| Contact US: help@patsnap.com