Method for preparing p-bromoanisole by oxidative bromination method
A technology of bromoanisole and oxidative bromination, applied in chemical instruments and methods, preparation of organic compounds, physical/chemical process catalysts, etc., can solve problems such as long reaction time, lengthy and complicated process, expensive precious metal palladium, etc. , to achieve high activity and selectivity, simple process flow and simple preparation process
- Summary
- Abstract
- Description
- Claims
- Application Information
AI Technical Summary
Problems solved by technology
Method used
Image
Examples
Embodiment example 1
[0016] Add 1.009g (12mmol) dicyandiamide to 20ml and dissolve 2.88g (1mmol) H 3 PW 12 O 40 .nH 2 60 ℃ hot water solution of O, add 1 g of activated carbon under constant stirring, stir vigorously at 60 ℃ for 5 h, after sufficient reaction, after the reaction mixture is cooled, the solvent is removed by rotary evaporation, and then the obtained solid sample is placed in a tubular Under the nitrogen atmosphere of the furnace, the calcination temperature was 350 °C, the heating rate was 5 °C / min, the temperature was maintained for 3 h, and the catalyst was naturally cooled to room temperature to obtain catalyst A1, wherein the content of PW was 45.9% (45.17%W, 0.73%P).
Embodiment example 2
[0018] Add 1.009g (12mmol) dicyandiamide to 20ml and dissolve 2.88g (1mmol) H 3 PW 12 O 40 .nH 2 60 ℃ hot water solution of O, add 1 g of activated carbon under constant stirring, stir vigorously at 60 ℃ for 5 h, after sufficient reaction, after the reaction mixture is cooled, the solvent is removed by rotary evaporation, and then the obtained solid sample is placed in a tubular Under the nitrogen atmosphere of the furnace, the calcination temperature was 450°C, the heating rate was 5°C / min, the temperature was maintained for 3 hours, and the catalyst was naturally cooled to room temperature to obtain catalyst A2, wherein the content of PW was 46.26% (45.53%W, 0.73%P).
Embodiment example 3
[0020] Add 1.009g (12mmol) dicyandiamide to 20ml and dissolve 2.88g (1mmol) H 3 PW 12 O 40 .nH 2 60 ℃ hot water solution of O, add 1 g of activated carbon under constant stirring, stir vigorously at 60 ℃ for 5 h, after sufficient reaction, after the reaction mixture is cooled, the solvent is removed by rotary evaporation, and then the obtained solid sample is placed in a tubular Under the nitrogen atmosphere of the furnace, the calcination temperature was 550°C, the heating rate was 5°C / min, the temperature was maintained for 3h, and then cooled to room temperature naturally to obtain catalyst A3, wherein the content of PW was 46.5% (45.76%W, 0.74%P).
PUM
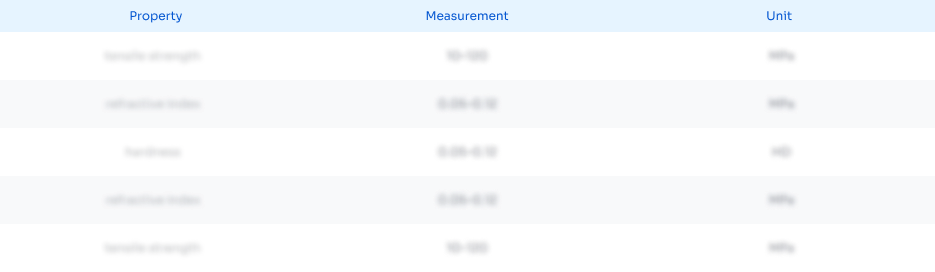
Abstract
Description
Claims
Application Information

- Generate Ideas
- Intellectual Property
- Life Sciences
- Materials
- Tech Scout
- Unparalleled Data Quality
- Higher Quality Content
- 60% Fewer Hallucinations
Browse by: Latest US Patents, China's latest patents, Technical Efficacy Thesaurus, Application Domain, Technology Topic, Popular Technical Reports.
© 2025 PatSnap. All rights reserved.Legal|Privacy policy|Modern Slavery Act Transparency Statement|Sitemap|About US| Contact US: help@patsnap.com