Diversion type low-flow-resistance heat pipe heat exchanger
A heat pipe heat exchanger, low flow resistance technology, applied in indirect heat exchangers, heat exchanger shells, heat exchange equipment, etc. Increased corrosion and other issues
- Summary
- Abstract
- Description
- Claims
- Application Information
AI Technical Summary
Problems solved by technology
Method used
Image
Examples
Embodiment Construction
[0024] Reference attached Figure 1 attach Figure 2 attach Figure 3 attach Figure 4 A diversion type low-flow resistance heat pipe heat exchanger shown comprises a heat exchanger box 1, a diversion type low-flow resistance heat pipe 2, a hot end fluid channel 3, a hot end 4, a tube plate 5, a cold end 6, a cold end fluid channel 7, a hot end diversion fin 8. When specifically implemented, the heat pipe hot end 4 is processed into an oval shape, and then the diversion fin 8 symmetrically welded to the hot end 4, in accordance with the requirements of the heat pipe production technology to produce a complete diversion type low flow resistance heat pipe 2, so far, including the hot end 4 and cold end 6 of the diversion type low flow resistance heat pipe is completed, and then the diversion type low flow resistance heat pipe 2 is assembled into the tube plate 5 composed of a heat exchanger bundle assembly according to the designed pipe arrangement, and this assembly is hoisted to the h...
PUM
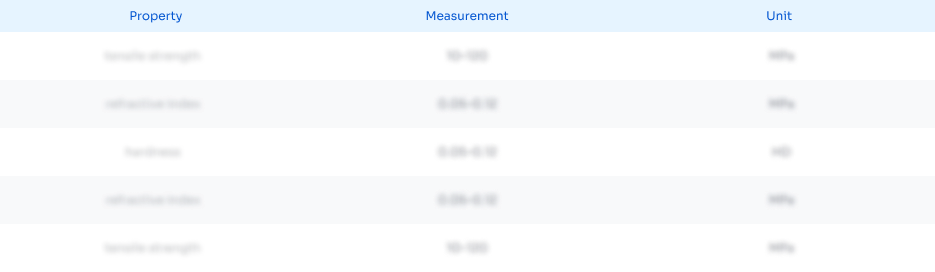
Abstract
Description
Claims
Application Information

- R&D
- Intellectual Property
- Life Sciences
- Materials
- Tech Scout
- Unparalleled Data Quality
- Higher Quality Content
- 60% Fewer Hallucinations
Browse by: Latest US Patents, China's latest patents, Technical Efficacy Thesaurus, Application Domain, Technology Topic, Popular Technical Reports.
© 2025 PatSnap. All rights reserved.Legal|Privacy policy|Modern Slavery Act Transparency Statement|Sitemap|About US| Contact US: help@patsnap.com