Preparation method of modified silicon dioxide-epoxy resin composite slurry
A technology of epoxy resin and silica, applied in the direction of epoxy resin glue, adhesive type, adhesive additive, etc., can solve the problem of high viscosity of composite slurry, achieve good sphericity, good dispersion, crosslinking high density effect
- Summary
- Abstract
- Description
- Claims
- Application Information
AI Technical Summary
Problems solved by technology
Method used
Examples
Embodiment 1
[0025] A. Preparation of modified silica
[0026] Weigh 30g of ammonia water with a concentration of 28wt%, 1000g of ethanol, and 200g of deionized water into a 3L kettle, start stirring, and add 80g of tetraethyl orthosilicate and 0.2g of methyltrimethoxysilane at a constant speed at a stirring speed of 150rpm , the dropping time is 20 minutes, after the dropwise addition is completed, the temperature is raised to 40°C, and the constant temperature is reacted for 3 hours; the temperature is continued to be raised to 60°C, and 50g of bis(3-triethoxysilylpropane) containing 2.5g is added dropwise to the reaction system base) amine and 2.5g of N,N-bis(3-trimethoxysilylpropyl)urea ethanol solution, reacted for 2.5 hours to obtain in-situ modified silica solution, and the modified silica solution was sequentially used Centrifuge in a centrifuge, wash with ethanol / water solvent, repeat the cycle 3 times, and then bake in a drying oven at 120°C for 11 hours to obtain in-situ modifie...
Embodiment 2
[0032] A. Preparation of modified silica
[0033]Weigh 15g of tetramethylammonium hydroxide with a concentration of 25wt%, add 1000g of ethanol, and 200g of deionized water into a 3L kettle, start stirring, and add 80g of tetraethyl orthosilicate and 0.2g of formazan at a constant speed at a stirring speed of 150rpm. Trimethoxysilane, the dropping time is 20 minutes. After the dropping is completed, the temperature is raised to 40°C, and the constant temperature reaction is carried out for 3 hours; the temperature is continued to be raised to 60°C, and 50g silylpropyl)amine and 2.5g of N,N-bis(3-trimethoxysilylpropyl)urea ethanol solution, reacted for 2.5 hours to obtain in-situ modified silica solution, the modified di The silicon oxide solution was centrifuged in a centrifuge, washed with ethanol / water solvent, repeated 3 times, and then baked in a drying oven at 120°C for 11 hours to obtain in-situ modified silicon dioxide powder;
[0034] B. Preparation of modified silica...
Embodiment 3
[0039] A. Preparation of modified silica
[0040] Weigh 30g of tetramethylammonium hydroxide with a concentration of 25wt%, add 1000g of ethanol and 200g of deionized water into a 3L kettle, start stirring, and add 80g of tetraethyl orthosilicate and 0.2g of formazan at a constant speed at a stirring speed of 150rpm. Trimethoxysilane, the dropping time is 20 minutes. After the dropping is completed, the temperature is raised to 40°C, and the temperature is reacted for 3 hours; the temperature is continued to rise to 60°C, and 50g of bis(triethoxysilane base) ethylene and 2.5g of N,N-bis(3-trimethoxysilylpropyl)urea ethanol solution, reacted for 2.5 hours to obtain the in-situ modified silica solution, and the modified silica solution was sequentially used Centrifuge in a centrifuge, wash with ethanol / water solvent, repeat the cycle 3 times, and then bake in a drying oven at 120°C for 12 hours to obtain in-situ modified silica powder;
[0041] B. Preparation of modified silica...
PUM
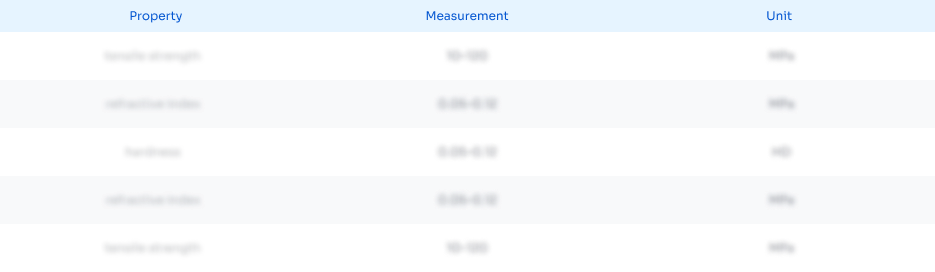
Abstract
Description
Claims
Application Information

- R&D Engineer
- R&D Manager
- IP Professional
- Industry Leading Data Capabilities
- Powerful AI technology
- Patent DNA Extraction
Browse by: Latest US Patents, China's latest patents, Technical Efficacy Thesaurus, Application Domain, Technology Topic, Popular Technical Reports.
© 2024 PatSnap. All rights reserved.Legal|Privacy policy|Modern Slavery Act Transparency Statement|Sitemap|About US| Contact US: help@patsnap.com