Smelting method of low-density stainless steel
A smelting method and stainless steel technology, which is applied in the field of low-density stainless steel smelting, can solve problems such as insufficient aluminum content in finished products, difficulty in homogenizing molten steel and aluminum alloy, and falsely high aluminum content, so as to improve uniformity and stability and promote agitation and mixing, to ensure the stability of the effect
- Summary
- Abstract
- Description
- Claims
- Application Information
AI Technical Summary
Problems solved by technology
Method used
Examples
Embodiment 1
[0021] Smeming method of low density stainless steel, the specific steps are as follows:
[0022] (1) Adjust 65T iron water into the converter, blow oxygen removal;
[0023] (2) The transformer oxidation period, add 25T high carbon-iron manganese, add 5T high carbon chrome;
[0024] (3) Restoration of the converter, add 1.2T high silicon manganese, 0.2T silicon iron, 0.35T aluminum block composite oxygen, resulting in decarbon-removal steel; reduction, the mass fraction of each component in the slag is: CAO: 50.58% SiO 2 : 5.33%, MGO: 5.96%, Al 2 O 3 : 25.62%, CAF 2 : 9.68%, MnO: 0.59%, Cr 2 O 3 : 0.43%, FeO: 0.32%; in which (CaO + MgO) / (SIO 2 + Al 2 O 3 ) = 1.83; FeO + MnO + Cr 2 O 3 = 1.34;
[0025] (4) Melting the 13T aluminum block using a medium frequency furnace to form a molten aluminum liquid, first into argon protection into the steel bag, then molten aluminum liquid in the steel bag, and then subsequently redeemed the decarburized steel water obtained by step (3), At t...
Embodiment 2
[0029] Smeming method of low density stainless steel, the specific steps are as follows:
[0030] (1) Adjust 65T iron water into the converter, blow oxygen removal;
[0031] (2) In the oxidation period of the converter, 21.6T high carbon manganese iron was added, and 6.5T high carbon chrome was added;
[0032] (3) The converter is reduced, and 1.5T high silicon manganese, 0.4T silicon iron, 0.31T aluminum block composite oxygen, resulting in decarbon-carbon steel; reduction, the mass fraction of each component in the slag is: CAO: 52.36% SiO 2 : 4.95%, MGO: 5.42%, Al 2 O 3 : 26.37%, CAF 2 : 9.06%, MnO: 0.45%, Cr 2 O 3 : 0.41%, FeO: 0.25%; (CaO + MgO) / (SIO 2 + Al 2 O 3 ) = 1.84; FeO + MnO + Cr 2 O 3 = 1.11;
[0033] (4) Use a medium frequency furnace to melt 12.4T aluminum block to form a molten aluminum liquid, first into argon protection into the packet, followed by ceping the molten aluminum solution into the packet, and then subsequently remove the decarbon-water water obtain...
Embodiment 3
[0036] Smeming method of low density stainless steel, the specific steps are as follows:
[0037] (1) Adjust 65T iron water into the converter, blow oxygen removal;
[0038] (2) The transformer oxidation period, 27T high carbon manganese iron was added, and 7.3T high carbon chromium was added;
[0039] (3) The reducing period of the converter, add 1.35T high silicon manganese, 0.33T silicon, 0.41T aluminum block composite oxygen, resulting in decarbon-removal steel; reduction, the mass fraction of each component in the slag is: CAO: 49.65% SiO 2 : 5.86%, MGO: 5.21%, Al 2 O 3 : 27.32%, CAF 2 : 9.15%, MnO: 0.32%, Cr 2 O 3: 0.4%, FeO: 0.33%; (CaO + MgO) / (SIO 2 + Al 2 O 3 ) = 1.65; FeO + MnO + Cr 2 O 3 = 1.05.
[0040] (4) Melting 11.3T aluminum block using a medium frequency furnace to form a molten aluminum liquid, first into argon protection in the steel bag, and then molten aluminum liquid into the packet, and then subsequently redeemed into the steel bag At the same time, the 2...
PUM
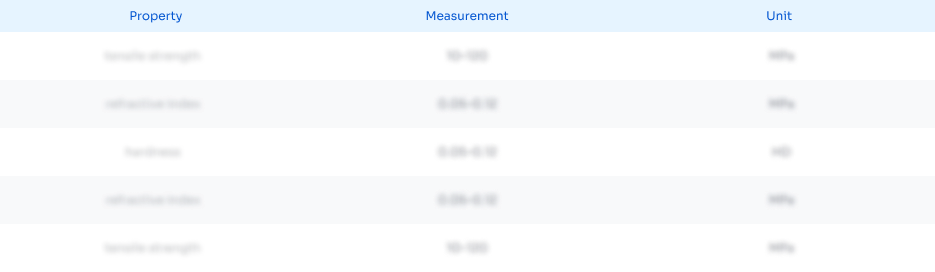
Abstract
Description
Claims
Application Information

- R&D
- Intellectual Property
- Life Sciences
- Materials
- Tech Scout
- Unparalleled Data Quality
- Higher Quality Content
- 60% Fewer Hallucinations
Browse by: Latest US Patents, China's latest patents, Technical Efficacy Thesaurus, Application Domain, Technology Topic, Popular Technical Reports.
© 2025 PatSnap. All rights reserved.Legal|Privacy policy|Modern Slavery Act Transparency Statement|Sitemap|About US| Contact US: help@patsnap.com