Nano-class conversion fluorescence material on fluoride matrix and its preparing process
A fluorescent material and fluoride technology, applied in the field of nano fluorescent materials and their preparation, can solve the problems of high calcination temperature and small particle size range, and achieve the effects of low calcination temperature, uniform particle size and high repeatability
- Summary
- Abstract
- Description
- Claims
- Application Information
AI Technical Summary
Problems solved by technology
Method used
Image
Examples
Embodiment 1
[0032] (1) Weigh 11.2905 grams of yttrium oxide, add enough hydrochloric acid (or nitric acid), heat to dissolve and evaporate to dryness. Add 500 ml of deionized water to dissolve, and the concentration of yttrium ions in the solution is 0.2 mol.L-1 at this time, which can be stored as a stock solution for a long time. Same as above, respectively weigh 18.125 g of gadolinium oxide, 16.3 g of lanthanum oxide, 19.7 g of ytterbium oxide, 19.1 g of erbium oxide, 19.3 g of thulium oxide, and 18.9 g of holmium oxide, each of which is made into 500 ml of 0.2 mol.L -1 stock solution. Take 16 milliliters of yttrium ion solution, 3.4 milliliters of ytterbium ion solution, and 0.6 milliliter of erbium ion solution in proportion, and place them in a 100 milliliter three-necked bottle. At this time, the molar ratio of rare earth ions in the solution is yttrium ion: ytterbium ion: erbium ion=80:17:3;
[0033] (2) In the above product, add 0.2 mol.L -1 20 ml of ethylenediaminetetraacetic...
Embodiment 2
[0038] (1) Take 17.4 milliliters of yttrium ion solution, 2.6 milliliters of ytterbium ion solution, and 0.02 milliliter of thulium ion solution in proportion, and place them in a 100 milliliter three-necked bottle. At this time, the molar ratio of rare earth ions in the solution is yttrium ion:ytterbium ion:thulium ion=87:13:0.1;
[0039] (2) In the above product, add 0.2mol.L -1 15 ml of ethylenediaminetetraacetic acid (EDTA) disodium salt solution;
[0040] (3) Weigh 2.1 g of sodium fluoride, add 65 ml of deionized water, and prepare an aqueous solution. At room temperature, under rapid stirring, the solution of step (2) was injected to form a precipitate, and the stirring reaction was continued for 1 hour;
[0041] (4) centrifugal separation and precipitation and washing with water three times, drying, and making a precursor;
[0042] (5) Putting the precursor into a high-temperature furnace and calcining at 400° C. for 4 hours to obtain a nano-scale up-conversion fluor...
Embodiment 3
[0044] (1) Take 16 milliliters of yttrium ion solution, 3.86 milliliters of ytterbium ion solution, and 0.04 milliliter of holmium ion solution in proportion, and place them in a 100 milliliter three-necked bottle. At this time, the molar ratio of rare earth ions in the solution is yttrium ion:ytterbium ion:holmium ion=80:19.8:0.2;
[0045] (2) In the above product, add 0.2mol.L -1 EDTA sodium salt 10 ml;
[0046] (3) Weigh 2.1 g of sodium fluoride, add 70 ml of deionized water, and prepare an aqueous solution. At room temperature, under rapid stirring, the above solution was injected to form a precipitate, and the stirring reaction was continued for 1 hour;
[0047] (4) centrifugal separation and precipitation and washing with water three times, drying, and making a precursor;
[0048] (5) Putting the precursor into a high-temperature furnace and calcining at 400° C. for 5 hours to obtain a nano-scale up-conversion fluorescent material with an average particle size of 77 n...
PUM
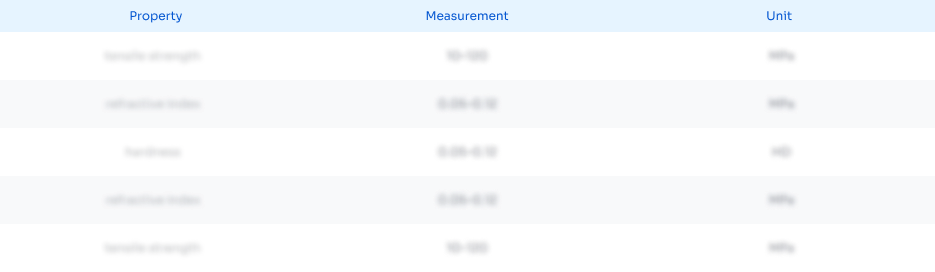
Abstract
Description
Claims
Application Information

- R&D
- Intellectual Property
- Life Sciences
- Materials
- Tech Scout
- Unparalleled Data Quality
- Higher Quality Content
- 60% Fewer Hallucinations
Browse by: Latest US Patents, China's latest patents, Technical Efficacy Thesaurus, Application Domain, Technology Topic, Popular Technical Reports.
© 2025 PatSnap. All rights reserved.Legal|Privacy policy|Modern Slavery Act Transparency Statement|Sitemap|About US| Contact US: help@patsnap.com