Preparation method of compound polyethylene glycol electrolyte particles
A polyethylene glycol and electrolyte technology, applied in the field of medicine, can solve problems such as uncontrollable quality of compound polyethylene glycol electrolyte preparations, packaging and adsorption of electrolyte inorganic salts, and difficulty in mixing uniformly, so as to achieve controllable product quality and reduce component variation , The effect of simple production process
- Summary
- Abstract
- Description
- Claims
- Application Information
AI Technical Summary
Problems solved by technology
Method used
Image
Examples
Embodiment 1
[0047] Example 1 Spray drying to prepare compound polyethylene glycol electrolyte particles:
[0048] Compound polyethylene glycol electrolyte granule formulation (prepared with 6.9kg of total material per batch) is shown in Table 1:
[0049] Table 1 Formula of compound polyethylene glycol electrolyte particles
[0050]
[0051] Preparation method: Weigh each component of the prescription amount in Table 1, crush 1.29 parts of sodium bicarbonate, 2.53 parts of sodium chloride, and 0.33 parts of potassium chloride and sieve it, and control the particle size to pass through the No. 7 sieve 30%~100%, then mix evenly with 40 parts of polyethylene glycol 3350, heat and melt the material at 65°C, stir and mix, then spray dry, adjust the spray drying air volume to 60%, and the air inlet temperature to 30°C , the atomization pressure was 1.5 bar, and the feed rate was 100%, to obtain polyethylene glycol particles wrapped with electrolyte inorganic salts. Mix the prepared polyethy...
Embodiment 2
[0058] Example 2 Preparation of compound polyethylene glycol electrolyte particles by spray drying:
[0059] Preparation method: Weigh each component of the prescription amount in Table 1, crush 1.29 parts of sodium bicarbonate, 2.53 parts of sodium chloride, and 0.33 parts of potassium chloride and sieve it, and control the particle size to pass through the No. 7 sieve 30%~100%, mix evenly with 95 parts of polyethylene glycol 3350, heat and melt the material at 70°C, stir and mix, then spray dry, adjust the spray drying air volume to 100%, and the air temperature to -20°C , the atomization pressure was 5 bar, and the feed rate was 100%, to obtain polyethylene glycol particles wrapped with electrolyte inorganic salts. Mix the prepared polyethylene glycol granules wrapped with electrolyte inorganic salts with sweetener and flavor evenly to obtain compound polyethylene glycol electrolyte granules (prescription 2). Perform Na on prescription 2 + 、K + Content detection, measure...
Embodiment 1
[0066] Comparative Example 1 Direct Mixing Process Prepares Compound Polyethylene Glycol Electrolyte Particles
[0067] Prepare compound polyethylene glycol electrolyte particles by direct mixing process: weigh 95 parts by weight of polyethylene glycol 3350, 1.29 parts of sodium bicarbonate, 2.53 parts of sodium chloride, and 0.33 parts of potassium chloride. Potassium chloride and sodium bicarbonate particle size is No. 7 sieve pass rate 30%~100%, take 1 part of polyethylene glycol 3350 and 1.29 parts of sodium bicarbonate, 2.53 parts of sodium chloride, 0.33 parts of potassium chloride, and mix for 10 minutes Add 46.5 parts of polyethylene glycol 3350 and mix for 10 minutes; finally add 47.5 parts of polyethylene glycol 3350, 0.07 parts of sweetener and 0.72 parts of essence, and mix for 30 minutes to obtain compound polyethylene glycol electrolyte particles (prescription 3). Perform Na on prescription 3 + 、K + Content detection, measure twice, content detection result is ...
PUM
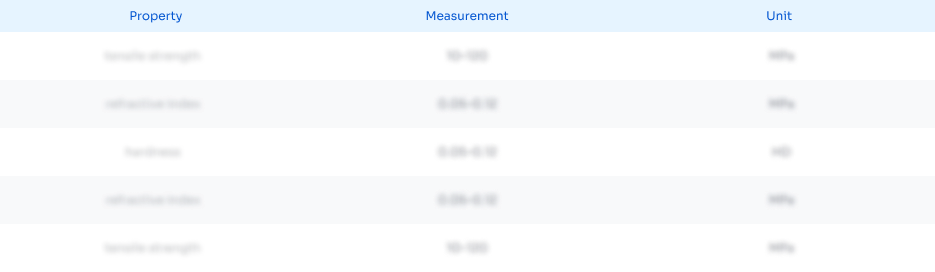
Abstract
Description
Claims
Application Information

- Generate Ideas
- Intellectual Property
- Life Sciences
- Materials
- Tech Scout
- Unparalleled Data Quality
- Higher Quality Content
- 60% Fewer Hallucinations
Browse by: Latest US Patents, China's latest patents, Technical Efficacy Thesaurus, Application Domain, Technology Topic, Popular Technical Reports.
© 2025 PatSnap. All rights reserved.Legal|Privacy policy|Modern Slavery Act Transparency Statement|Sitemap|About US| Contact US: help@patsnap.com