Er,Zr composite rein forced Al-Mg-Mn alloy
A technology for alloys and final products, applied in the field of aluminum alloy materials, can solve problems such as no reports, and achieve high-temperature mechanical properties and improve mechanical properties.
- Summary
- Abstract
- Description
- Claims
- Application Information
AI Technical Summary
Problems solved by technology
Method used
Image
Examples
example 1
[0012] Example 1: adopt Al-6%Er master alloy, 2.3% Al-4.52%Zr master alloy, 6.98% Al-10.02%Mn master alloy and 4.8% pure magnesium accounting for 3.33% of the total weight of the alloy, and the rest are Raw material of pure aluminum, ingot metallurgy, covered with covering agent, C 6 Cl 6 Degassing and refining, smelting in a crucible resistance furnace to form an alloy ingot with a composition of Al-4.5%Mg-0.7%Mn-0.2%Er-0.1%Zr. The ingot is homogenized and annealed at 480°C for 24 hours, then cut and milled, diathermy (470°C for 1 hour) and hot rolled (78% of the total reduction), cooled to room temperature and then intermediate annealed (470°C for 1 hour) And cold rolled (67% total reduction) to produce a 1.5mm thick plate, and its mechanical properties were measured. The results are shown in Table 1 for alloy C.
example 2
[0013] Example 2: adopt Al-6%Er master alloy, 2.3% Al-4.52%Zr master alloy, 6.98% Al-10.02%Mn master alloy and 4.8% pure magnesium accounting for 6.67% of the total weight of the alloy, and the rest are Raw material of pure aluminum, ingot metallurgy, covered with covering agent, C 6 Cl 6 Degassing and refining, smelting in a crucible resistance furnace to form an alloy ingot with a composition of Al-4.5%Mg-0.7%Mn-0.4%Er-0.1%Zr. The ingot was homogenized and annealed at 480°C for 24 hours, then cut and face milled, diathermy (470°C for 1 hour) and hot rolled (78% of the total reduction), cooled to room temperature and then intermediate annealed (470°C for 1 hour) And cold rolled (67% total reduction) to produce a 1.5mm thick plate, and its mechanical properties were measured. The results are shown in Table 1 for alloy D.
example 3
[0014] Example 3: adopt Al-6%Er master alloy, 2.3% Al-4.52%Zr master alloy, 6.98% Al-10.02%Mn master alloy and 4.8% pure magnesium accounting for 10% of the total weight of the alloy, and the rest are Raw material of pure aluminum, ingot metallurgy, covered with covering agent, C 6 Cl 6 Degassing and refining, smelting in a crucible resistance furnace to form an alloy ingot with a composition of Al-4.5%Mg-0.7%Mn-0.6%Er-0.1%Zr. The ingot was homogenized and annealed at 480°C for 24 hours, then cut and face milled, diathermy (470°C for 1 hour) and hot rolled (78% of the total reduction), cooled to room temperature and then intermediate annealed (470°C for 1 hour) And cold rolled (67% total reduction) to produce a 1.5mm thick plate, and its mechanical properties were measured. The results are shown in Table 1 for E alloy.
PUM
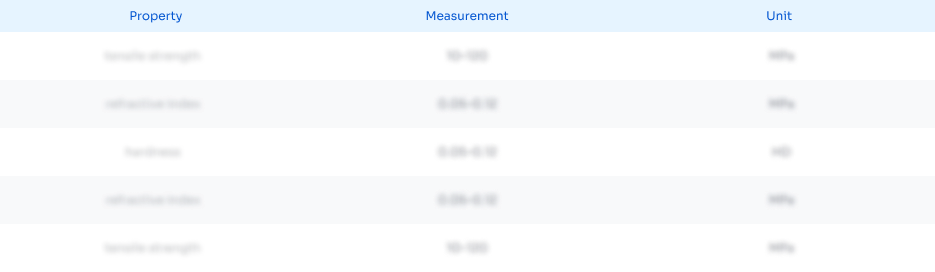
Abstract
Description
Claims
Application Information

- R&D
- Intellectual Property
- Life Sciences
- Materials
- Tech Scout
- Unparalleled Data Quality
- Higher Quality Content
- 60% Fewer Hallucinations
Browse by: Latest US Patents, China's latest patents, Technical Efficacy Thesaurus, Application Domain, Technology Topic, Popular Technical Reports.
© 2025 PatSnap. All rights reserved.Legal|Privacy policy|Modern Slavery Act Transparency Statement|Sitemap|About US| Contact US: help@patsnap.com