Heat-insulating light sandwich wall board
A light-weight wallboard and sandwich technology, applied in building components, sustainable waste treatment, solid waste management, etc., can solve problems such as increasing processes, reducing bending and compressive resistance, and affecting the strength of wallboards, so as to increase practicality area, reduce wet work, and save the total cost
- Summary
- Abstract
- Description
- Claims
- Application Information
AI Technical Summary
Problems solved by technology
Method used
Image
Examples
Embodiment Construction
[0009] 1. Specific formula
[0010] Shell: straw powder 50%, light mineral powder 35%, fly ash 2.9%, halogen powder 10%, glass fiber silk 1%, gelling agent 0.5%, flame retardant 0.5%, brightener 0.05%, curing agent 0.05%,
[0011] Inner core: polystyrene foam, thickness 80mm.
[0012] 2. Manufacturing method
[0013] Match the required raw material ingredients in proportion-uniformly stir-inject into the mold-level-spread glass fiber-inject the mixed raw material for the second time-second level-place the polystyrene with a length of 2600mm×250mm×80mm Two vinyl foam boards with a 10mm gap between them-the third injection of mixed raw materials-the second time of laying glass filaments-the fourth injection-leveling (the entire operation process is completed within 20 minutes) —— Curing—— Demoulding—— Natural curing, after drying, it can be used in the factory.
PUM
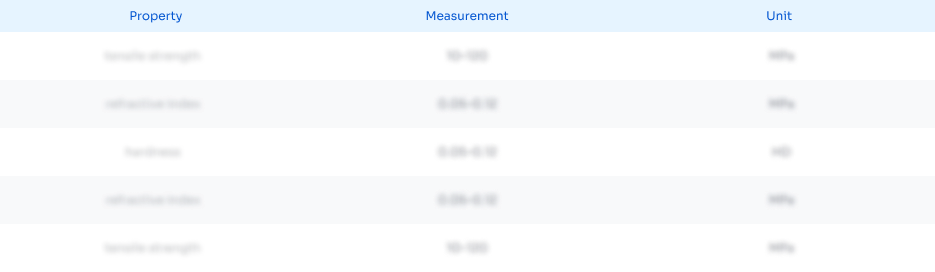
Abstract
Description
Claims
Application Information

- R&D
- Intellectual Property
- Life Sciences
- Materials
- Tech Scout
- Unparalleled Data Quality
- Higher Quality Content
- 60% Fewer Hallucinations
Browse by: Latest US Patents, China's latest patents, Technical Efficacy Thesaurus, Application Domain, Technology Topic, Popular Technical Reports.
© 2025 PatSnap. All rights reserved.Legal|Privacy policy|Modern Slavery Act Transparency Statement|Sitemap|About US| Contact US: help@patsnap.com