Laser additive manufacturing isotropic scanning method for scanning galvanometer
A laser additive and isotropic technology, applied in the field of additive manufacturing, can solve problems such as anisotropy of tissue properties, and achieve the effects of reducing residual stress, reducing cumulative effect, and increasing the existence time of molten pool
- Summary
- Abstract
- Description
- Claims
- Application Information
AI Technical Summary
Problems solved by technology
Method used
Image
Examples
Embodiment 1
[0020] A laser additive manufacturing isotropic scanning method for scanning galvanometers is adopted, which includes the following steps:
[0021] (1) Set the size of the processing surface to be 100×100mm, and the size of each small area to be 4×4mm;
[0022] (2) A small area is evenly filled with a sine curve as the scanning path. The amplitude of the sine function curve is 1mm, the period is 2π, and the initial phase angle is 0°. Two adjacent sinusoids are equally spaced, with a distance of 0.03mm; a straight line is uniformly filled as the remelting path, and two adjacent lines are equally spaced, with a distance of 0.03mm. The remelting path is perpendicular to the axis of the scanning path along the period direction;
[0023] (3) Carry out laser scanning filling and synchronous remelting along the scanning path and remelting path planned in step (2), the laser power is 600W, and the scanning speed is 500mm / s; Melting, the two remelting paths are perpendicular to each ...
Embodiment 2
[0025] The invention is used to repair the cavitation part of the steam turbine blade, and the mild cavitation area of the blade is polished and the surface oil stains are removed with acetone.
[0026] Perform penetrant testing on the area to be repaired to confirm that the cavitation area is completely removed.
[0027] A Co-based alloy powder is selected as the repair material, and its composition is as follows:
[0028]
[0029] The area of the blade to be repaired is a curved surface, and a 6% sodium silicate solution is used as the binder. After mixing with the alloy powder at a weight ratio of 1:5 to a paste, smear it on the area to be repaired and compact it, and then add a 0.2mm feeler gauge. Spread it on both sides of the powder, use a spatula to smooth the powder, and let it sit for 5 minutes to wait for the adhesive to dry.
[0030] Adjust the focal length of the galvanometer laser additive manufacturing system, divide the area to be repaired into several 5...
PUM
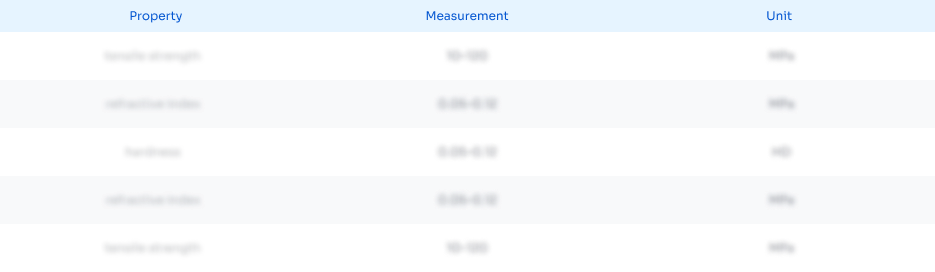
Abstract
Description
Claims
Application Information

- R&D Engineer
- R&D Manager
- IP Professional
- Industry Leading Data Capabilities
- Powerful AI technology
- Patent DNA Extraction
Browse by: Latest US Patents, China's latest patents, Technical Efficacy Thesaurus, Application Domain, Technology Topic, Popular Technical Reports.
© 2024 PatSnap. All rights reserved.Legal|Privacy policy|Modern Slavery Act Transparency Statement|Sitemap|About US| Contact US: help@patsnap.com