Method for treating coated layer on surface of metal material and making pattern
The technology of a metal material and a manufacturing method, which is applied to the device, coating, pretreatment surface and other directions of coating liquid on the surface, can solve the problems of easy to stick to oil fume, easy to change color, not resistant to chemical corrosion, etc., and achieve low production cost. , Soft and bright color, strong anti-oxidation effect
- Summary
- Abstract
- Description
- Claims
- Application Information
AI Technical Summary
Problems solved by technology
Method used
Examples
Embodiment 1
[0024] 1. Use the selected semi-hard or full-hard copper with a thickness of 20 wires; 2. Use 3% H for the copper 2 SO 4 Soak the solution for 30-40 seconds, rinse with water after soaking; 3. After natural drying, use 5% acetone, 30% benzene, and 15% n-propyl acetate to smear (artificially or mechanically) the surface, then use P8 Blow the surface with a pressure air machine; 4. After drying, use a thyristor far-infrared heating device to heat at 180°C for 40 minutes; 5. Electrostatically spray 40% polyester epoxy powder coating on the heated copper surface, spray After it is finished, heat it again at 175°C for 40 minutes with silicon controlled silicon far-infrared heating equipment; 6. Mix and mix well with 25% epoxy resin powder, 15% butyl acetate, and 30% industrial paint masterbatch, and roll coating or manual Carry out surface production and make patterns; 7. Use thyristor far-infrared heating equipment to heat at 180°C for 60 minutes; 8. After heating, spray 20% BJS ...
Embodiment 2
[0026] 1. Select an aluminum alloy plate with an aluminum content of more than 80% and a thickness of 20-80 wires, semi-hard or full-hard; 2. Use 3.5% H for the aluminum alloy 2 SO 4 Soak the solution for 30-50 seconds, rinse with water after soaking; 3. After natural drying, use 10% acetone, 40% benzene, and 20% n-propyl acetate to smear (artificially or mechanically) the surface, then use P8 Blow the surface with a high-pressure air compressor; 4. After drying, use a thyristor far-infrared heating device to heat at 180°C for 40 minutes; 5. Spray 60% polyester epoxy powder coating on the heated aluminum alloy surface. Again use silicon controlled rectifier far-infrared heating equipment to heat at 175°C for 50 minutes; 6. Use 30% epoxy resin powder, 30% butyl acetate, and 20% industrial paint color masterbatch to make patterns by rolling or by hand. Heating was performed at 150° C. for 60 minutes with a heating device. 7. Spray 30% BJS varnish on the surface of the heated a...
Embodiment 3
[0028] 1. Choose semi-hard or full-hard iron with a thickness of 40 wires; 2. Put the iron in 3% H 2 Soak in SO4 solution for 30-40 seconds, rinse with water after soaking; 3. After natural drying, use 8% acetone, 35% benzene, and 17% n-propyl acetate to smear (artificially or mechanically) the surface, then use Blow the surface with a P8 pressure air machine; 4. After drying, use a silicon controlled silicon far-infrared heating device to heat at 175°C for 50 minutes; 5. Spray 50% polyester epoxy powder coating on the heated iron surface, and then spray it again Use thyristor far-infrared heating equipment to heat at 150°C for 40 minutes; 6. Use 20% epoxy resin powder, 25% butyl acetate, and 30% industrial paint color masterbatch to make the surface and pattern by hand. Use thyristor far-infrared heating equipment to heat at 150°C for 40 minutes; 7. Use a spraying machine to spray 25% BJS varnish on the iron surface, and then use thyristor far-infrared heating equipment to he...
PUM
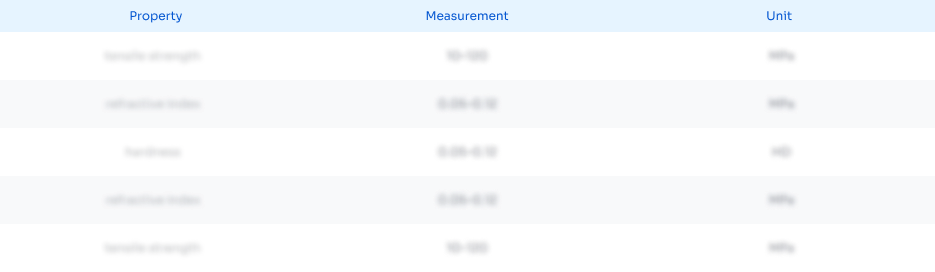
Abstract
Description
Claims
Application Information

- Generate Ideas
- Intellectual Property
- Life Sciences
- Materials
- Tech Scout
- Unparalleled Data Quality
- Higher Quality Content
- 60% Fewer Hallucinations
Browse by: Latest US Patents, China's latest patents, Technical Efficacy Thesaurus, Application Domain, Technology Topic, Popular Technical Reports.
© 2025 PatSnap. All rights reserved.Legal|Privacy policy|Modern Slavery Act Transparency Statement|Sitemap|About US| Contact US: help@patsnap.com