Catalyst used for hydrating epoxy ethane to prepare ethandiol
A technology of ethylene oxide hydration and catalyst, which is applied in the direction of metal/metal oxide/metal hydroxide catalyst, physical/chemical process catalyst, hydroxyl addition preparation, etc. Acid catalyst poor stability, high reaction water ratio and other problems, to achieve the effect of long life, high selectivity, low operating water ratio
- Summary
- Abstract
- Description
- Claims
- Application Information
AI Technical Summary
Problems solved by technology
Method used
Examples
Embodiment 1
[0039] Fully mix 113 grams of aluminum hydroxide powder, 5 grams of graphite, and 5 grams of squash powder, then add 60 milliliters of 4% (weight) dilute nitric acid, fully knead in a kneader to form a lump material, and extrude , dried at room temperature for 24 hours, dried at 150°C for 2 hours, and calcined at 1200°C for 4 hours to obtain strip-shaped α-Al 2 o 3 carrier. The oxalic acid solution containing 6.25 grams of niobic acid is impregnated on the prepared carrier, dried at 120°C for 2 hours; then ammonium metavanadate is dissolved in 5% (weight) hydrogen peroxide, impregnated on the catalyst again, dried at 120°C for 2 hours Hours; Finally, impregnate the catalyst with an aqueous solution of lanthanum trichloride and dry at 120°C for 2 hours. The above catalyst precursor was calcined in air at 700° C. for 4 hours to obtain catalyst A. The catalyst composition is shown in Table 1.
Embodiment 2
[0041] Fully mix 67.6 grams of aluminum hydroxide, 40 grams of silicon dioxide, 8 grams of graphite, and 4 grams of cyclodextrin, then add 60 milliliters of 4% (weight) dilute nitric acid, and fully knead in a kneader to form a lump material , extruded, dried at 150°C for 2 hours, and calcined at 1400°C for 4 hours to obtain a strip-shaped carrier. Use a certain concentration of ammonium molybdate solution of 125 mmol / L to impregnate the above-mentioned carrier at room temperature, the volume ratio of impregnated liquid to solid is 2:1, impregnate for 2 hours, filter the solution, and dry in vacuum at 120°C for 2 hours; then use a certain 15% niobium ammonium complex solution (NH 4 [NbO(C 2 o 4 ) 2 (H 2 O) 2 ]·(H 2 O) n ) continue to impregnate the above-mentioned treated carrier at room temperature, the impregnating liquid-solid volume ratio is 2:1, the impregnating time is 2 hours, the solution is filtered off, and vacuum-dried at 120° C. for 2 hours, thus performing ...
Embodiment 3
[0043] Fully mix 40.5 grams of commercially available niobium oxalate, 15 grams of polyvinyl alcohol, 8 grams of precipitated sulfur, the required ammonium tungstate and 100 grams of titanium dioxide to obtain a mixture, then add an appropriate amount of water, and fully knead in a kneader to form Agglomerate material, extruded into strips, dried at 200°C for 3 hours, then impregnated with praseodymium trichloride solution with a concentration of 0.12 mol / liter into the above catalyst, dried at 150°C for 2 hours, and roasted in a carbon dioxide atmosphere at 400°C for 4 hours. hours, to obtain catalyst C. The catalyst composition is shown in Table 1.
PUM
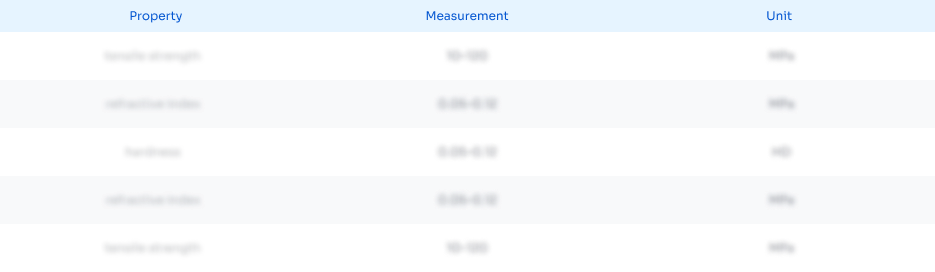
Abstract
Description
Claims
Application Information

- Generate Ideas
- Intellectual Property
- Life Sciences
- Materials
- Tech Scout
- Unparalleled Data Quality
- Higher Quality Content
- 60% Fewer Hallucinations
Browse by: Latest US Patents, China's latest patents, Technical Efficacy Thesaurus, Application Domain, Technology Topic, Popular Technical Reports.
© 2025 PatSnap. All rights reserved.Legal|Privacy policy|Modern Slavery Act Transparency Statement|Sitemap|About US| Contact US: help@patsnap.com