Flux for silicon carbide ceramic connection and preparation method thereof
A technology of silicon carbide ceramics and flux, which is applied in the field of aerospace materials, can solve problems such as poor connection performance and achieve good connection effects
- Summary
- Abstract
- Description
- Claims
- Application Information
AI Technical Summary
Problems solved by technology
Method used
Image
Examples
Embodiment 1
[0028] Mix 32.55kg Si powder, 2.45kg Ti powder, 2kg Zr powder, 12.3kgB powder, 1.1kg Fe powder, 6.5kg Cu powder, 2.5kg Hf powder in an agate mortar and grind them evenly, then place them in a graphite crucible for sintering , the sintering condition is 1400°C / 2h, after the sintering is completed, place it in a planetary ball mill for fine grinding and sieving, and then the flux product can be obtained.
Embodiment 2
[0030] Mix 36.55kg of Si powder, 2.5kg of Ti powder, 2.5kg of Zr powder, 12.5kg of B powder, 1.5kg of Fe powder, 8.5kg of Cu powder, and 1.5kg of Hf powder in an agate mortar and grind them evenly, then place them in a graphite crucible for sintering. The condition is 1400°C / 2h. After the sintering is completed, place it in a planetary ball mill for fine grinding and sieving, and then the flux product can be obtained.
Embodiment 3
[0032] Mix 40kg Si powder, 2.7kg Ti powder, 3.5kg Zr powder, 14.2kgB powder, 1.5kg Fe powder, 9.5kg Cu powder, 1.7kg Hf powder in an agate mortar and grind them evenly, then place them in a graphite crucible for sintering , the sintering condition is 1400°C / 2h, after the sintering is completed, place it in a planetary ball mill for fine grinding and sieving, and then the flux product can be obtained.
[0033] The flux that embodiment 1-3 makes is respectively used in the welding between pottery and pottery, and welding mode is brazing, and welding method comprises the following steps:
[0034] ①Pretreatment: Ceramic-10*10*3mm cut sample, 20*10*3mm stretched sample, polished with a brown brush (sequentially polished with water-based sandpaper with a roughness of 300-2000 mesh, each Grinding with roughness sandpaper for 30min)→silicon carbide coating (that is, coating a silicon carbide coating on the surface of the ceramic shear sample, coating the silicon carbide coating on t...
PUM
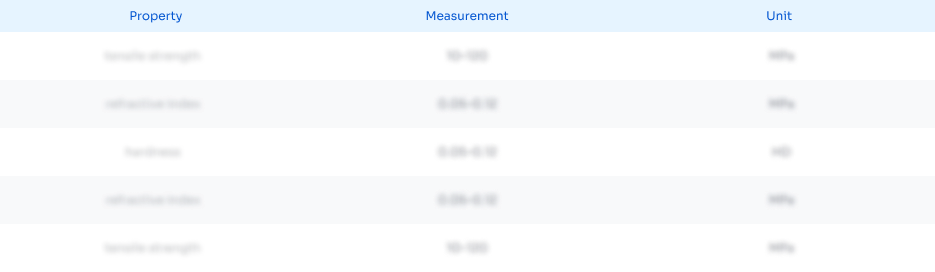
Abstract
Description
Claims
Application Information

- R&D Engineer
- R&D Manager
- IP Professional
- Industry Leading Data Capabilities
- Powerful AI technology
- Patent DNA Extraction
Browse by: Latest US Patents, China's latest patents, Technical Efficacy Thesaurus, Application Domain, Technology Topic, Popular Technical Reports.
© 2024 PatSnap. All rights reserved.Legal|Privacy policy|Modern Slavery Act Transparency Statement|Sitemap|About US| Contact US: help@patsnap.com