Manufacturing process of high-performance nano-material ceramic thin-film device
A technology of nano-materials and ceramic films, applied in the field of nano-ceramic materials, can solve the problems of easy brittle cracking, poor film toughness, etc.
- Summary
- Abstract
- Description
- Claims
- Application Information
AI Technical Summary
Problems solved by technology
Method used
Image
Examples
Embodiment 1
[0035] Preparation of hydrogen-containing POSS:
[0036] A1. Mix 100mL isopropanol, 0.12mol phenyltrimethoxysilane, 2mg deionized water and 0.1mol flake sodium hydroxide, stir well, heat the reaction system to 73°C with an oil bath, and reflux under nitrogen atmosphere After reacting for 5 hours, then stirring and reacting at room temperature for 48 hours, the obtained mixed solution was subjected to rotary evaporation to remove isopropanol, and vacuum dried at 60°C for 18 hours to obtain octaphenyl polysilsesquioxane sodium salt;
[0037]A2. Add 0.1mol octaphenyl polysilsesquioxane sodium salt into a three-necked flask, under nitrogen protection, add 150mL anhydrous tetrahydrofuran, stir well, add 0.21mol triethylamine, react in ice bath at 0°C for 1h, use Slowly add 70 mL of tetrahydrofuran solution containing 0.25 mol of methyldichlorosilane into the constant pressure funnel dropwise at a rate of 2 drops / second, react for 6 hours, then raise the temperature to room temperat...
Embodiment 2
[0039] Functional additives are made by:
[0040] S1. Add 1 mol of carborane and 100 mL of anhydrous tetrahydrofuran into the three-necked flask, blow in nitrogen to drive away the air in the three-necked flask, and add 2.1 mol of n-butyllithium dropwise with a constant pressure dropping funnel at 0°C in a nitrogen atmosphere. Hexane solution, ensure that the temperature of the reaction system remains at 0±1°C during the dropping process, and the dropping rate is 1 drop / second. After the dropping is complete, slowly warm up to room temperature, continue to stir for 2 hours, and then add 80mL of 2.1mol benzyl Trimethylammonium hydroxide methanol solution, stirred at -0.07MPa, 40°C for 30min to remove residual water and methanol in the system, and then dropwise added 2.1mol 1,3-bis(3-amino Anhydrous tetrahydrofuran solution of propyl)-1,1,3,3-tetramethyldisiloxane, the dropping rate is 1 drop / second, after the drop is complete, slowly raise the temperature and reflux for 12 hour...
Embodiment 3
[0044] Functional additives are made by:
[0045] S1. Add 1 mol of carborane and 100 mL of anhydrous tetrahydrofuran into the three-necked flask, blow in nitrogen to drive away the air in the three-necked flask, and add 2.3 mol of n-butyllithium dropwise with a constant pressure dropping funnel at 0°C in a nitrogen atmosphere. Hexane solution, ensure that the temperature of the reaction system remains at 0±1°C during the dropping process, and the dropping rate is 1 drop / second. After the dropping is complete, slowly warm up to room temperature, continue to stir for 2 hours, and then add 2.3mol benzyl Trimethylammonium hydroxide methanol solution, stirred at -0.07MPa, 40°C for 30min, remove residual water and methanol in the system, then add 90mL solution containing 2.3mol 1,3-bis(3- Aminopropyl)-1,1,3,3-tetramethyldisiloxane in anhydrous tetrahydrofuran solution, the dropping rate is 2 drops / second, after the drop is complete, slowly heat up and reflux for 12 hours, after the ...
PUM
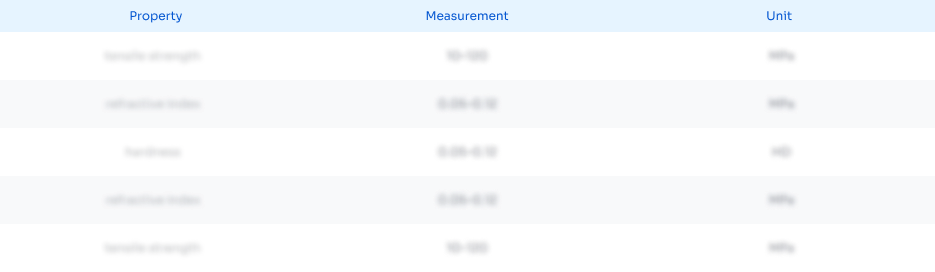
Abstract
Description
Claims
Application Information

- Generate Ideas
- Intellectual Property
- Life Sciences
- Materials
- Tech Scout
- Unparalleled Data Quality
- Higher Quality Content
- 60% Fewer Hallucinations
Browse by: Latest US Patents, China's latest patents, Technical Efficacy Thesaurus, Application Domain, Technology Topic, Popular Technical Reports.
© 2025 PatSnap. All rights reserved.Legal|Privacy policy|Modern Slavery Act Transparency Statement|Sitemap|About US| Contact US: help@patsnap.com