Golf ball having reduced surface hardness
a golf ball and surface hardness technology, applied in the field of golf balls, can solve the problems of reducing the spin imparted, reducing the softness of the surface, and reducing the compression and spin rate of the wound golf ball, so as to reduce the hardness measurement, improve the free volume, and soften the crosslinked network
- Summary
- Abstract
- Description
- Claims
- Application Information
AI Technical Summary
Benefits of technology
Problems solved by technology
Method used
Image
Examples
Embodiment Construction
[0087]The golf ball of the invention may comprise cover layer comprising a thermoplastic composition. The thermoplastic material may comprise ethylene / acrylic acid copolymers, ethylene / methacrylic acid copolymers, ethylene / methyl acrylate / acrylic acid terpolymers, ethylene / n-butyl acrylate / methacrylic acid terpolymers, ethylene / isobutyl-acrylate / methacrylic acid terpolymers, or blends thereof.
[0088]The cover layer may further comprise a thermoplastic polyurethane, a thermoplastic polyurea, a styrene block copolymer, a polyester amide, polyester-ester, polyamides, single-site catalyzed polymers, metallocene-catalyzed polymers, polyesters, poly(ethylene terephthalate), poly(butylene terephthalate), poly(propylene terephthalate), poly(trimethylene terephthalate), poly(ethylene naphthenate), polystyrene polymers, poly(styrene-co-maleic anhydride), acrylonitrile-butadiene-styrene, poly(styrene sulfonate), polyethylene styrene, grafted polypropylenes, grafted polyethylenes, polyvinyl chlo...
PUM
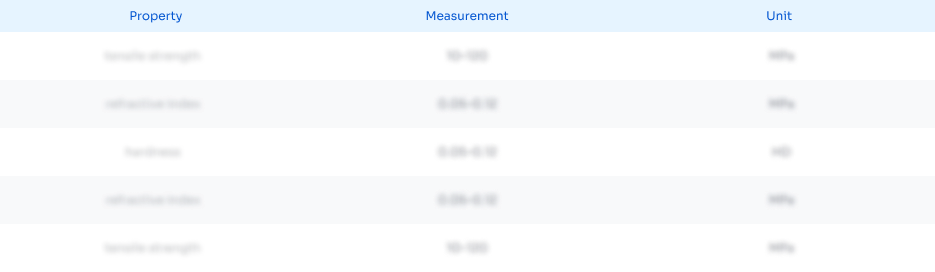
Abstract
Description
Claims
Application Information

- R&D
- Intellectual Property
- Life Sciences
- Materials
- Tech Scout
- Unparalleled Data Quality
- Higher Quality Content
- 60% Fewer Hallucinations
Browse by: Latest US Patents, China's latest patents, Technical Efficacy Thesaurus, Application Domain, Technology Topic, Popular Technical Reports.
© 2025 PatSnap. All rights reserved.Legal|Privacy policy|Modern Slavery Act Transparency Statement|Sitemap|About US| Contact US: help@patsnap.com