Catalyst of catalyzing, cracking for reducing sulfur content in gasoline and preparation process thereof
A catalytic cracking and catalyst technology, applied in catalytic cracking, cracking, petroleum industry, etc., can solve the problems of reducing the sulfur content of gasoline, increasing the consumption of catalysts, and poor stability of additives or catalysts
- Summary
- Abstract
- Description
- Claims
- Application Information
AI Technical Summary
Problems solved by technology
Method used
Examples
Embodiment 1
[0044] Add water to 10Kg (dry basis) of the original kaolin to make a slurry with a solid content of 35%, and add 2.5Kg of sodium silicate as a dispersant for spray molding to obtain 8.5Kg of spray microspheres. The sprayed microspheres were calcined in a muffle furnace at 940° C. for 3 hours to obtain calcined microspheres. In the stirring state, sodium silicate 500ml, lye 670ml, zeolite directing agent (containing 11.65% SiO 2 , 1.32% Al 2 o 3 , 12.89% Na 2 (2) 125ml, 200ml of deionized water, and 1200g of roasted microspheres were put into a stainless steel reactor, and the temperature was raised to 90° C. and crystallized at a constant temperature for 24 hours. After the crystallization is completed, the mother liquor is removed by filtration, and the filter cake is washed and dried to obtain crystallized product microspheres. As determined by X-ray diffraction, the crystallization product microspheres contained 23% NaY zeolite, and the zeolite silicon-aluminum ratio (...
Embodiment 2
[0046] All reaction raw materials are the same as in Example 1. Under stirring, sodium silicate 450ml, lye 706ml, guiding agent 160ml, deionized water 160ml, copper nitrate 100g, ferrous chloride 20g, zirconium chloride 12g, and roasted microspheres 1100g Put it into a stainless steel reactor, raise the temperature to 90°C and conduct crystallization at constant temperature for 20 hours. X-ray diffraction determined that the crystallized product contained 19% NaY zeolite, and the zeolite silicon-aluminum ratio was 5.2. The crystallized product microspheres were subjected to ion exchange and high-temperature calcination treatment in the same manner as in Example 1, except that: three cross-linked rare earths / one roasting material=3. The final microsphere sodium oxide content is 0.75%, and the rare earth oxide content is 2.5%, and the catalyst B of the present invention is obtained.
Embodiment 3
[0048] Adding water to 10Kg (dry basis) former kaolin to make a slurry with a solid content of 20%, and adding 0.2Kg sodium hydroxide, 0.2Kg sodium pyrophosphate, and 0.1Kg sodium hexametaphosphate as a dispersant, sprayed into microspheres, and obtained 8Kg of spray microspheres. A part of the sprayed microspheres was calcined in a muffle furnace at 950°C for 1 hour to obtain calcined microspheres A, and a part was calcined at 700°C for 1 hour to obtain calcined microspheres B. While stirring, put 3000ml of sodium silicate, 900ml of lye, 90ml of zeolite directing agent, 200ml of deionized water, and 500g of roasted microspheres A and B into a stainless steel reactor in sequence, raise the temperature to 90°C and crystallize at constant temperature for 24 hours. After the crystallization is completed, the mother liquor is removed by filtration, and the filter cake is washed and dried to obtain crystallized product microspheres. As determined by X-ray diffraction, the crystall...
PUM
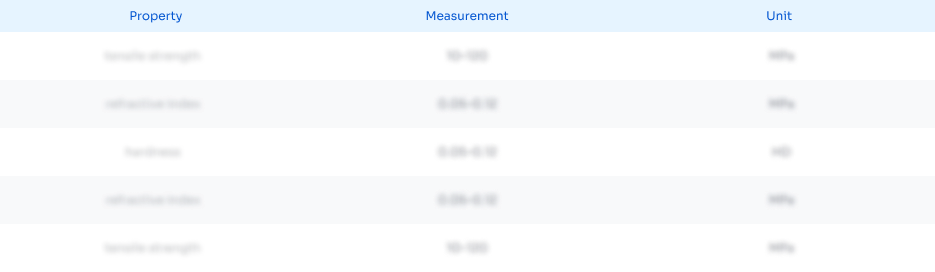
Abstract
Description
Claims
Application Information

- R&D
- Intellectual Property
- Life Sciences
- Materials
- Tech Scout
- Unparalleled Data Quality
- Higher Quality Content
- 60% Fewer Hallucinations
Browse by: Latest US Patents, China's latest patents, Technical Efficacy Thesaurus, Application Domain, Technology Topic, Popular Technical Reports.
© 2025 PatSnap. All rights reserved.Legal|Privacy policy|Modern Slavery Act Transparency Statement|Sitemap|About US| Contact US: help@patsnap.com