Hard alloy composite roll collar for high-speed wire production line and method for manufacturing the same
A technology of cemented carbide and composite rolls, which is used in metal rolling, manufacturing tools, metal rolling, etc. to achieve the effects of good performance, improved service life, and improved wear resistance.
- Summary
- Abstract
- Description
- Claims
- Application Information
AI Technical Summary
Problems solved by technology
Method used
Image
Examples
Embodiment Construction
[0037] Below in conjunction with accompanying drawing and embodiment the present invention is further described:
[0038] image 3 Shown is an embodiment of the high-wire cemented carbide composite roll ring of the present invention, B in the figure represents the composite working layer, and C represents the matrix part of the composite roll ring. The workpiece specification is Φ228.3mm, the hardness of the working layer B is 87HRA, and the density is 14.3 / cm3 tungsten carbide powder, and the tungsten carbide material of the roller ring base C has a hardness of 85HRA and a density of 13.9g / cm 3 The double-grade materials are sintered into one body through a composite process, and then processed into a composite roller ring by grinding. For another example, the workpiece specification is Φ168.66mm, the hardness of the tungsten carbide cemented carbide material of the roller ring base is 85HRA, and the density is 13.9g / cm 3 , the working layer tungsten carbide hard alloy mate...
PUM
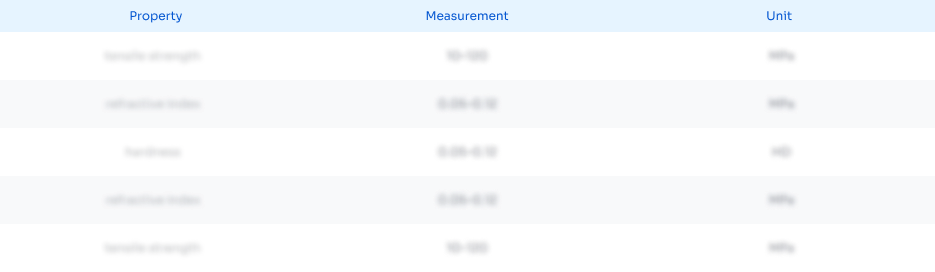
Abstract
Description
Claims
Application Information

- R&D Engineer
- R&D Manager
- IP Professional
- Industry Leading Data Capabilities
- Powerful AI technology
- Patent DNA Extraction
Browse by: Latest US Patents, China's latest patents, Technical Efficacy Thesaurus, Application Domain, Technology Topic, Popular Technical Reports.
© 2024 PatSnap. All rights reserved.Legal|Privacy policy|Modern Slavery Act Transparency Statement|Sitemap|About US| Contact US: help@patsnap.com