Method for fabrication food wrap paper and cultural paper by using corn stalk to make no chlorin bleached pulp
A technology for food wrapping paper and cultural paper, applied in the fields of food wrapping paper and paperboard, cultural paper and paperboard, can solve the problem of not emphasizing alkali strengthening, and achieve the improvement of whiteness, environmental protection quality and environmental protection. Effect
- Summary
- Abstract
- Description
- Claims
- Application Information
AI Technical Summary
Problems solved by technology
Method used
Examples
example 1
[0032] The cooking uses corn stalks as the raw material, after being cut, dusted, and pre-soaked, then put into the cooker. The weight percentage of the medicine to the absolutely dry corn stalks is:
[0033] Ammonium sulfite 15~20%
[0034] Potassium sulfite 3~7%
[0035] Urea 1.5~3.5%
[0036] Sulfur 0.5~2%
[0037] The process conditions of steaming ball cooking are: liquid ratio 2.8, heating time 1 hour, heating to 160°C, and heat preservation for 2 hours.
[0038] Pulp bleaching adopts a hydrogen peroxide bleaching process with simultaneous reinforcement of oxygen and alkali and urea activation. The bleaching process is:
[0039] The weight percentage of the medicine to the absolute dry unbleached pulp is:
[0040] Hydrogen peroxide 0.5~2%
[0041] Urea 0.4~1.5%
[0045] Pulp concentration 8%
[0046] Oxygen flow under 0.5MPa oxygen pressure
[0047] Treated at 80°C for 1 hour to obta...
example 2
[0049] Steaming uses depithed corn stalks as raw materials, cuts, dusts, and presoaks, and then puts them into the digester. The weight percentage of the medicine to the absolutely dry depithed cornstalk is:
[0050] Ammonium sulfite 15~24%
[0051] Potassium sulfite 3~10%
[0052] Urea 1~4%
[0053] Sulfur 0.35~3%
[0054] The process conditions of steaming ball cooking are: liquid ratio 2.8, heating time 1 hour, heating to 165°C, holding for 2 hours,
[0055] Pulp bleaching adopts the hydrogen peroxide bleaching process in which oxygen and alkali are simultaneously strengthened and urea is activated. The process conditions are:
[0056] The weight percentage of the medicine to the absolute dry unbleached pulp is:
[0057] Hydrogen peroxide 0.8~3%
[0058] Urea 0.5~2%
[0059] Magnesium sulfate 0.3~1%
[0061] Sodium hydroxide 2.5~7%
[0062] Pulp concentration 8%
[0063] Oxygen flow under the oxygen pressure of 0.5MPa
[0064] Treated at 90°C for 1....
example 3
[0066] Using de-pithed corn stalk as raw material, after cutting, dusting and pre-soaking, put it into the digester, the weight percentage of the medicine to the absolutely dry de-pithed corn stalk is:
[0067] Sodium sulfite 12~20%
[0068] Potassium sulfite 2~5%
[0069] Sodium hydroxide 1.5~5%
[0070] Sulfur 0.3~1%
[0071] The process conditions of steaming ball cooking are: liquid ratio 3, heating time 1 hour, heating to 155°C, and heat preservation for 2 hours.
[0072] Pulp bleaching adopts a hydrogen peroxide bleaching process in which oxygen and alkali are simultaneously strengthened and urea is activated. The process conditions are:
[0073] The weight percentage of the medicine to the absolute dry unbleached pulp is
[0074] Hydrogen peroxide 0.8~2%
[0075] Urea 0.5~1%
[0076] Magnesium sulfate 0.3~1%
[0077] Sodium silicate 1~3%
[0078] Sodium hydroxide 1.5~5%
[0079] Pulp concentration 8%
[0080] Oxygen flow under the oxygen pressure of 0.5MPa
[0081] Treated ...
PUM
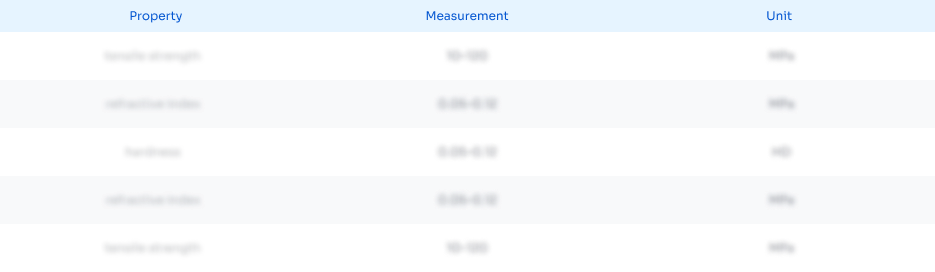
Abstract
Description
Claims
Application Information

- R&D
- Intellectual Property
- Life Sciences
- Materials
- Tech Scout
- Unparalleled Data Quality
- Higher Quality Content
- 60% Fewer Hallucinations
Browse by: Latest US Patents, China's latest patents, Technical Efficacy Thesaurus, Application Domain, Technology Topic, Popular Technical Reports.
© 2025 PatSnap. All rights reserved.Legal|Privacy policy|Modern Slavery Act Transparency Statement|Sitemap|About US| Contact US: help@patsnap.com