Coal tar hydrogenating modification catalyst and its prepn and application
A hydrogenation modification and catalyst technology, applied in tar processing, petroleum industry, refined hydrocarbon oil, etc., can solve the problem of low activity, achieve strong aromatics saturation and ring-opening ability, good stability and mechanical strength, good The effect of hydrodesulfurization
- Summary
- Abstract
- Description
- Claims
- Application Information
AI Technical Summary
Problems solved by technology
Method used
Examples
Embodiment 1
[0020] Add zirconium nitrate to deionized water at room temperature to make a solution. The composition of the solution is: 5g zirconium nitrate / 50ml. Add Y-type molecular sieves to the solution, and add 25g molecular sieves to the 50ml solution. Stir evenly, let stand at room temperature for 10 hours, and then dry it at 80°C. The drying time is 8 hours. Take it out, grind it, and pass through a 100-mesh sieve.
[0021] Mix 150g of pseudo-boehmite, 60g of silica sol, and 25g of modified Y-type molecular sieve evenly, then add 4g of scallop powder, appropriate amount of nitric acid, deionized water, etc., and knead to form. Drying is carried out at a temperature of 90° C., and the drying time is 8 hours. After that, it is fired at a temperature of 600°C. The calcination time is 4 hours, and the carrier is made. Its shape is cylindrical. Put the molded carrier into the treatment furnace, at 800°C, the water vapor space velocity is 6h -1 Under certain conditions, water va...
Embodiment 2
[0023] Add ammonium dihydrogen phosphate to deionized water at room temperature to make a solution. The composition of the solution is: 10g ammonium dihydrogen phosphate / 50ml. Add Y-type molecular sieves to the solution, and add 25g molecular sieves to the 50ml solution. Stir well, stand at room temperature for 4 hours, and then dry it at 140°C. The drying time is 4 hours. Take it out, grind it, and pass through a 140-mesh sieve.
[0024] Mix 150g of pseudo-boehmite, 60g of silica sol, and 25g of modified Y-type molecular sieve evenly, then add 5g of scallop powder, an appropriate amount of nitric acid, deionized water, etc., and knead to form it. Drying is carried out at a temperature of 120° C., and the drying time is 6 hours. After that, it is fired at a temperature of 500°C. The calcination time is 10 hours, and the carrier is made. Its shape is clover-shaped. Put the molded carrier into the treatment furnace, at 600°C, the water vapor space velocity is 4h -1 Under...
Embodiment 3
[0026] Add ammonium metatungstate and nickel nitrate into deionized water, and the solution composition is 80g ammonium metatungstate / 100ml, 30g nickel nitrate / 100ml. Immerse 100g of carrier A in 200ml of the above solution, soak at 15°C for 2h, filter and let stand at room temperature for 2h, then dry at 110°C for 8h, and then calcined at 460°C for 10h to prepare catalyst A1. Its properties are shown in Table 1.
PUM
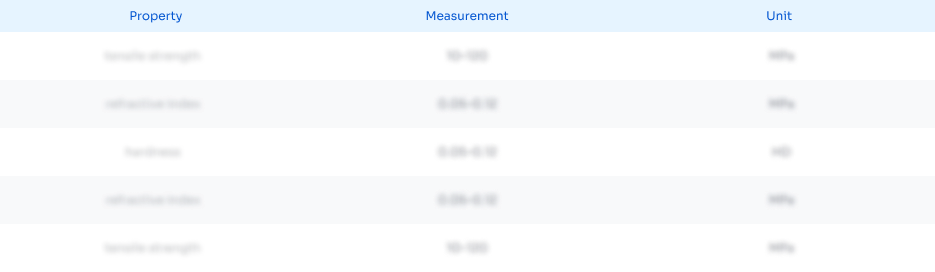
Abstract
Description
Claims
Application Information

- Generate Ideas
- Intellectual Property
- Life Sciences
- Materials
- Tech Scout
- Unparalleled Data Quality
- Higher Quality Content
- 60% Fewer Hallucinations
Browse by: Latest US Patents, China's latest patents, Technical Efficacy Thesaurus, Application Domain, Technology Topic, Popular Technical Reports.
© 2025 PatSnap. All rights reserved.Legal|Privacy policy|Modern Slavery Act Transparency Statement|Sitemap|About US| Contact US: help@patsnap.com