High-strength wear-resistant composite fender and processing technology thereof
A processing technology and fender technology, applied in transportation and packaging, ink, coating, etc., can solve the problems of limited service life, insufficient wear resistance, high price, etc., and achieve strong waterproof and anti-fouling ability, wear resistance Good, high-intensity effect
- Summary
- Abstract
- Description
- Claims
- Application Information
AI Technical Summary
Problems solved by technology
Method used
Image
Examples
Embodiment 1
[0047] A processing technology for a high-strength wear-resistant composite fender, comprising the following steps:
[0048] S1: Heat 100 parts of caprolactam to 110°C for heating and melting, vacuumize to remove water until there are no bubbles, add 3 parts of modified cellulose nanocrystals, and vacuum to remove water until there are no bubbles, then add tetrahydrofuran of ethylmagnesium bromide Mixed liquid 1mol / L, heat up to 150°C and continue vacuuming to remove water until there are no bubbles, add bisacylated lactam-1,6-hexamethylenediamine 2mol / kg to react for 25min, then quickly cast into Dry and polymerize at a constant temperature in a mold for 1 hour, and cool to obtain anionic polymerized nylon 6;
[0049] The preparation of modified cellulose nanocrystals comprises the following steps:
[0050] (1) 6.2mmol cellulose nanocrystals were evacuated at 100°C for 48h, under the protection of nitrogen, cellulose nanocrystals, 18.6mmol triethylamine, 18.6mmol toluene dii...
Embodiment 2
[0059] A processing technology for a high-strength wear-resistant composite fender, comprising the following steps:
[0060] S1: Heat 100 parts of caprolactam to 113°C for heating and melting, vacuumize to remove water until there are no bubbles, add 3 parts of modified cellulose nanocrystals, and vacuum to remove water until there are no bubbles, then add tetrahydrofuran of ethylmagnesium bromide Mixed liquid 1mol / L, heat up to 153°C and continue vacuuming to remove water until there are no bubbles, add bisacylated lactam-1,6-hexamethylenediamine 2mol / kg to react for 25min, then quickly cast into Dry and polymerize at a constant temperature in a mold for 1 hour, and cool to obtain anionic polymerized nylon 6;
[0061] The preparation of modified cellulose nanocrystals comprises the following steps:
[0062] (1) 6.2mmol cellulose nanocrystals were evacuated at 102°C for 48h. Under nitrogen protection, cellulose nanocrystals, 18.6mmol triethylamine, 18.6mmol toluene diisocyana...
Embodiment 3
[0071] A processing technology for a high-strength wear-resistant composite fender, comprising the following steps:
[0072] S1: Heat 100 parts of caprolactam to 115°C for heating and melting, vacuumize to remove water until there are no bubbles, add 3 parts of modified cellulose nanocrystals, and vacuum to remove water until there are no bubbles, then add tetrahydrofuran of ethylmagnesium bromide Mixed liquid 1mol / L, heat up to 155°C and continue vacuuming to remove water until there are no bubbles, add bisacylated lactam-1,6-hexamethylenediamine 2mol / kg to react for 25min, then quickly cast into Dry and polymerize at a constant temperature in a mold for 1 hour, and cool to obtain anionic polymerized nylon 6;
[0073]The preparation of modified cellulose nanocrystals comprises the following steps:
[0074] (1) 6.2mmol cellulose nanocrystals were evacuated at 105°C for 48h, under the protection of nitrogen, cellulose nanocrystals, 18.6mmol triethylamine, 18.6mmol toluene diis...
PUM
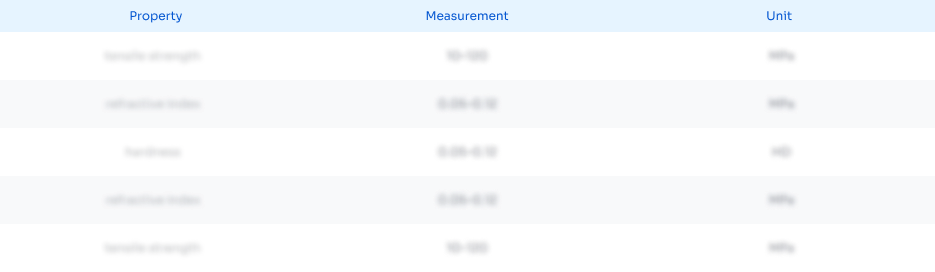
Abstract
Description
Claims
Application Information

- R&D
- Intellectual Property
- Life Sciences
- Materials
- Tech Scout
- Unparalleled Data Quality
- Higher Quality Content
- 60% Fewer Hallucinations
Browse by: Latest US Patents, China's latest patents, Technical Efficacy Thesaurus, Application Domain, Technology Topic, Popular Technical Reports.
© 2025 PatSnap. All rights reserved.Legal|Privacy policy|Modern Slavery Act Transparency Statement|Sitemap|About US| Contact US: help@patsnap.com