Carbon-silicon carbide base composite material toughened by carbon fiber and its preparation method
A composite material, silicon carbide-based technology, applied in chemical instruments and methods, layered products, ceramic layered products, etc., can solve the problem that the thermal expansion matching of carbon fiber and silicon carbide matrix is not ideal, affecting the mechanical and thermal properties of composite materials Restricting the development of composite materials and other issues, to achieve the effect of convenient structural design and optimization, reduced elastic modulus, and good thermal expansion matching
- Summary
- Abstract
- Description
- Claims
- Application Information
AI Technical Summary
Problems solved by technology
Method used
Examples
Embodiment 1
[0015] (1) Soak the continuous carbon fiber braid in acetone for about 30 minutes, remove the carbon fiber surface treatment agent epoxy resin, dry at low temperature, and remove the acetone solvent. Then impregnate the carbon fiber braid by vacuum-pressure method;
[0016] (2) 100g boron phenolic aldehyde and 100g alcohol miscible, be mixed with organic precursor solution;
[0017] (3) Place the carbon fiber braid in a pre-prepared mold, fix the braid on the mold with cotton thread, take it out after impregnating for a period of time, transfer the sample to an autoclave, heat up to 50°C, and maintain a vacuum of 0.5 h, then add 6MPa air pressure, keep it for 1h, then raise the temperature to 180°C for pre-curing for 2h, and finally raise the temperature to 230°C for post-curing, and then put the sample in a pit furnace at 1000°C, N 2 Medium cracking 6h;
[0018] (4) configuration mass ratio is the polycarbosilane / vinylbenzene solution of 1: 0.4;
[0019] (5) Place the carb...
Embodiment 2
[0022] (1) Soak the continuous carbon fiber braid in acetone for about 30 minutes, remove the carbon fiber surface treatment agent epoxy resin, dry at low temperature, and remove the acetone solvent. Then impregnate the carbon fiber braid by vacuum-pressure method;
[0023] (2) 100g boron phenolic aldehyde and 100g alcohol miscible, be mixed with organic precursor solution;
[0024] (3) Place the carbon fiber braid in a pre-prepared mold, fix the braid on the mold with cotton thread, take it out after impregnating for a period of time, transfer the sample to an autoclave, heat up to 50°C, and maintain a vacuum of 0.5 h, then add 6MPa air pressure, keep it for 1h, then raise the temperature to 180°C for pre-curing for 2h, and finally raise the temperature to 230°C for post-curing, and then put the sample in a pit furnace at 1000°C, N 2 Medium cracking 6h;
[0025] (4) Carry out the process described in step (3) once again;
[0026] (5) configure a polycarbosilane / vinylbenzen...
Embodiment 3
[0031] (1) Soak the short-fiber rolled carbon felt in acetone for about 30 minutes, remove the carbon fiber surface treatment agent epoxy resin, dry at low temperature, and remove the acetone solvent. The short fiber rolled carbon felt is then impregnated by vacuum-pressure method;
[0032] (2) 100g boron phenolic aldehyde and 100g alcohol miscible, be mixed with organic precursor solution;
[0033] (3) Place the short-fiber rolled carbon felt in a pre-prepared mold, fix the carbon felt on the mold with cotton thread, take it out after impregnating for a period of time, transfer the sample to an autoclave, and heat up to 50°C. Keep vacuuming for 0.5h, then add 6MPa air pressure, keep it for 1h, then raise the temperature to 180°C for pre-curing for 2h, and finally raise the temperature to 230°C for post-curing, then put the sample in a pit furnace at 1000°C, N 2 Medium cracking 6h;
[0034] (4) configuration mass ratio is the polycarbosilane / vinylbenzene solution of 1: 0.4; ...
PUM
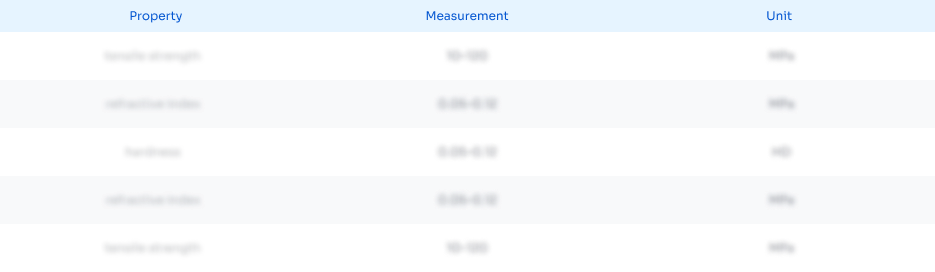
Abstract
Description
Claims
Application Information

- R&D
- Intellectual Property
- Life Sciences
- Materials
- Tech Scout
- Unparalleled Data Quality
- Higher Quality Content
- 60% Fewer Hallucinations
Browse by: Latest US Patents, China's latest patents, Technical Efficacy Thesaurus, Application Domain, Technology Topic, Popular Technical Reports.
© 2025 PatSnap. All rights reserved.Legal|Privacy policy|Modern Slavery Act Transparency Statement|Sitemap|About US| Contact US: help@patsnap.com