Hydrogenation catalyst for 2, 5-furandicarboxylic acid and reaction process
A technology of furandicarboxylic acid and tetrahydrofurandicarboxylic acid, which is applied in the field of 2,5-furandicarboxylic acid hydrogenation catalyst and its reaction process, can solve the problems of less research, achieve strong acid corrosion resistance, good stability, and simplify production The effect of process operations
- Summary
- Abstract
- Description
- Claims
- Application Information
AI Technical Summary
Problems solved by technology
Method used
Image
Examples
Embodiment 1
[0022] By dipping method, 0.65g RuCl 3 ·3H 2 O was added to 5 mL of aqueous solution, and 5 g of TiO was added 2 The carrier was mixed, then stirred at 25°C until it became a paste, left standing at room temperature for 24h to make the ruthenium salt evenly dispersed in the carrier, and then dried in an oven at 110°C for 12h. Final catalyst precursor at 500 °C H 2 Reduction in atmosphere for 4h, H 2 The flow rate was 40 mL / min.
[0023] Catalyst performance test: In a 75mL autoclave, add 0.2g of the 5% Ru / TiO prepared above 2 Catalyst, 1g FDCA, 20mL water, after the reactor is airtight, fill with 1MPa hydrogen to replace the residual air in the reactor, after repeating 6-8 times, fill the reactor with hydrogen, the reaction pressure is 2MPa, and the reaction temperature is 120°C , stirred at 700rpm, and reacted for 1h. After the reaction, the liquid-solid mixture was taken out for suction filtration separation, the obtained liquid was filtered with a 0.22um membrane, the...
Embodiment 2
[0025] By dipping method, 0.78g RuCl 3 ·3H 2 O was added to 10 mL aqueous solution, and 10 g SiO was added 2 The carrier was mixed, then stirred at 25°C until it became a paste, left at room temperature for 24h to make the ruthenium salt evenly dispersed in the carrier, and then dried in an oven at 100°C for 12h. Final catalyst precursor at 550 °C H 2 Reduction in atmosphere for 4h, H 2 The flow rate was 50 mL / min.
[0026] Catalyst performance test: In a 75mL autoclave, add 0.5g of the 3% Ru / SiO prepared above 2 Catalyst, 2g FDCA, 20mL tetrahydrofuran, after the reactor is sealed, fill with 1MPa hydrogen to replace the residual air in the reactor, after repeating 6-8 times, fill the reactor with hydrogen, the reaction pressure is 2MPa, and the reaction temperature is 100°C , stirred at 700rpm, and reacted for 2h. After the reaction, the liquid-solid mixture was taken out for suction filtration separation, the obtained liquid was filtered with a 0.22um membrane, the obta...
Embodiment 3
[0028] Using the impregnation method, 1.3 g RuCl 3 ·3H 2 O was added to 10 mL of aqueous solution, and 10 g of diatomaceous earth carrier was added to mix, then stirred at 50 °C until it became a paste, stood at room temperature for 24 h to make the ruthenium salt evenly dispersed in the carrier, and then dried in an oven at 110 °C Dry for 12h. Final catalyst precursor at 400 °C H 2 Reduction in atmosphere for 4h, H 2 The flow rate was 100 mL / min.
[0029] Catalyst performance test: In a 75mL autoclave, add 0.2g of the 5% ruthenium / diatomite catalyst prepared above, 2g of FDCA, and 20mL of methanol. After the reactor is sealed, fill it with 1MPa hydrogen to replace the residual air in the reactor. After repeating 6-8 times, the reaction kettle was filled with hydrogen, the reaction pressure was 3MPa, the reaction temperature was 120°C, and the reaction was carried out for 2h under stirring at a speed of 700rpm. After the reaction, the liquid-solid mixture was taken out fo...
PUM
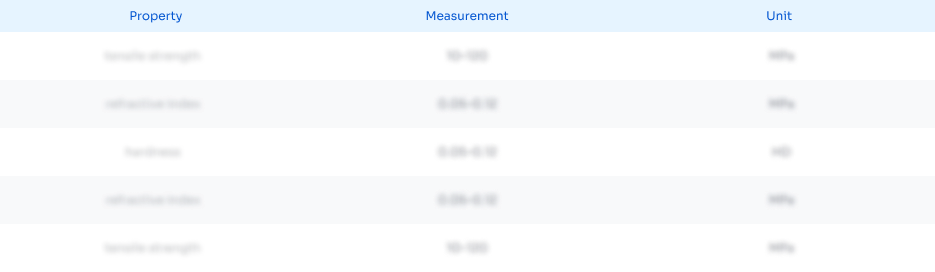
Abstract
Description
Claims
Application Information

- R&D
- Intellectual Property
- Life Sciences
- Materials
- Tech Scout
- Unparalleled Data Quality
- Higher Quality Content
- 60% Fewer Hallucinations
Browse by: Latest US Patents, China's latest patents, Technical Efficacy Thesaurus, Application Domain, Technology Topic, Popular Technical Reports.
© 2025 PatSnap. All rights reserved.Legal|Privacy policy|Modern Slavery Act Transparency Statement|Sitemap|About US| Contact US: help@patsnap.com