Production technology of graphene fiber board
A technology of graphene fiber and production process, which is applied in the direction of manufacturing tools, wood processing appliances, and pretreatment of molding materials, etc., which can solve the problems that ordinary fiberboards are prone to mildew, limit the application field of fiberboards, and cannot be used in temperature and humidity environments. To achieve the effect of solving the defects of mechanical properties and dimensional stability, enhancing the anti-corrosion effect, improving strength and toughness
- Summary
- Abstract
- Description
- Claims
- Application Information
AI Technical Summary
Problems solved by technology
Method used
Image
Examples
Embodiment 1
[0054] Embodiment 1, the present embodiment provides a kind of production technology of graphene fiberboard, comprising:
[0055] 1) Log peeling and slicing;
[0056] 2) cleaning the wood chips to remove impurities in the wood chips so that the sand content of the cleaned wood chips is no more than 0.03%;
[0057] 3) Put the cleaned wood chips into the wood chip cooking device, and soften them by pressure cooking. The cooking time is 4 minutes, and the cooking temperature is 180°C;
[0058] 4) heat-grinding the softened wood chips to obtain wood chip fibers;
[0059]5) Put the dried wood chip fiber into the sizing device to apply viscose, which includes graphene-based additives, and the graphene-based additives include: composite graphene, chlorinated polyethylene and titanate coupling agent, according to parts by weight, the composite graphene is 80 parts, the chlorinated polyethylene is 5 parts, and the titanate coupling agent is 0.5 parts, and the composite graphene is co...
Embodiment 2
[0068] Embodiment 2, the present embodiment provides a kind of production technology of graphene fiberboard, comprising:
[0069] 1) Log peeling and slicing;
[0070] 2) cleaning the wood chips to remove impurities in the wood chips so that the sand content of the cleaned wood chips is no more than 0.05%;
[0071] 3) Put the cleaned wood chips into the wood chip cooking device, and soften them by pressure cooking. The cooking time is 6 minutes, and the cooking temperature is 190°C;
[0072] 4) heat-grinding the softened wood chips to obtain wood chip fibers;
[0073] 5) Put the dried wood chip fiber into the sizing device to apply viscose, which includes graphene-based additives, and the graphene-based additives include: composite graphene, chlorinated polyethylene and titanate coupling agent, according to parts by weight, the composite graphene is 120 parts, the chlorinated polyethylene is 25 parts, and the titanate coupling agent is 6 parts, and the composite graphene is c...
Embodiment 3
[0082] Embodiment 3, the present embodiment provides a kind of production technology of graphene fiberboard, comprising:
[0083] 1) Log peeling and slicing;
[0084] 2) cleaning the wood chips to remove impurities in the wood chips so that the sand content of the cleaned wood chips is no more than 0.04%;
[0085] 3) Put the cleaned wood chips into the wood chip cooking device, and soften them by pressure cooking. The cooking time is 5 minutes, and the cooking temperature is 185°C;
[0086] 4) heat-grinding the softened wood chips to obtain wood chip fibers;
[0087] 5) Put the dried wood chip fiber into the sizing device to apply viscose, which includes graphene-based additives, and the graphene-based additives include: composite graphene, chlorinated polyethylene and titanate coupling agent, according to parts by weight, the composite graphene is 100 parts, the chlorinated polyethylene is 10 parts, and the titanate coupling agent is 3 parts, and the composite graphene is c...
PUM
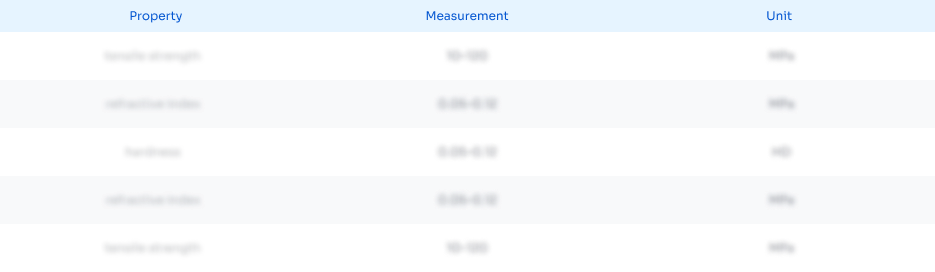
Abstract
Description
Claims
Application Information

- R&D
- Intellectual Property
- Life Sciences
- Materials
- Tech Scout
- Unparalleled Data Quality
- Higher Quality Content
- 60% Fewer Hallucinations
Browse by: Latest US Patents, China's latest patents, Technical Efficacy Thesaurus, Application Domain, Technology Topic, Popular Technical Reports.
© 2025 PatSnap. All rights reserved.Legal|Privacy policy|Modern Slavery Act Transparency Statement|Sitemap|About US| Contact US: help@patsnap.com