Application of thermosetting polyimide in preparation of high-temperature-resistant resin-based composite material
A high-temperature-resistant resin and polyimide technology, which is applied in the field of preparing high-temperature-resistant resin-based composite materials and thermosetting polyimide, can solve the problems of reducing the mechanical properties of materials and high porosity of composite products, and achieve good application scenarios, The effect of high solubility and high heat resistance
- Summary
- Abstract
- Description
- Claims
- Application Information
AI Technical Summary
Problems solved by technology
Method used
Image
Examples
preparation example Construction
[0035] In some more specific embodiments, the preparation method of described thermosetting polyimide comprises:
[0036] S1. Under a protective atmosphere, react the mixed reaction system comprising fluorene dianhydride monomer, aromatic diamine monomer and organic solvent at 80-100°C for 6-8 hours;
[0037] S2. Add an end-capping agent to the mixed reaction system described in step S1, and continue the reaction for 2 to 4 hours;
[0038] S3. The temperature of the reaction mixture obtained in step S2 is raised to 170-190° C. and the reaction is continued for 4-6 hours to obtain a polyimide resin.
[0039] In some more specific embodiments, the fluorene dianhydride monomer has a structure as shown in formula (II):
[0040]
[0041] In some more specific embodiments, the aromatic diamine monomers include 2,2'-bis(trifluoromethyl)-4,4'-diaminobiphenyl, 4,4'-diaminobiphenyl Ether, 3,4'-diaminodiphenyl ether, 1,3-bis(3-aminophenoxy)benzene, 1,3-bis(4-aminophenoxy)benzene, 4,...
Embodiment 1
[0062] Under the protection of nitrogen, add 3.931g of 4,4'-diaminodiphenyl ether, 6.000g of fluorene dianhydride monomer and 20g of m-cresol into a 100ml reaction flask, react at 90°C for 6h, and then add 3.249g 4-PEPA, while adding 10g of m-cresol to adjust the solid content of the solution to 30wt%, and continue the reaction for 3h; then under the protection of nitrogen, the reaction system was heated to 185°C for 5h, and the reaction system was cooled to room temperature and then poured into ethanol , filtered, washed, and dried at 250° C. for 2 h to obtain the polyimide shown in formula (i).
[0063]
[0064] Performance characterization: the dissolved solid content of the polyimide prepared in this embodiment can reach 30% in polar aprotic solvent, its 13 CNMR spectrum such as figure 1 As shown, the FT-IR spectrum is shown as figure 2 As shown, the rheological curve is shown as image 3 As shown, the cured product DMA curve of polyimide is as follows Figure 4 As...
Embodiment 2
[0066] Under the protection of nitrogen, 5.210g of 2,2'-bismethyl-4,4'-diaminobiphenyl, 5.000g of fluorene dianhydride monomer and 40g of m-cresol were added to a 100ml reaction flask, at 100 ℃ for 8 hours, then add 6.769g of 4-PEPA, and at the same time add 10g m-cresol to adjust the solid content of the solution to 25wt%, and continue the reaction for 2 hours; then, under the protection of nitrogen, the reaction system is heated to 190 ℃ for 6 hours, and the reaction system After cooling to room temperature, pour it into ethanol, filter, wash, and dry at 260° C. for 3 hours to obtain the polyimide shown in formula (ii).
[0067] The polyimide prepared in this example has a dissolved solid content of up to 30% in a polar aprotic solvent, a minimum melt viscosity of 31Pa·s, a cured product glass transition temperature of 451°C, and a thermal weight loss of 5% in air The temperature is 556°C.
[0068]
PUM
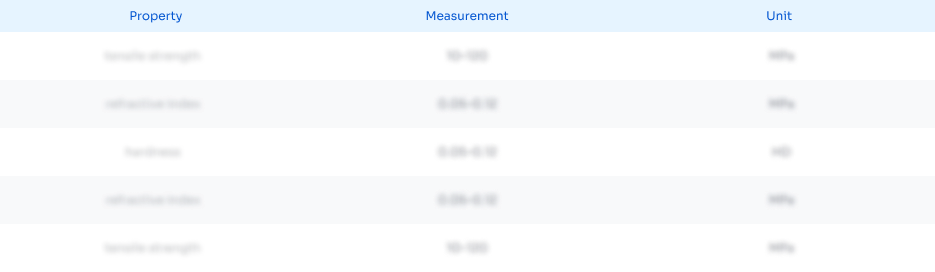
Abstract
Description
Claims
Application Information

- Generate Ideas
- Intellectual Property
- Life Sciences
- Materials
- Tech Scout
- Unparalleled Data Quality
- Higher Quality Content
- 60% Fewer Hallucinations
Browse by: Latest US Patents, China's latest patents, Technical Efficacy Thesaurus, Application Domain, Technology Topic, Popular Technical Reports.
© 2025 PatSnap. All rights reserved.Legal|Privacy policy|Modern Slavery Act Transparency Statement|Sitemap|About US| Contact US: help@patsnap.com