Silicon polishing composition, preparation method and application thereof
A technique for polishing compositions and substances, applied in polishing compositions containing abrasives, grinding/polishing equipment, machine tools for surface polishing, etc., can solve problems such as weakening adsorption and carrying effects, reducing mechanical effects, and decreasing polishing rates , to achieve the effect of prolonging the recycling performance, prolonging the storage time, and cleaning the polished surface
- Summary
- Abstract
- Description
- Claims
- Application Information
AI Technical Summary
Problems solved by technology
Method used
Image
Examples
Embodiment 1
[0056] (1) Preparation of composition intermediate products
[0057] 20g potassium hydroxide, 2g oxalic acid, 0.1g fatty alcohol polyoxyethylene ether, 1g propylene glycol, 0.025g 2-methyl-4-isothiazolin-3-one, 0.075g 2-methyl-5-chloro-4 - Dissolve isothiazolin-3-one in 200 g of deionized water, stir evenly, then add the solution to 166.7 g of 30wt% nano-silica colloid (average particle size 25 nm) while stirring, ultrasonically disperse for 15 min, and set aside for use .
[0058] (2) Preparation of polishing composition
[0059] Dissolve 4g of piperazine and 0.2g of 2-furancarboxylic acid in 100g of deionized water, stir evenly, then add the solution to the intermediate product of the composition after the above (1) treatment while stirring, and continue to add deionized water until dispersed. The total mass of the liquid was 2 kg, and the solution was encapsulated after magnetic stirring for 30 min. The pH value of the dispersion liquid was 10.
Embodiment 2
[0061] (1) Preparation of composition intermediate products
[0062] 60g ethylenediamine, 10g citric acid, 0.2g fatty alcohol polyoxyethylene ether, 2g propylene glycol, 0.25g 2-methyl-4-isothiazolin-3-one, 0.75g 2-methyl-5-chloro- 4-Isothiazolin-3-one was dissolved in 200 g of deionized water, stirred evenly, and then the solution was added to 250 g of 40 wt% nano-silica colloid (average particle size 40 nm) while stirring, and ultrasonically dispersed for 15 min. .
[0063] (2) Preparation of polishing composition
[0064] Dissolve 10g of 1-methylpiperazine and 1.5g of 2-tetrahydrofurancarboxylic acid in 150g of deionized water, stir evenly, then add the solution to the intermediate product of the composition after the above (1) treatment while stirring, and continue to add The total mass of the ionized water to the dispersion liquid is 2kg, and after magnetic stirring for 30min, the dispersion liquid is packaged, and the pH value of the dispersion liquid is 10.5.
Embodiment 3
[0066] (1) Preparation of composition intermediate products
[0067] 100g tetramethylammonium hydroxide, 20g citric acid, 2g isomeric alcohol polyoxyethylene ether, 8g propylene glycol, 0.3g 2-methyl-4-isothiazolin-3-one, 0.9g 2-methyl-5 -Chloro-4-isothiazolin-3-one was dissolved in 300g of deionized water, stirred evenly, then the solution was added to 750g of 40wt% nano-silica colloid (average particle size 40nm) while stirring, and ultrasonically dispersed for 15min, stand-by.
[0068] (2) Preparation of polishing composition
[0069] Dissolve 30g of 1-ethylpiperazine and 6g of 2-furanacetic acid in 200g of deionized water, stir evenly, add the solution to the intermediate product of the composition after the above (1) treatment while stirring, and continue to add deionized water. The total mass of the water to the dispersion liquid is 2kg, the magnetic stirring is carried out for 30min and then packaged, and the pH value of the dispersion liquid is 11.3.
PUM
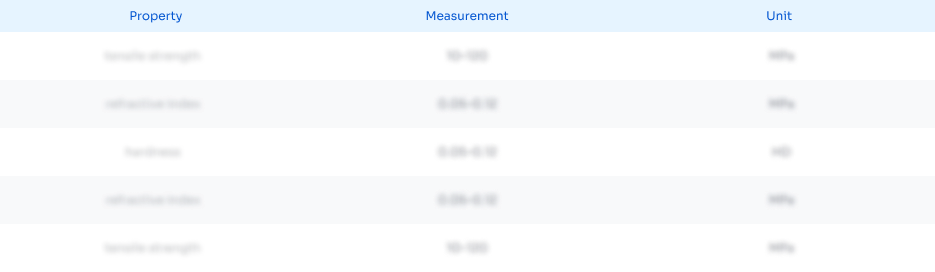
Abstract
Description
Claims
Application Information

- R&D Engineer
- R&D Manager
- IP Professional
- Industry Leading Data Capabilities
- Powerful AI technology
- Patent DNA Extraction
Browse by: Latest US Patents, China's latest patents, Technical Efficacy Thesaurus, Application Domain, Technology Topic, Popular Technical Reports.
© 2024 PatSnap. All rights reserved.Legal|Privacy policy|Modern Slavery Act Transparency Statement|Sitemap|About US| Contact US: help@patsnap.com