Method for controlling vacuum treatment carbon-oxygen reaction of aluminum-free bearing steel
A vacuum treatment, aluminum bearing technology, applied in the field of metallurgy, can solve the problems of stop production, continuous casting machine breaking, and oxygen content exceeding the process requirements, so as to maintain the balance of carbon-oxygen reaction, increase stability, and reduce accidental production accidents Effect
- Summary
- Abstract
- Description
- Claims
- Application Information
AI Technical Summary
Problems solved by technology
Method used
Examples
Embodiment 1
[0032] (1) After the scrap steel and desulfurized hot metal are decarburized, dephosphorized, carbon-preserved and heated up in the primary smelting furnace, the steel is tapped, the target carbon content is controlled at 0.16%, and the oxygen content of the tapped steel is 180ppm;
[0033] (2) The ladle is washed, and the steel type produced in the early stage of the ladle is a hard line steel type that is not high oxygen, low aluminum, and low titanium;
[0034] (3) The basicity of the slag in the early stage of refining is 1.8, the silicon element composition of the alloy is controlled to 0.30%, and the oxygen content of the molten steel before vacuum treatment is 14ppm;
[0035] (4) Adopt the vacuum tank in the early stage, and the number of online times is the 8th;
[0036] (5) Vacuum treatment time is 28 minutes; soft blowing to continuous casting after breaking the air;
[0037] For the bearing steel produced by this method, 17 furnaces were produced in the entire pour...
Embodiment 2
[0039] 1) The scrap steel and desulfurized hot metal are decarburized, dephosphorized, carbon-preserved and heated up in the primary smelting furnace, and then the steel is tapped. The target carbon content is controlled at 0.18%, and the oxygen content of the tapped steel is 160ppm;
[0040] (2) The ladle is washed, and the steel type produced in the early stage of the ladle is a hard line steel type that is not high oxygen, low aluminum, and low titanium;
[0041] (3) The basicity of the slag in the early stage of refining is 1.9, the silicon element composition of the alloy is controlled to 0.31%, and the oxygen content of the molten steel before vacuum treatment is 14ppm;
[0042] (4) Adopt the vacuum tank in the early stage, and the number of online times is the 23rd;
[0043] (5) Vacuum treatment time is 30 minutes; soft blowing to continuous casting after air breaking.
[0044] For the bearing steel produced by this method, 15 furnaces were produced in the entire pouri...
PUM
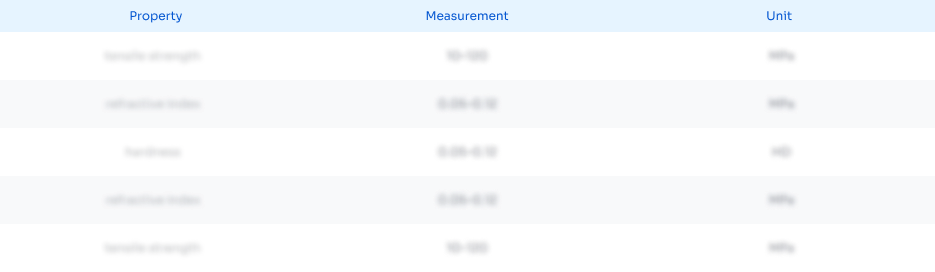
Abstract
Description
Claims
Application Information

- R&D Engineer
- R&D Manager
- IP Professional
- Industry Leading Data Capabilities
- Powerful AI technology
- Patent DNA Extraction
Browse by: Latest US Patents, China's latest patents, Technical Efficacy Thesaurus, Application Domain, Technology Topic, Popular Technical Reports.
© 2024 PatSnap. All rights reserved.Legal|Privacy policy|Modern Slavery Act Transparency Statement|Sitemap|About US| Contact US: help@patsnap.com