A processing method for corrosion-resistant metal shelves
A processing method and corrosion-resistant technology, applied in the direction of metal material coating technology, etc., can solve the problems of unsatisfactory product life, products responding to complex environments, and protective layer falling off, so as to reduce energy consumption and benefit the human body and the environment. Environmental protection and service life extension effect
- Summary
- Abstract
- Description
- Claims
- Application Information
AI Technical Summary
Problems solved by technology
Method used
Image
Examples
Embodiment 1
[0032] Ingredients: Weigh raw materials according to the composition and mass percentage of the above-mentioned corrosion-resistant metal shelves, including Tl: 5%, Be: 0.4%, C: 0.7%, Os: 0.8%, Pb: 2%, Sn: 3%, Ir : 0.6%, the balance is Fe and impurities, wherein the impurities include S<0.055%, O<0.015%.
[0033] Powder making: Put the raw material powder mixed in proportion into the jet mill, feed nitrogen, set the nitrogen pressure to 0.8MPa, and obtain alloy powder after continuous processing for 135 hours.
[0034] Compression molding: Fill the alloy powder into the mold of each part of the prefabricated shelf, fill it with nitrogen until the pressure in the mold reaches 3 atmospheres, and take out the blanks of each part after pressing for 4 hours.
[0035] Sintering: put the blank into the sintering furnace, first pre-sinter at 700°C for 1.5h, and carry out repressing treatment at the same time, then sinter the blank at 1100°C for 4h, then cool to room temperature, and f...
Embodiment 2
[0038] Ingredients: Weigh raw materials according to the composition and mass percentage of the above-mentioned corrosion-resistant metal shelves, including Tl: 4%, Be: 0.2%, C: 0.6%, Os: 0.6%, Pb: 1%, Sn: 2%, Ir : 0.4%, the balance is Fe and impurities, wherein the impurities include S<0.055%, O<0.015%.
[0039] Powder making: Put the raw material powder mixed in proportion into the jet mill, feed nitrogen, set the nitrogen pressure to 0.8MPa, and obtain alloy powder after continuous processing for 135 hours.
[0040] Compression molding: Fill the alloy powder into the mold of each part of the prefabricated shelf, fill it with nitrogen until the pressure in the mold reaches 3 atmospheres, and take out the blanks of each part after pressing for 4 hours.
[0041] Sintering: put the blank into the sintering furnace, first pre-sinter at 700°C for 1.5h, and carry out repressing treatment at the same time, then sinter the blank at 1100°C for 4h, then cool to room temperature, and fin...
Embodiment 3
[0044] Ingredients: Weigh raw materials according to the composition and mass percentage of the above-mentioned corrosion-resistant metal shelves, including Tl: 6%, Be: 0.6%, C: 0.8%, Os: 1%, Pb: 3%, Sn: 4%, Ir : 0.8%, the balance is Fe and impurities, wherein the impurities include S<0.055%, O<0.015%.
[0045] Powder making: Put the raw material powder mixed in proportion into the jet mill, feed nitrogen, set the nitrogen pressure to 0.8MPa, and obtain alloy powder after continuous processing for 135 hours.
[0046] Compression molding: Fill the alloy powder into the mold of each part of the prefabricated shelf, fill it with nitrogen until the pressure in the mold reaches 3 atmospheres, and take out the blanks of each part after pressing for 4 hours.
[0047] Sintering: put the blank into the sintering furnace, first pre-sinter at 700°C for 1.5h, and carry out repressing treatment at the same time, then sinter the blank at 1100°C for 4h, then cool to room temperature, and fin...
PUM
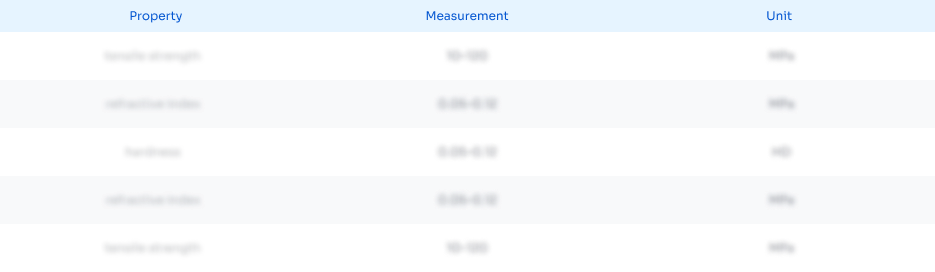
Abstract
Description
Claims
Application Information

- R&D
- Intellectual Property
- Life Sciences
- Materials
- Tech Scout
- Unparalleled Data Quality
- Higher Quality Content
- 60% Fewer Hallucinations
Browse by: Latest US Patents, China's latest patents, Technical Efficacy Thesaurus, Application Domain, Technology Topic, Popular Technical Reports.
© 2025 PatSnap. All rights reserved.Legal|Privacy policy|Modern Slavery Act Transparency Statement|Sitemap|About US| Contact US: help@patsnap.com